Electrospun Scaffolding for Regenerative Medicine
In order to properly regenerate cells and tissues that have been damaged or lost due to a disease or age, the scientific community has employed electrospun samples thanks to their ability to biomimic the extracellular matrix (ECM) native structure. The most common properties of electrospun scaffolds are a high surface area, controllable fiber diameter and pore size, the ability to process thermolabile components, use of natural and synthetic material to create biomimetic structures, and ease of post-sample processing to desired needs. All these features allow fibrous scaffolding sample preparation for tissue regeneration, wound-healing platforms, delivery of living cells into scaffolds to then be used in vivo.
The use of water-soluble polymeric fibers not only allow the scaffold to mimic the ECM environment, but it also gives the sample bioadhesive properties. When the proper bioactive is added to the fiber structure of this bioadhesive, drug release over time can be achieved to regenerate an affected area. However, if the unidirectional release is desired, a second hydrophobic layer can be implemented. When a polymer is carefully selected and their chemical properties are exploited, post-thermal treatment of hydrophobic and hydrophilic layers can be implemented to physically adhere the hydrophilic bioadhesive scaffold onto a second substrate. By doing this, the drug penetration into the targeted area is enhanced and drug loss into the hydrophobic side is avoided. An example of this process for regenerative medicine, and created with the Fluidnatek® equipment, includes the Rivelin® patches.
Rivelin® Patches: Mouth Wound Case Study
The SEM images below show the microstructure of Rivelin® patches. Image ‘a’ shows the surface morphology of the hydrophilic fibers having a drug on its structure. While these specific fibers are in the range of less than 5 µm, the Fluidnatek® equipment can create fibers and particles having diameters ranging from 20 nm to 100 µm, which will all depend on the solution to be used and the processing parameters. Interestingly, by using the roll-to-roll capacity in the Fluidnatek® electrospinning equipment, a layer of a second product can be spun on top of the first one. When thermal treatment is used, one can selectively sinter one polymer to join both layers together (image ‘b’), allowing to maintain desired hydrophilic and hydrophobic properties in the same sample and desired location. Image ‘c’ shows the final product after electrospinning and post-treating the dual layer. The final Rivelin® patch is applied to a patient to treat the affected mucosa area inside the mouth (image ‘d’).
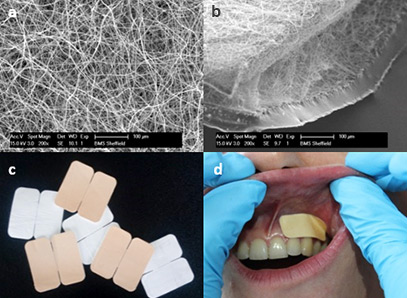
The use of electrospun scaffolding material for tissue engineering and regenerative medicine has become more popular, especially in the industry production. Typical home built units are not able to achieve production rates needed for commercialization and client demand. The Fluidnatek® technology offers a complete package when high throughput for pilot-scale and industrial fabrication are needed. From roll-to-roll ability, usage of up to 96 emitters at a time, up to 4,000 mL of solution, fiber/particle production in a semi-continuous way, ability of the equipment to be certified by current good manufacturing processes (cGMP) and ISO-13485 for medical devices, and employment of a climate control environmental unit to obtain reproducible fiber production by maintaining and conditioning the spinning conditions, makes the Fluidnatek® electrospinning equipment an ideal choice for pharmacological applications where high production are needed.