Fractography is a method in failure analysis for studying the fracture surface of materials. Studying the characteristics of the fractured surface can help to determine the cause of failure in an engineered product. Different modes of failure produce characteristic features on the surface, allowing a forensic analysis to determine the root cause of the failure.
Scanning electron microscopy allows examination of fractured surfaces with incredible detail. The Phenom XL desktop SEM provides magnification up to 150,000x, revealing the tiny features that point to a specific failure mode. Some causes of crack growth include fatigue, stress corrosion cracking, and hydrogen embrittlement.
Many fractographic features can be identified using SEM, including fatigue striations, intergranular cracking, microvoid coalescence, transgranular cleavage, and secondary cracking. Some of those features are highlighted in the following case study of a fractured bolt.
Scanning Electron Microscopes in Fractography
The scanning electron microscope (SEM) is a critical tool in fractographic studies. SEM has much better resolution and depth of field than optical microscopes, which are key to revealing the topographical features of fracture surfaces.
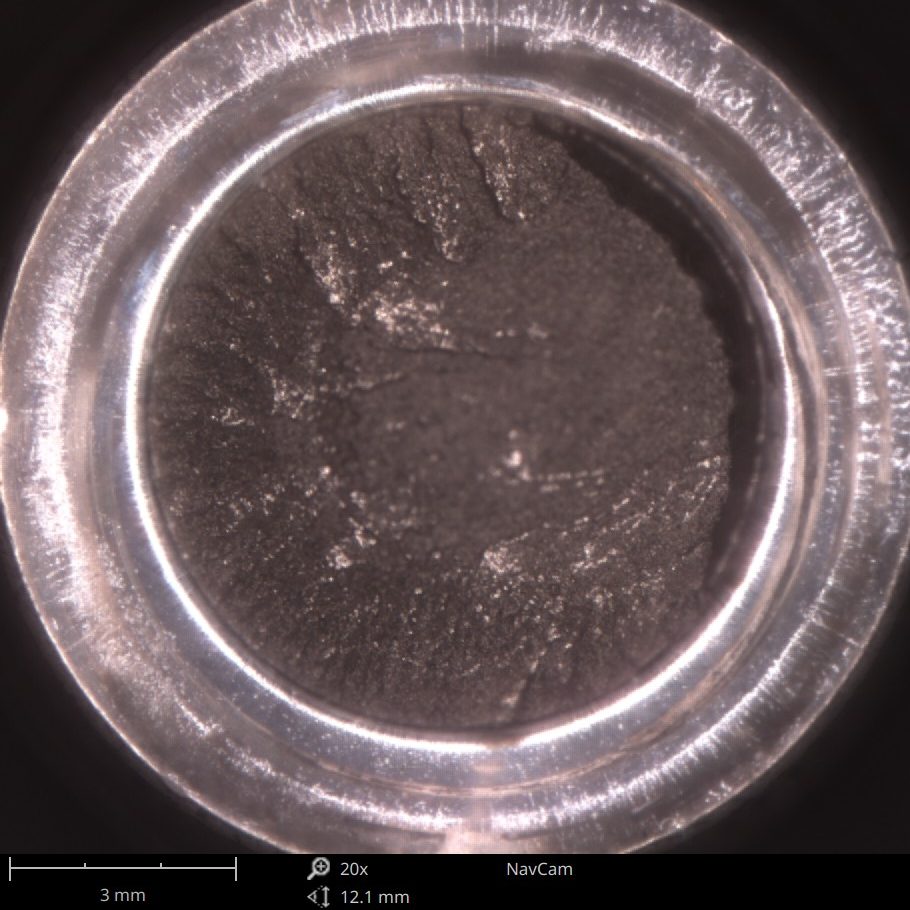
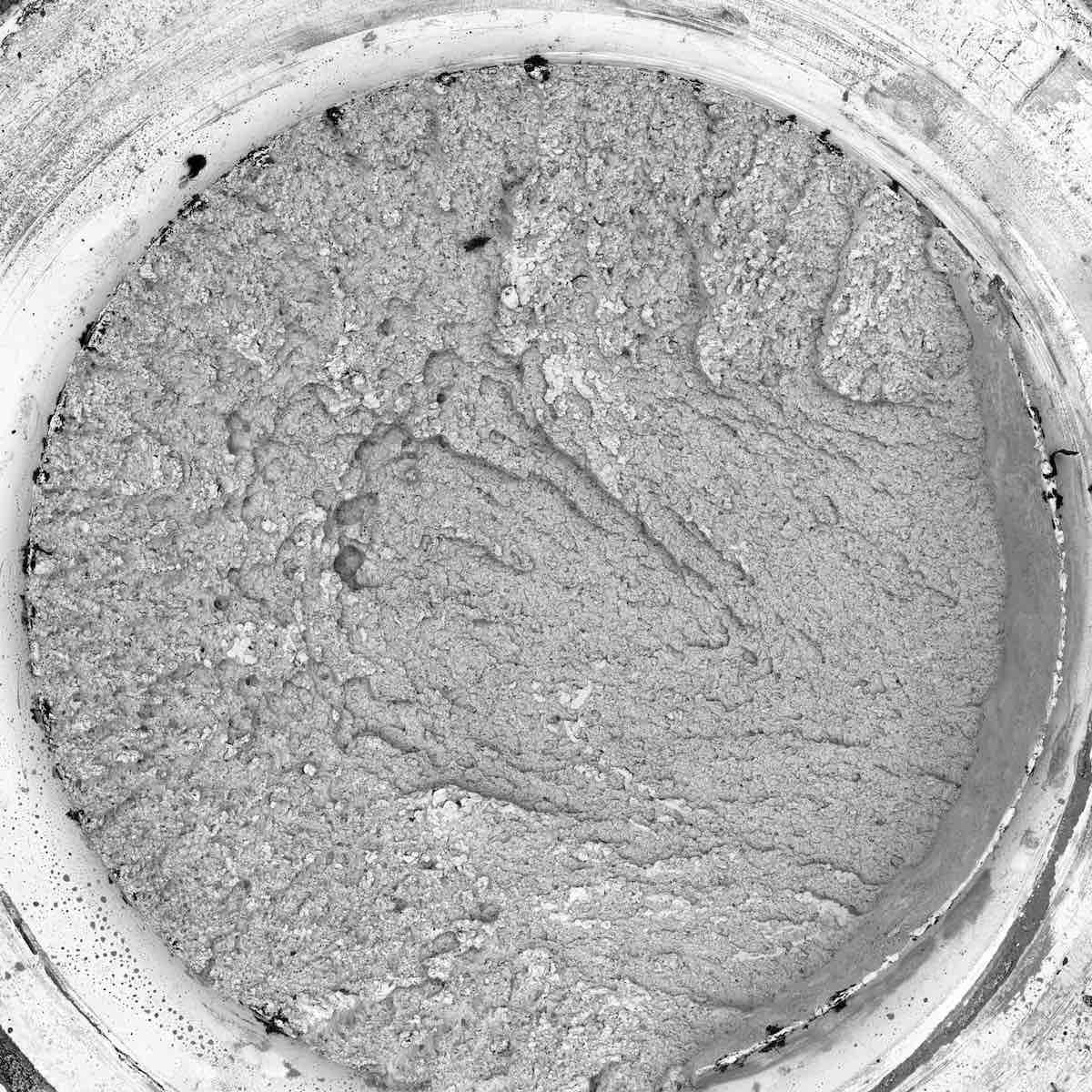
Revealing the Mode of Fracture via SEM
Specific modes of failure impart characteristic features on the fracture surface. This section will show some examples of the small-scale features that can be found using SEM.
Microvoid Coalescence
In ductile fracture, the separation of material at the fracture surface creates microvoids. These voids grow during plastic flow of the material and eventually coalesce into larger voids. In the final stages of the failure, these voids separate at the fracture surface and undergo significant necking, which leads to a characteristic dimpled texture. Round dimples are said to be equiaxed microvoids – the separation occurred normally to the fracture plane. If there are shear stresses involved, the coalesced microvoids will be elongated in the direction of shear.
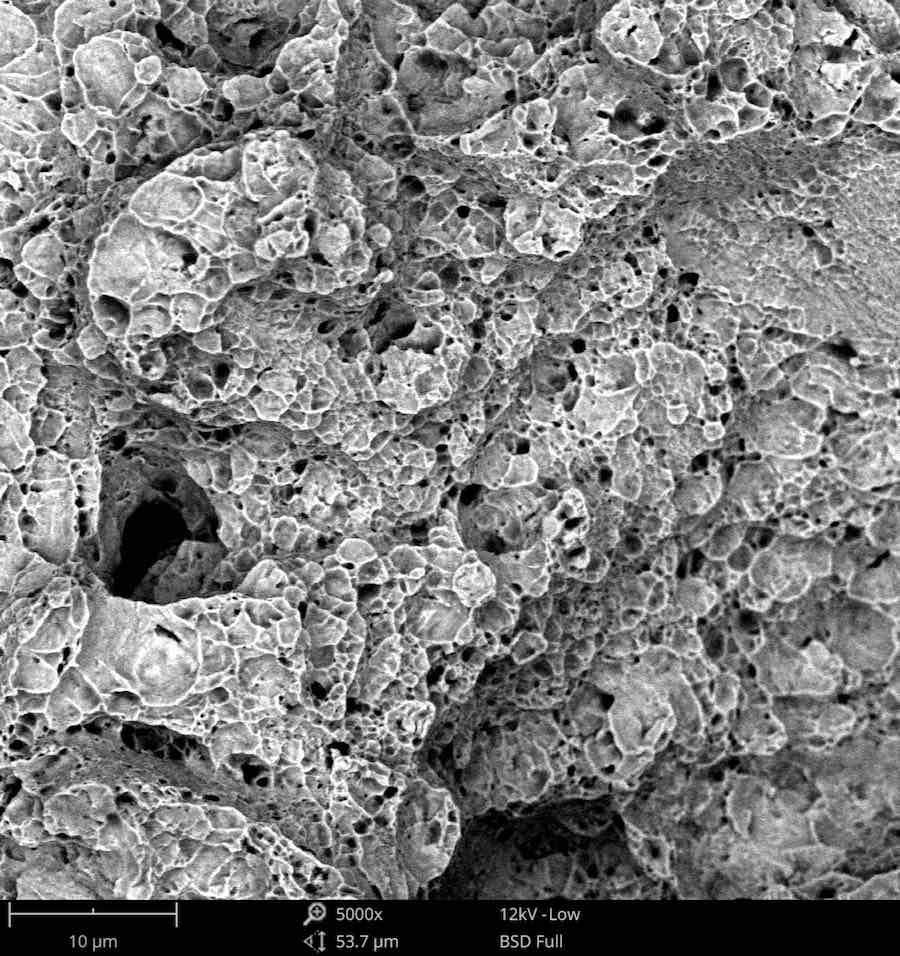
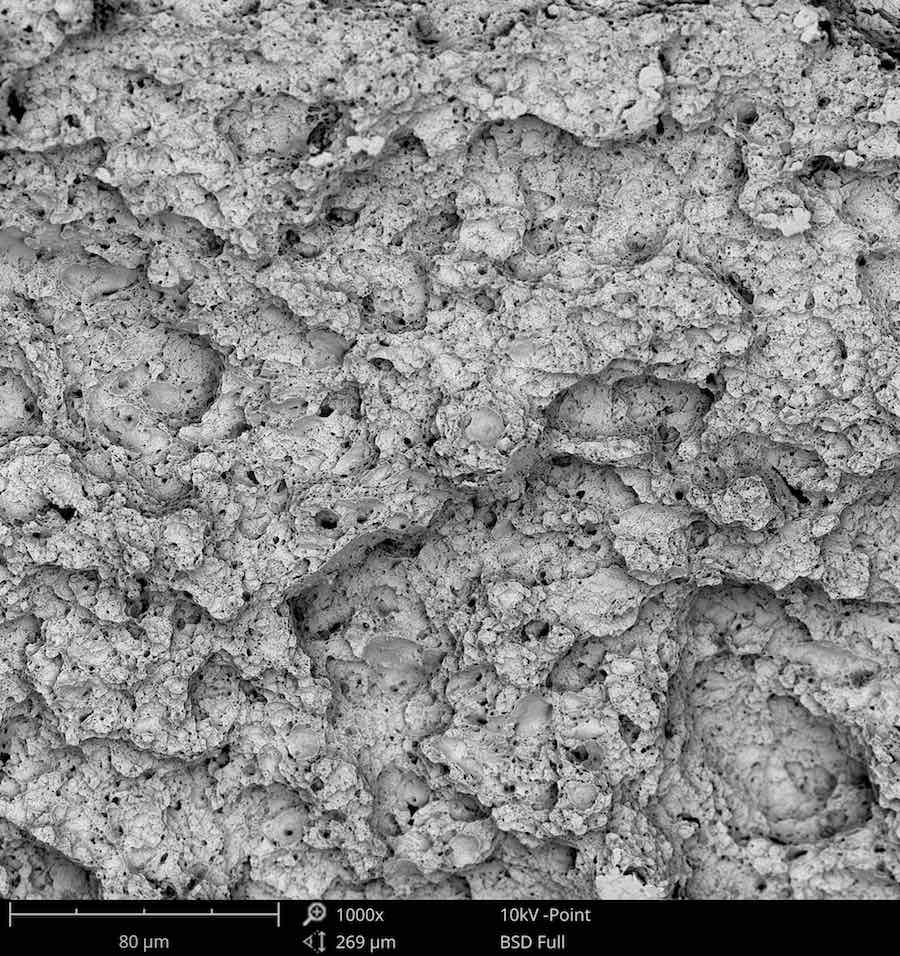
Intergranular and Transgranular Cleavage
In brittle fracture of metals, the fracture plane must either separate the individual metal grains or go around them. These failure modes are called transgranular and intergranular cleavage, respectively. Intergranular cleavage is a lower energy process since the energy required to separate grains along the grain boundary is lower than the energy required to separate the atoms within a crystal.
Intergranular cleavage is sometimes called “rock candy fracture” because of the appearance of the exposed metal grains.
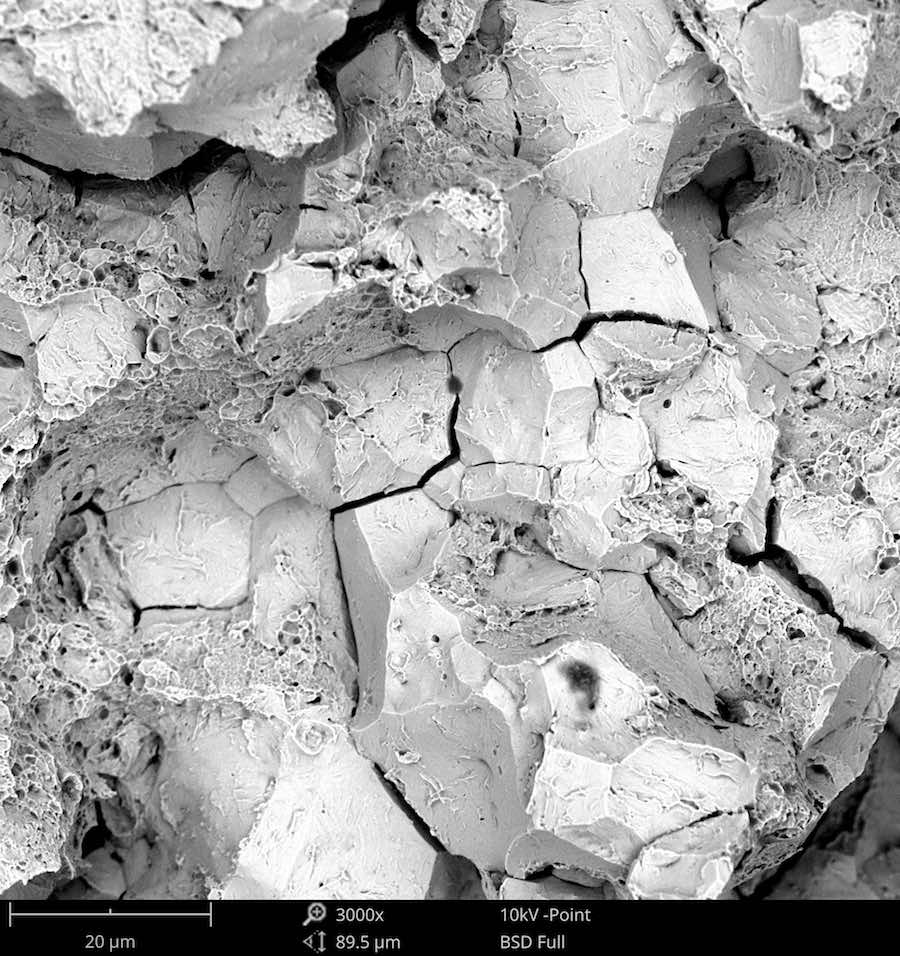
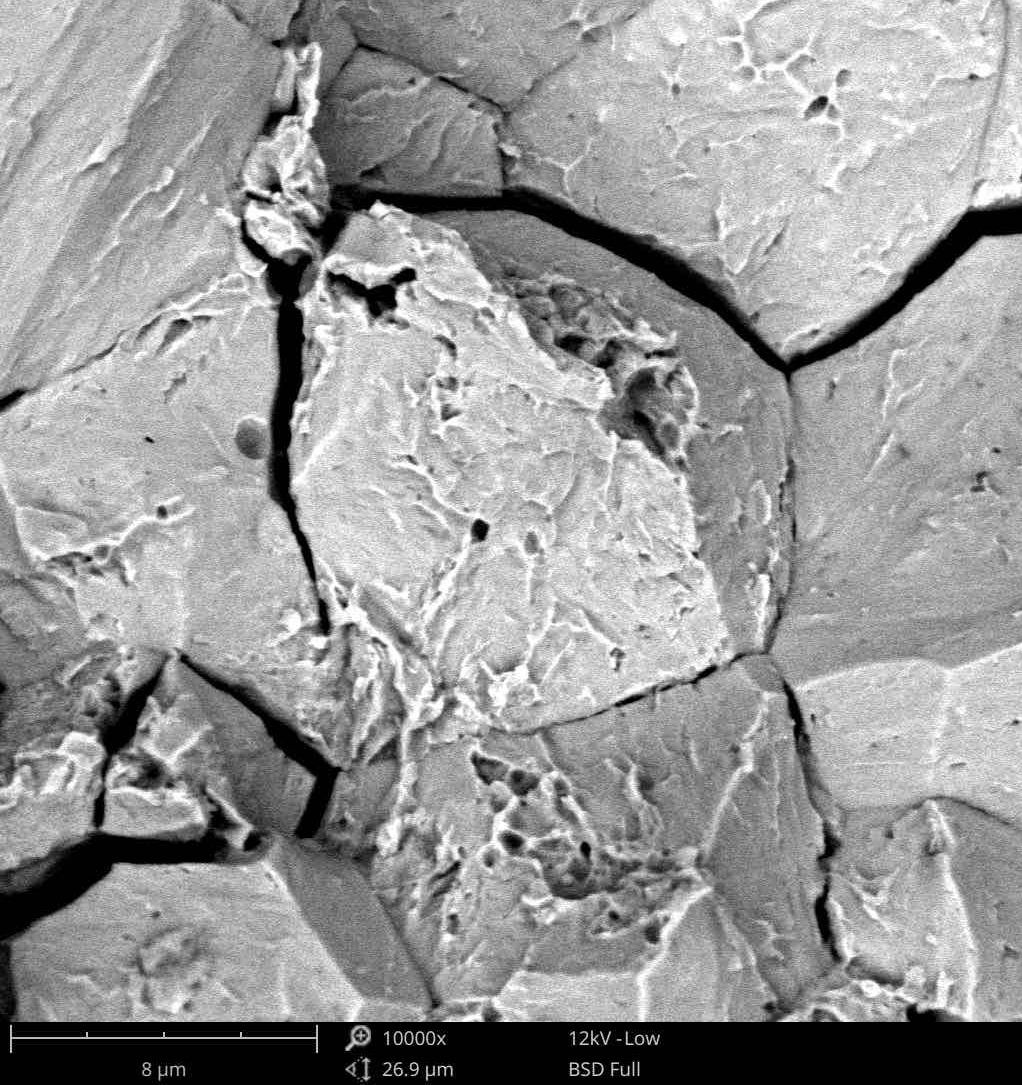