Introduction
Powders are one of the most common forms of materials that are analyzed using scanning electron microscopy (SEM). The distribution of particle sizes, composition, and surface morphology plays an important role in determining their behavior in different environments. Powders have found utility in every industry around the world, whether it be to formulate beauty products, enhance the bioavailability of pharmaceuticals, or as raw material in additively manufactured components. Therefore, studying the tiny particles that make up powder samples is a vital part of many scientific pursuits and industrial applications.
Conventional light microscopy has been the gold standard for studying the morphological properties of particles. As particles in powders decrease in size and become more granular, light microscopy becomes less effective at discerning their geometries and surface morphologies due to its limited resolving power. To overcome the limitations of optical microscopy, a more advanced instrument such as the scanning electron microscope is necessary. Since the SEM uses an electron beam, it has a much higher resolving power than light microscopes and can provide morphological properties of much smaller particles. Additionally, when combined with energy dispersive X-ray spectroscopy (EDS), the technique can provide elemental details of individual particles.
Sample Preparation
Sample preparation remains one of the most important steps in characterizing powders using SEM. Poor adhesion of the particle to the sample support is a critical challenge encountered when preparing powder samples for SEM. The choice of appropriate sample support can help alleviate this issue.
Another important aspect of powder preparation is to obtain a uniform distribution of particles on the sample support. Care should be taken to minimize agglomeration, which helps to distinguish single particles from collective aggregates in SEM images. Obtaining monolayers means that all the particles are adhered to the sample support, reducing the risk of loose particles contaminating various components in the SEM when the sample is exposed to a vacuum (Shown in Figure 1).
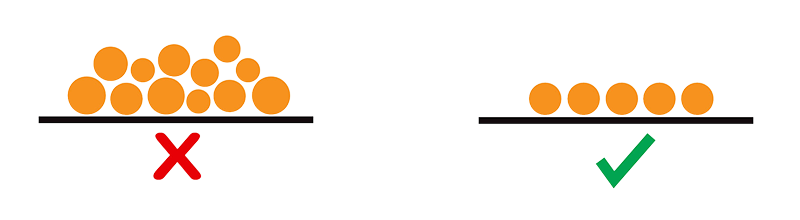
Methods to Prepare Powders
Several different methods are commonly used to prepare powder samples for SEM analysis. These range from the low-tech, low-cost methods that apply common laboratory consumables to the use of dedicated instruments such as the Nebula Powder Disperser.
Flick Method
The flick method provides a way to transfer particles onto a stub with accuracy and uniformity. This method uses a cotton swab with a wooden handle to disperse them onto a sample support as seen in Figure 2. The particles are dispersed by striking the handle of the cotton swab (flick of a finger), whereby the abrupt force dislodges the powder from the tip of the swab with enough energy to aerosolize the particles. This results in an even distribution of particles on the stub, which is crucial for accurate SEM analysis. A can of compressed air can be used to blow away any excess particles on the stub.
The rigidity of the handle is essential as it helps concentrate the spray of aerosolized particles and ensures that the particles travel a shorter distance with similar launch velocities. In contrast, an uncontrolled flinging motion with a high elasticity handle increases the range with which the particles travel, leading to a less uniform deposition on the stub.
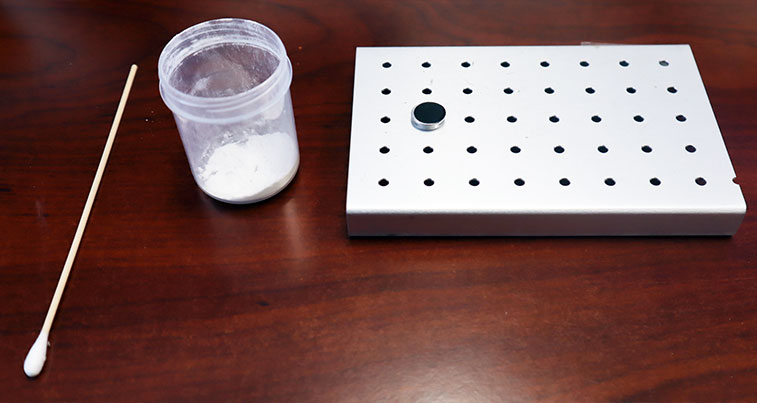
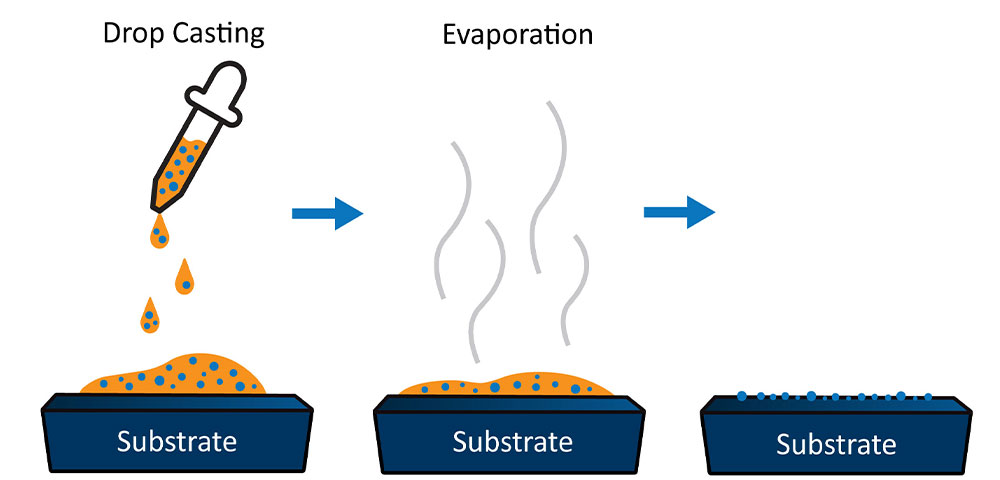
Drop Casting
Drop casting is a highly effective particle deposition technique that relies on liquid solvents to transfer particles onto a sample stub. This technique involves mixing the powder of interest in a solvent, usually with low vapor pressure, and depositing it onto the sample stub. As the solvent evaporates, it leaves behind the particles of interest deposited on the surface of the stub (Figure 3). Isopropyl alcohol and ethanol are the two most used solvents since they create a turbulent effect as they evaporate, ensuring that the particles remain well dispersed.
Dish Method
The dish method is a simple technique to prepare a monolayer of particles from a powder. In this method, the particles are spread over the area of a petri dish or similar flat surface using a spatula to form a thin, even layer of particles. Figure 4 illustrates this method by showing a stub with carbon tape attached to the surface is placed facing the powder layer and gentle pressure is applied to pick up the particles. Any excess and loosely bound particles can be removed by using a stream of compressed gas.
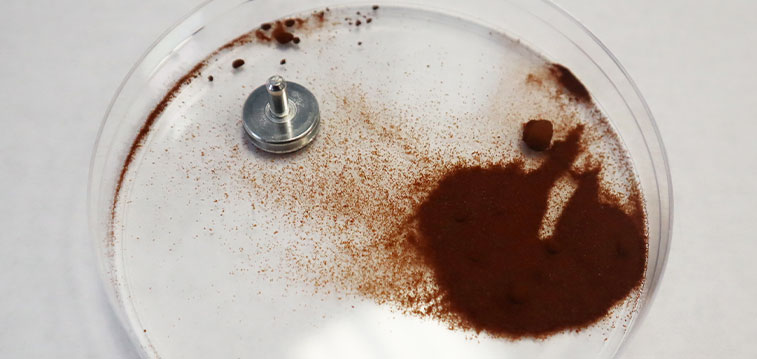
Powder Dispersion with the Nebula Dispenser
The Nebula Particle Disperser is a dedicated device made for preparing uniform powder layers for SEM analysis. The two predominant factors to adjust on the instrument are the chamber pressure and the amount of powder placed inside. Pressure controls the degree of dispersion while the quantity of powder directly correlates to the number of individual particles deposited onto the sample support. Higher vacuum levels can prevent agglomeration because the number of interactions between gaseous molecules and powder particles is reduced. The Nebula has a susceptibility to contamination compared to other methods, so it is vital to ensure thorough cleaning procedures are followed before and after every sample run.
Preparing a powder sample using the Nebula is straightforward. First, a clean stub with carbon tape is placed inside the chamber. The vacuum pressure is adjusted as needed for the powder to be dispersed. Maximum vacuum settings are suitable for metallic powders, whereas lower vacuum levels are suitable for more brittle materials subject to structural damage in a vacuum. Next, the powder is then loaded in the dispenser and dispersed in the chamber vacuum. A well dispersed sample attaches to the stub and can be used for analysis in an SEM within seconds (Figure 5).
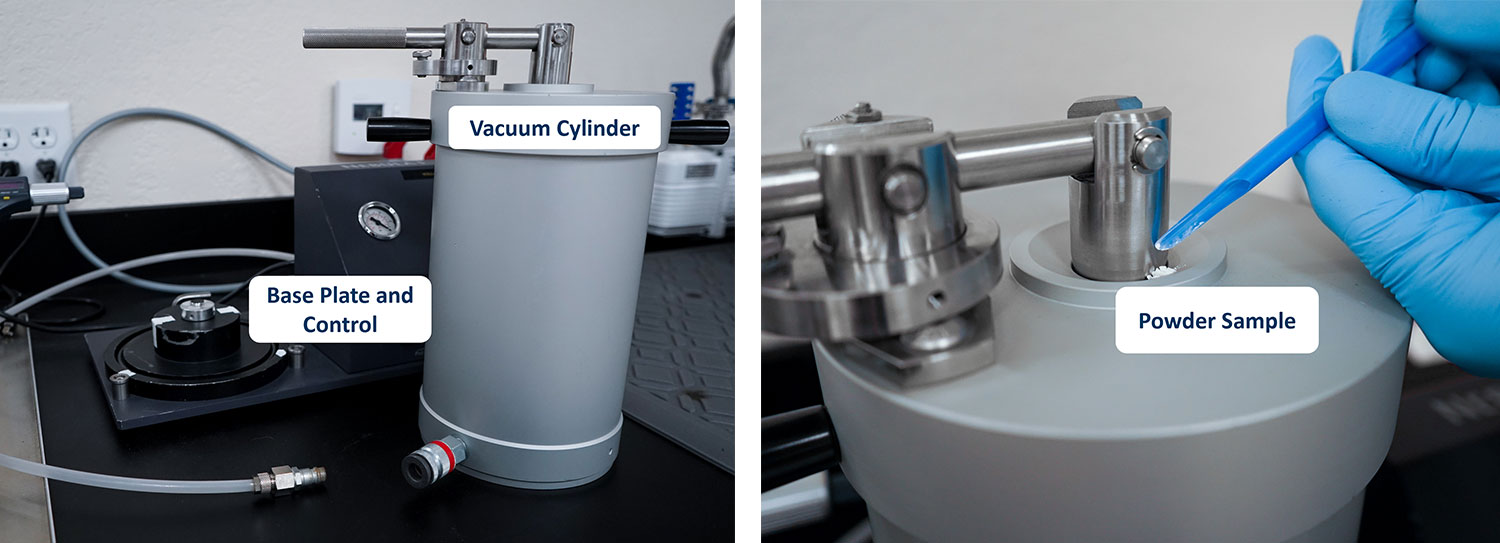
Which method works best based on the size of the particles?
For particles with diameters 500 µm > D > 1 µm
As the average diameter of particles decreases, the right number of particles is critical to achieving adequate particle separation and a monolayer of particles. To this end, the flick method is an efficient way to aerosolize a small amount of the powder (Figure 6). The dish method and Nebula dispersion device offer additional alternatives to preparing particles within this size range.
For particles with diameters 1 µm > D > 200 nm
When applying the drop casting technique here, it’s important to remember that two solvents (isopropyl alcohol and ethanol) keep particles from clumping by creating turbulence as they evaporate.
For particles with diameters D < 200 nm
As powder particles diminish in size below 200 nm, there are two ways to use drop casting. The first way involves using silicon as a base rather than carbon tape. Drop casting on the tape directly can cause the particles to sink into it, whereas silicon provides a supportive structure for the small particles to rest upon.
Alternatively, drop casting directly onto a TEM grid opens opportunities for STEM (scanning transmission electron microscopy) imaging. This is particularly of interest for particles within this size domain due to the high magnification and resolution needed to gain visibility on the sample.
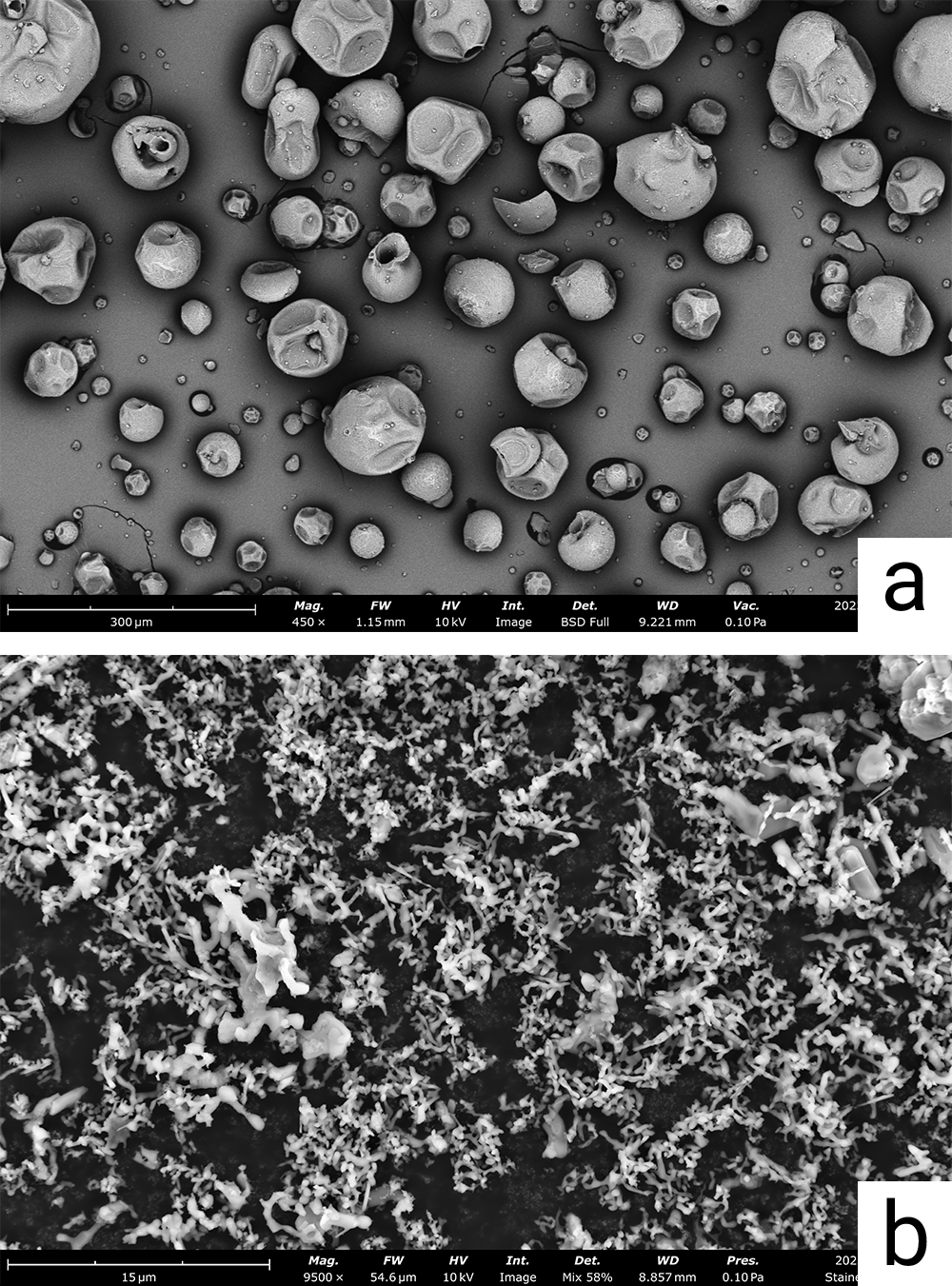
Flick | Dish | Drop-casting | Nebula Dispenser | ||
500 µm > D > 1 µm | |||||
1 µm > D > 200 nm | |||||
D < 200 nm |