What is electrospinning?
Electrospinning is a voltage-driven material fabrication process that can be used to produce micro to nano-scale fibers. The electrospinning process is a combination of interacting electric, hydrodynamic, and surface tension forces resulting in “electrohydrodynamic phenomena” which affect the electrospinning solution as a high voltage is applied. The most common basic setup involves a spinneret, high voltage source, material (e.g., polymer) in solution within a reservoir, and a grounded or charged collector.
When the high voltage is applied to the spinneret containing the electrospinning solution, the electric charges introduced begin to accumulate along the solution’s surface. The combination of this charge buildup and surface tension forces of the solution cause deformation of the liquid into a conical shape, known as the Taylor cone. Once a critical voltage is reached, the surface tension forces are overcome, and a liquid jet emerges from the peak of the Taylor cone. This straight jet is drawn toward the oppositely charged/grounded collector and experiences “bending instability”, a phenomenon that causes the jet to whip rapidly, allowing jet thinning and evaporation of the solvent to collect dried fibers on the collector surface. This process can continue for as long as desired, assuming the processing parameters and solution properties/supply are maintained.
Why use Electrospinning?
Electrospinning allows the production of continuous nanofibers with diameters ranging from tens of nanometers to a few micrometers. The diameter of the fibers can be modulated using several parameters including solution concentration, flow rate, applied voltage, needle-to-collector distance, and boiling point of solvents. Fabrication of micro and nanofibers using electrospinning has some distinct advantages that include:
1. High surface-to-volume ratios
The electrospun fibers have an extremely high surface area-to-volume ratio due to their small diameters and porous nature. This property makes them useful where large surface interactions or loading capacities are important, especially in applications in filtration, adsorption, and drug delivery.
2. Versatility
The electrospinning method can be used to process a multitude of viable materials, such as polymers, ceramics, metallic elements, or a combination of these. Whether dissolved, mixed, emulsified, or suspended, if the material(s) can be adequately incorporated into a solvent(s), it may be a candidate for electrospinning. Even delicate materials which may be temperature sensitive or require low boiling point solvents can be processed under the ambient room temperature conditions of electrospinning. This inherent versatility makes it an ideal processing option for many applications where solvent and/or material variety are a necessity.
3. Tailored properties
The properties of the electrospun fibers can be tailored to meet specific requirements such as surface area, porosity, stability, and mechanical strength. These can be achieved by controlling the processing parameters such as polymer composition, additives, and solvents. Additives, such as surfactants, salts, antimicrobials, and antibacterials can be incorporated into the electrospinning process by either loading the additive in solution before performing electrospinning, co-spinning material with an additional independent needle, or by post-processing a previously electrospun sample. The use of additives can help optimize the solution processability, enhance the sample material characteristics (rheological properties, morphology, chemical resistance), or even allow new material functionality (surface chemistry, reactivity). Fibers with different mechanical structures such as hollow fibers, core-shell fibers, and a combination of fiber and particles can also be fabricated by using advanced electrospinning techniques that include dual solution processing, coaxial or triaxial encapsulation, and gas/solvent-gas assisted electrospinning. Additionally, altering the collector type, such as a flat plate or rotating drum, provides fiber morphological differences. For example, a flat plate may be used to collect fibers that are randomly aligned, while a high-speed rotating drum may be used to collect fibers that are linearly aligned along the rotation direction.
4. Scalability
Though the electrospinning setup may be as simple as one spinneret, one applied voltage, and one material solution, the process may be expanded to include multiple spinnerets, applied voltages, solutions, and collection methods. This adaptability allows the process to be scaled from basic initial research to large industrial or commercial production. The combination of numerous material/solvent compatibilities and various setup configurations allows for a variety of producible materials and tunable throughput.
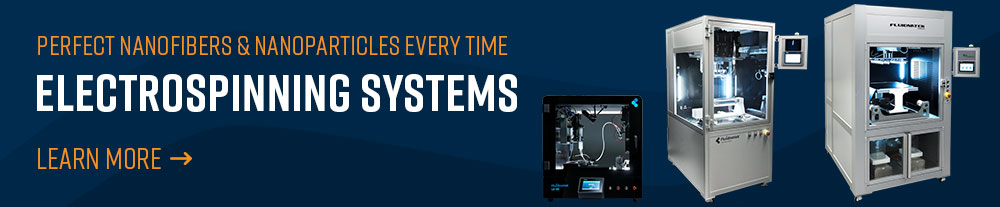
Applications of Electrospinning
The use of electrospinning has expanded into many applications including filtration, sequestration, food packaging, energy generation and storage, environmental science, biomedical engineering, textiles, and even fashion and cosmetics. Biomedical applications like tissue engineering, drug delivery, medical devices, wound healing, vein grafting, and nerve conduits have benefitted from the array of materials, setup configurations, and collector types that provide application-specific adaptability.
5. Filtration and Separation
The high surface area and porosity of electrospun nanofibers make them excellent candidates for filtration and separation applications. They can efficiently capture and remove fine particles, aerosols, and pollutants. Specialty filtration for air and water has benefitted similarly, with the high surface area to volume ratio allowing for many functional/reaction sites.
6. Energy Generation and Storage Devices
Electrospun nanofibers can be modified with catalysts to enhance catalytic reactions due to their high surface area and easy accessibility for reactants. They have been applied as catalytic membranes in fuel cells. Electrospinning has been employed to fabricate electrodes for energy storage devices such as supercapacitors and lithium-ion batteries. The high surface area and porosity of nanofibers improve the ion transport and energy storage capacity.
7. Protective Clothing and Cosmetics
Nanofiber-based materials can be utilized to develop protective clothing with enhanced properties, such as improved breathability, water repellency, flame/heat resistance, and antibacterial characteristics. Electrospun materials have found their place in textiles, fashion, and cosmetics as nonwoven fabrics, face masks, ultraviolet (UV) filtering particles, and other novel uses made possible by the immense selection of materials and flexibility of fabrication.
8. Sensors
The high surface area to volume ratio of electrospun fibers allows for many functionalized sites decorated with specific chemical groups or nanoparticles to create sensors for detecting various analytes, including gases, chemicals, and biological molecules. The ability to make electrospun fibers with different mechanical and chemical properties also assists in the development of sensors that could withstand harsh environments.
9. Drug Delivery
Electrospun nanofibers can be used to encapsulate drugs or therapeutic agents, allowing controlled release over time. This controlled drug delivery system enhances treatment efficacy, reduces side effects, and improves patient compliance. For example, encapsulation capabilities via coaxial or triaxial electrospinning allow for many drug delivery and extended-release options by layering various polymers incorporated with the desired drug.
10. Biomedical Applications
Electrospinning has found extensive use in biomedical fields including tissue engineering, wound healing, and tissue scaffolds for regenerative medicine. The nanofibrous structures fabricated by electrospinning mimic the extracellular matrix and can be used to create three-dimensional scaffolds, providing a supportive structure for cell growth and tissue regeneration. The tissue engineering and wound healing applications appreciate the fibrous nature of the materials mimicking the native tissue extracellular matrix supplemented with a high surface area to volume ratio, tunable porosity, and surface functionality.
Conclusion
Electrospinning is a valuable material fabrication method that can be adapted to suit many fields for a wide variety of applications. The inclusivity of materials, the flexibility of setup configurations, scalability, fiber size/type tunability, and ease of processability make electrospinning an attractive solution for the future’s most challenging needs.