Particles are used daily in a wide variety of applications including coating surfaces and encapsulation of active ingredients. Coating surfaces can impart additional functionality and modulate the mechanical properties of the surface. Encapsulation of active pharmaceutical ingredients (APIs) is an effective method of delivering drugs to the site of action, especially water-insoluble drugs. Encapsulation of food ingredients is commonly used to enhance or mask flavors and make food more palatable.
Depending on the application, different parameters of the particles are critical including the material, particle size (micro- or nano-scale), shape, surface roughness, and porosity. Different methods of fabricating particles have been developed including chemical precipitation, emulsification, spray drying, milling & grinding, and electrospraying. Each method has its advantages and disadvantages, with the choice of method depending on the application. Electrospraying has emerged as a method of choice for many applications that utilize polymeric, ceramic, and metals, or a combination of those materials.
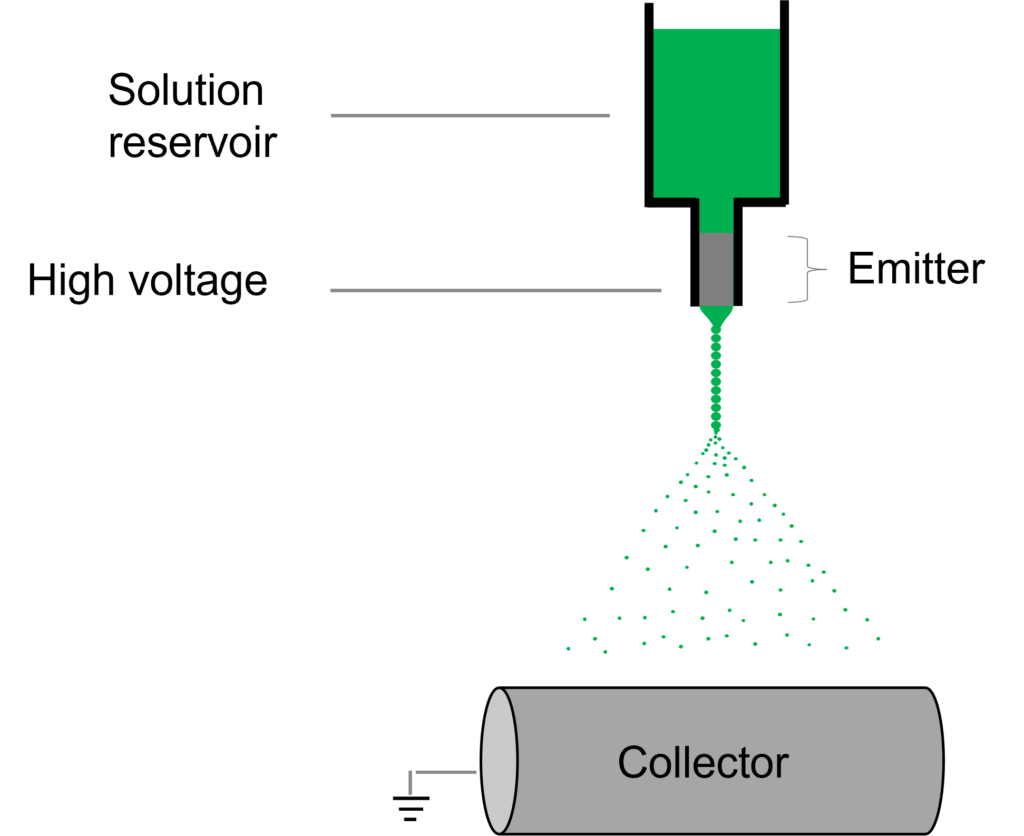
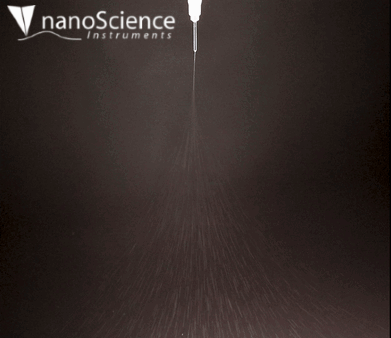
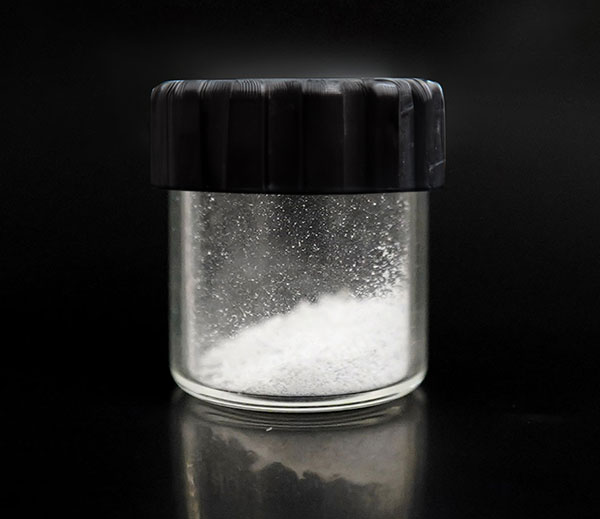
What is Electrospraying?
Electrospraying is a voltage-driven technique where a polymer solution, or emulsion in a solvent is ejected through a capillary needle at a specific flow rate in a high-voltage field. Charges accumulate on the surface of the liquid and deform into what is known as a Taylor cone. The solution is ejected towards the collector, and it breaks down into smaller drops due to Coulomb repulsion forces and solvent evaporation. The generated particles are deposited on the surface of a collector. Electrospraying has distinct advantages over other techniques for fabricating particles, including the following:
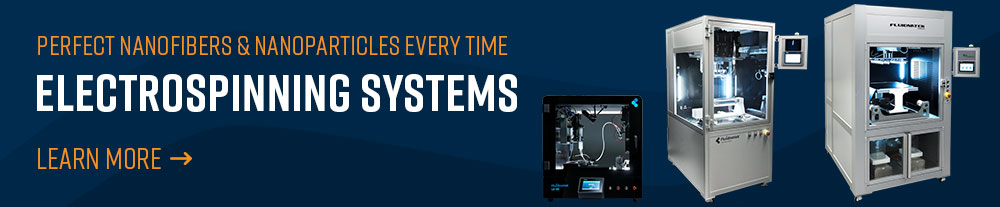
1. Control of Particle Diameter and Morphology
Electrospraying parameters can be tuned to fabricate particles of different dimensions, from nanoscale to microscale. Typical diameter ranges from 20 nm to 30 µm. Electrospraying can tightly control diameter with very little variability. The surface morphology of electrosprayed particles can also be controlled based on solution and processing parameters to create a plethora of unique morphologies. Examples include plain spherical with a smooth or rough surface, collapsed particle, Janus morphology (two distinctive structures on the same particle), buckled, wrinkled, and nail-like.
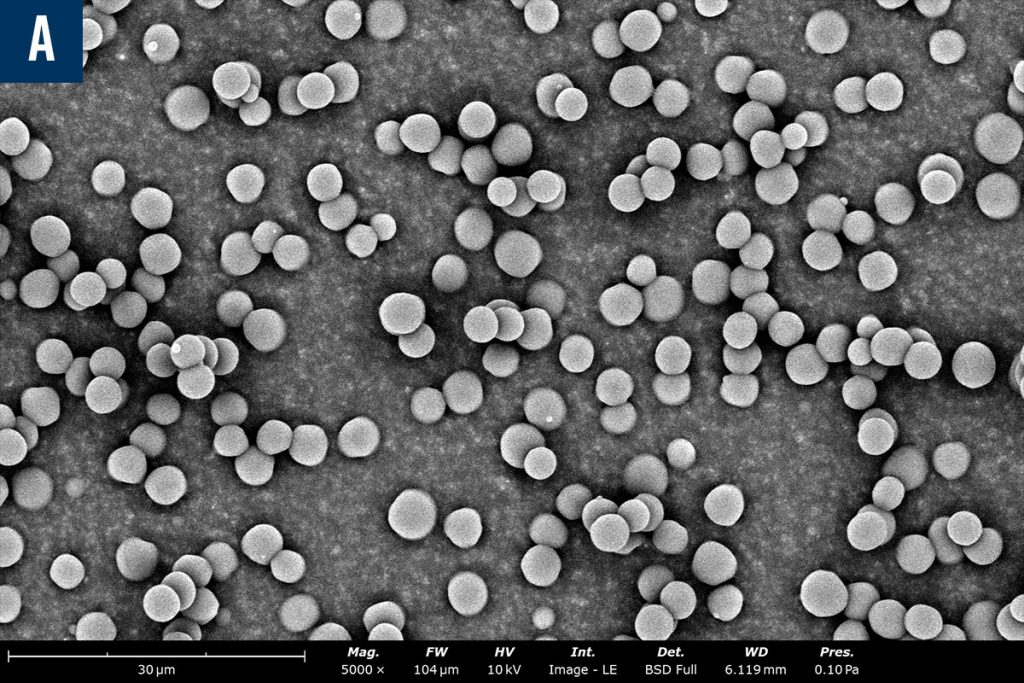
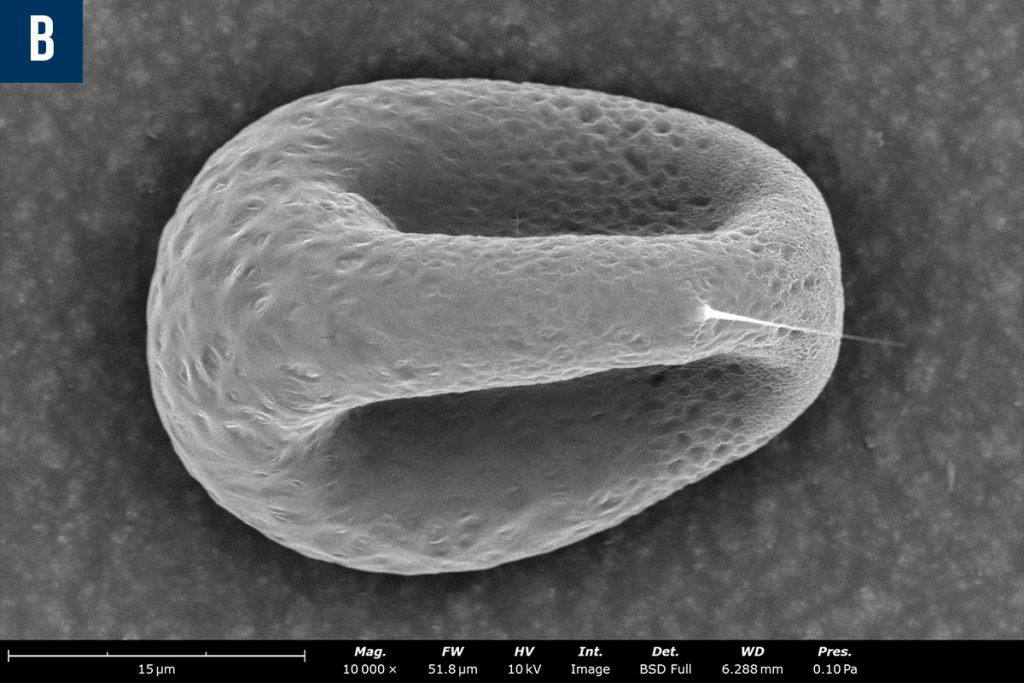
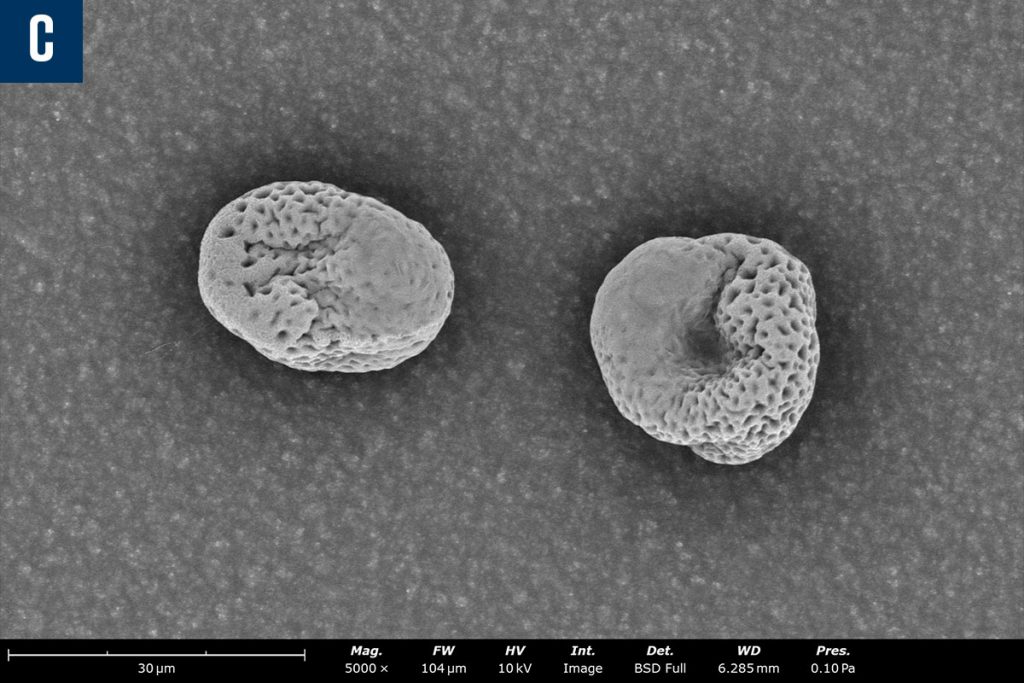
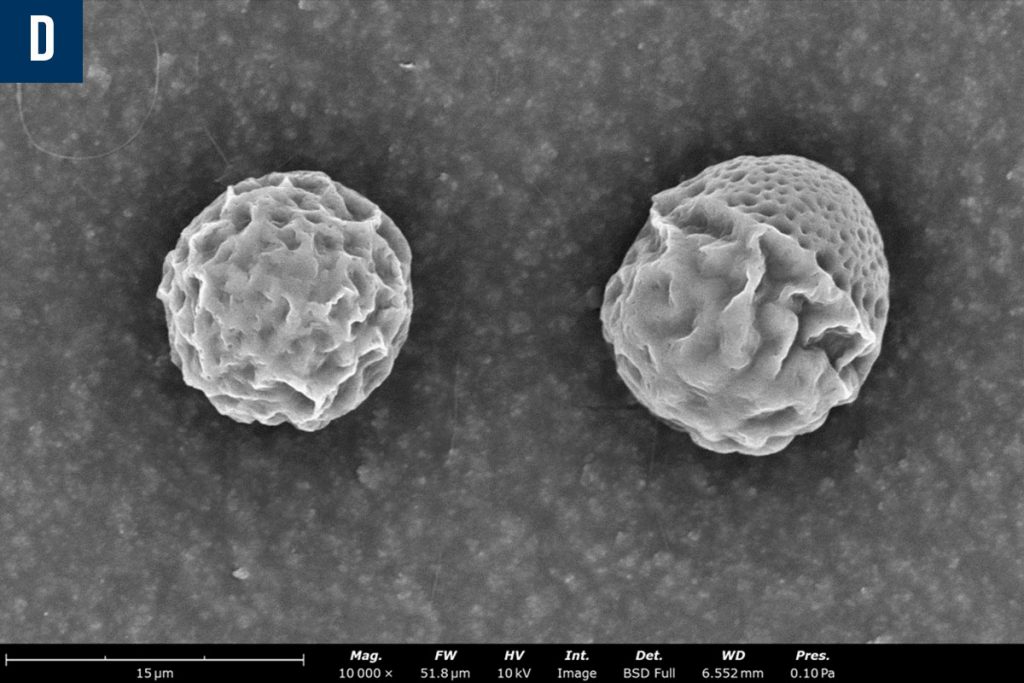
2. Dry particles are generated in a single step
The solvent completely evaporates during the electrospraying particle fabrication process. This allows the generation of dry particles in a single step which offers several distinct advantages. Dry nanoparticles will increase production efficiency, save on costs, reduce energy consumption, and enhance shelf-life. Dry particles also allow for ease of handling during transport and reduce the risk of contamination when compared to other techniques that require post-processing with other chemicals.
3. Encapsulate materials in a single step during fabrication
APIs like antioxidants, drugs, and vitamins can be efficiently encapsulated within the particles with very high efficiency during the fabrication process. These ingredients can be incorporated throughout the particle or inside the particle (ex. coaxial particles) to protect them from harsh environments. Encapsulation by electrospraying reduces the loss of active ingredients by having a minimal amount of residual solvent or carrier liquid. Since the technique minimizes agglomeration, all encapsulated ingredients are distributed uniformly within the particles. Both advantages are ideal for applications like pharmaceuticals, drug delivery, and controlled release systems.
4. Electrospraying is a room-temperature process
Electrospraying is a process that does not require heating during particle production, making it suitable to handle temperature-sensitive materials. This is important in various applications like for pharmaceutical industries where sensitive bioactive compounds or drugs can be affected even at slightly high temperatures. Another advantage of being a room temperature process is the possibilities of materials that can be used which are essential for applications where the choice of material is essential for the particle properties. Some examples of the wide range of materials include polymers, metals, ceramics, composites, particles pre-suspended in solution, and biomolecules.
5. Electrospraying can be scaled up to increase throughput
The use of multi-needles, enhanced flow rates, and material selection allows for the process to be scaled up to meet the requirements of various industries. A process developed with one needle can be scaled to multi-needle systems by solution optimization and the use of a pressure vessel to increase the flow rate by more than 10-fold. This allows electrospraying to be a practical choice for different industries in pharmaceutical, medical, food processing, electronics, and textiles, where large-scale production is necessary.
6. Electrospraying minimizes agglomeration
Control of more than 10 parameters during electrospraying makes the technique well-suited to achieve uniform and agglomeration-free fabrication of particles. This proves to be beneficial in homogenously coating surfaces with reduced material waste. The technique allows precise control over thickness for applications where the deposition thickness is critical. Preventing agglomeration and coating specific areas of your device can be achieved and is crucial for a smooth and uniform finish without clumping.
7. Fabricate Complex Structures in Combination with Other Techniques
Electrospraying can be used in combination with electrospinning, a technique used to fabricate nanofibers and microfibers, to develop nanoparticle-coated fibers. Similarly, implantable medical devices like stents and heart valves, made by other techniques can be functionalized by electrospraying. This could make the devices biocompatible or used in targeted drug delivery. Precise nanostructuring and patterning can also be combined with electrospraying to generate patterns on surfaces where a defined structure is needed. Both Electrospinning and electrospraying functionalities are available in commercial equipment like those available from Fluidnatek.
Conclusion
Electrospraying stands out as a room-temperature, versatile dry particle generation technique offering precise control over particle diameter, morphology, and encapsulation, all in one single step. Its ability to use different materials, ease of surface coating, and scale-up make it ideal for multiple industries where batch-to-batch consistency and reproducibility are key for success. Electrospraying is becoming the technique of choice for researchers and industry for particle production.