In the world of material fabrication, various techniques have emerged to create complex and functional materials for a wide range of applications, from medical devices to industrial components. Among these techniques, electrospinning and 3D printing have gained significant attention. While both methods offer unique advantages, they also present different challenges and limitations. In this blog we summarize the two techniques and deliberate if electrospinning can enhance the functionality of 3D fabricated devices.
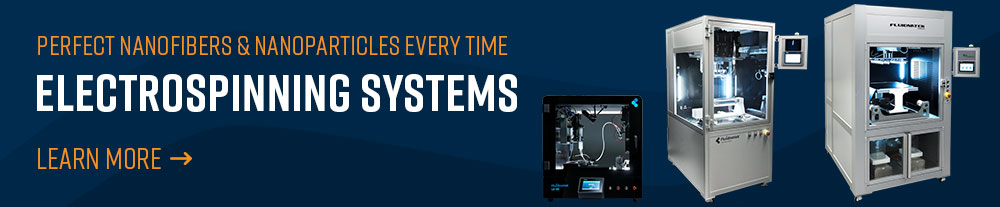
3D Printing
3D printing often involves extruding materials and depositing them to build up a structure layer-by-layer.1 Various 3D printing methods exist, including Fused Deposition Modeling (FDM), Stereolithography (SLA), and Selective Laser Sintering (SLS), each using different principles to build up 3D structures. 3D printing can use a broad range of materials including polymers, metals, ceramics, biological materials, and composites. The choice of the material is dependent on the specific 3D printing technique along with the intended end application. Controlled and precise construction of large and complex shapes can be achieved using 3D printing. Structures with specific mechanical properties can be fabricated, making 3D-printed parts more robust and suitable for structural applications. However, one of the primary limitations of 3D printing is resolution, and achieving nanoscale resolution of the fabricated parts can be challenging.
Electrospinning
Electrospinning is a versatile fabrication technique that uses an electric field to draw solutions (typically polymer) into fine fibers, typically in the nanometer to micrometer range.2 These fibers can be collected to form non-woven mats, scaffolds, or even more intricate structures, depending on the parameters used. The resulting materials have a high surface area-to-volume ratio and are porous. A wide range of materials, including natural and synthetic polymers, ceramics, and even metal oxides can be electrospun. This versatility allows for the tailoring of properties of the electrospun fibers to meet specific requirements, such as biodegradability, mechanical strength, or electrical conductivity. The ability to control fiber diameter, alignment, and surface morphology is a significant advantage of electrospinning. Electrospinning can fabricate a variety of form factors, from large area mats to small intricate structures. However, one of the limitations of electrospinning is structural rigidity. Electrospinning typically produces thin (<1mm) fibrous structures rather than thick, complex shapes.
Electrospinning vs 3D Printing
Scale vs. Complexity: 3D printing excels at fabricating complex, macro-scale geometries with high precision, while it often struggles with producing features at the micro or nanoscale. Electrospinning, on the other hand, is well-suited for creating fine fibers and structures at small scales but finds it difficult in fabricating structurally complex structures.
Structural Integrity: 3D-printed objects typically have good structural integrity, making them suitable for load-bearing applications. Electrospun materials, while less robust in terms of bulk mechanical properties, excel in applications that benefit from high surface area, such as filtration or catalysis.
Macro vs. Nano Customization: 3D printing allows for the direct translation of digital designs into physical objects, making it highly customizable in terms of shape and geometry. Electrospinning, while also customizable, is more focused on tailoring the properties of the fibers themselves rather than the overall shape of the final product.
These differences mean that the choice between electrospinning and 3D printing often comes down to the specific requirements of the application.
Electrospinning to Enhance 3D Printed Structures
Electrospinning can complement 3D printing by combining the strengths of each technique to create multi-scale, multifunctional structures (Figure 1). This synergy is particularly valuable in fields like biomedical engineering, materials science, and electronics, where combining nanoscale features (from electrospinning) with complex 3D geometries (from 3D printing) opens unique applications.
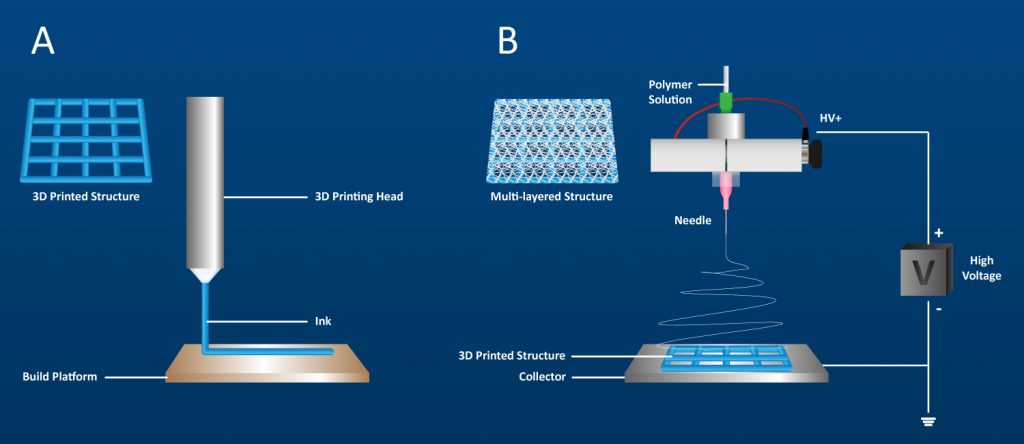
Biomedical Applications:
3D printing can fabricate strong, complex, supportive structures that provide structural integrity, while electrospinning can add a layer of nanoscale fibers on these structures. The electrospun fibers provide a large surface area and tunable porosity thereby enhancing the biocompatibility of the 3D printed structures and provide a more favorable environment for cell proliferation.3
The electrospun fibers can also be used to incorporate bioactive molecules, such as drugs, growth factors, or antibiotics, for controlled release. A 3D printed scaffold can then be used as a supporting structure or to encapsulate the fibers for controlled release of the bioactive molecules. Figure 2 shows SEM images of a 3D printed scaffold before and after it was coated with electrospun fibers. This approach is ideal in many situations including wound healing, where an initial fast release followed by sustained delivery is beneficial.
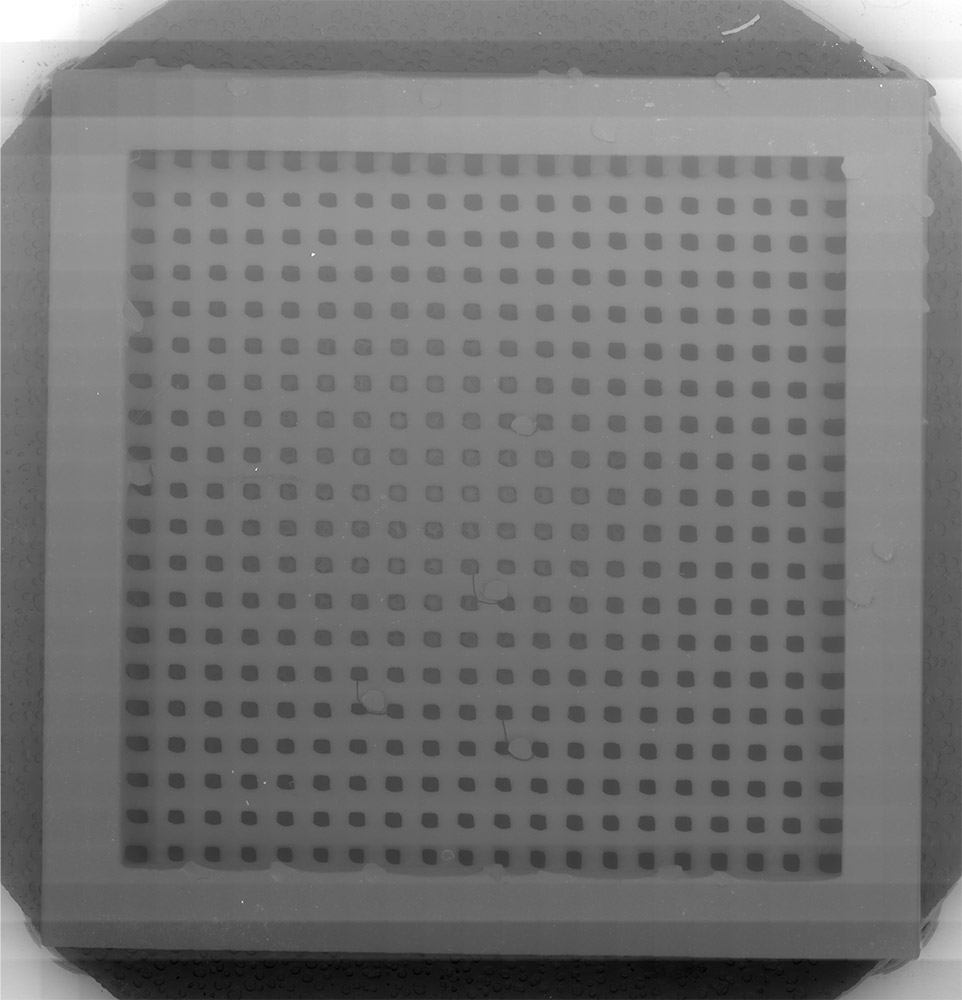
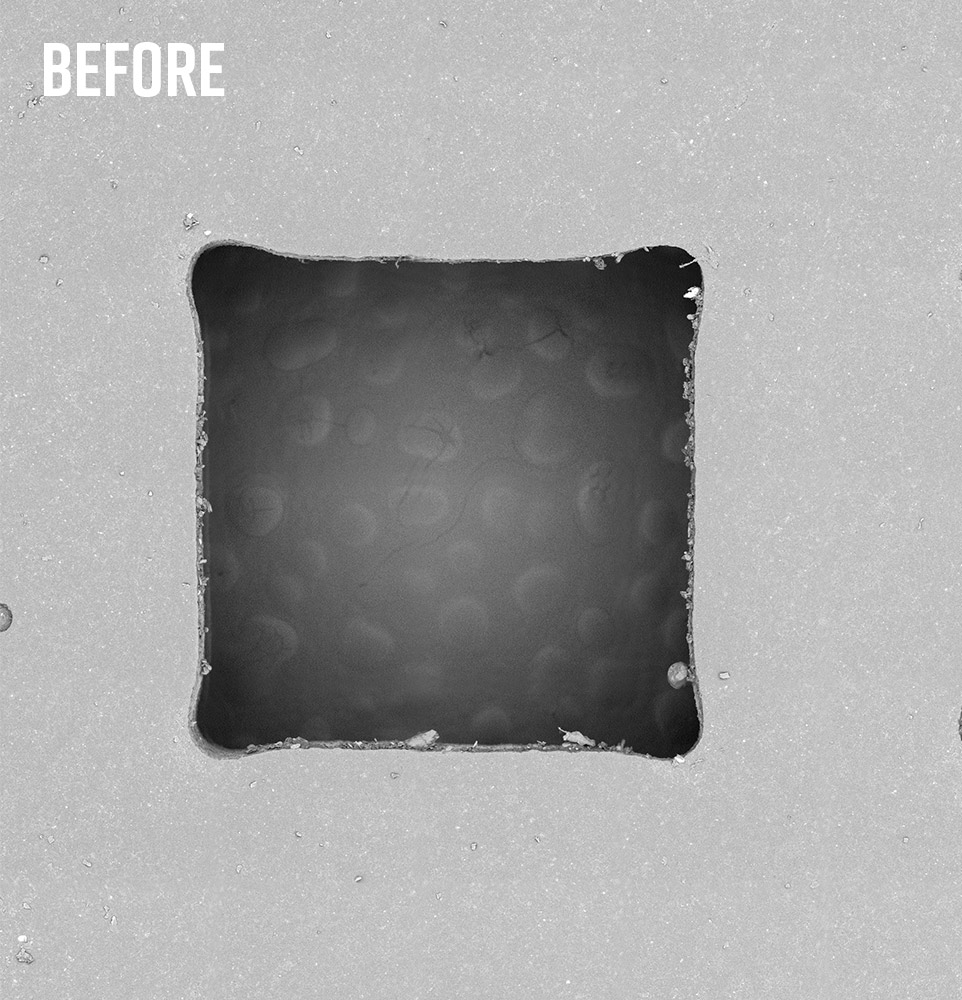
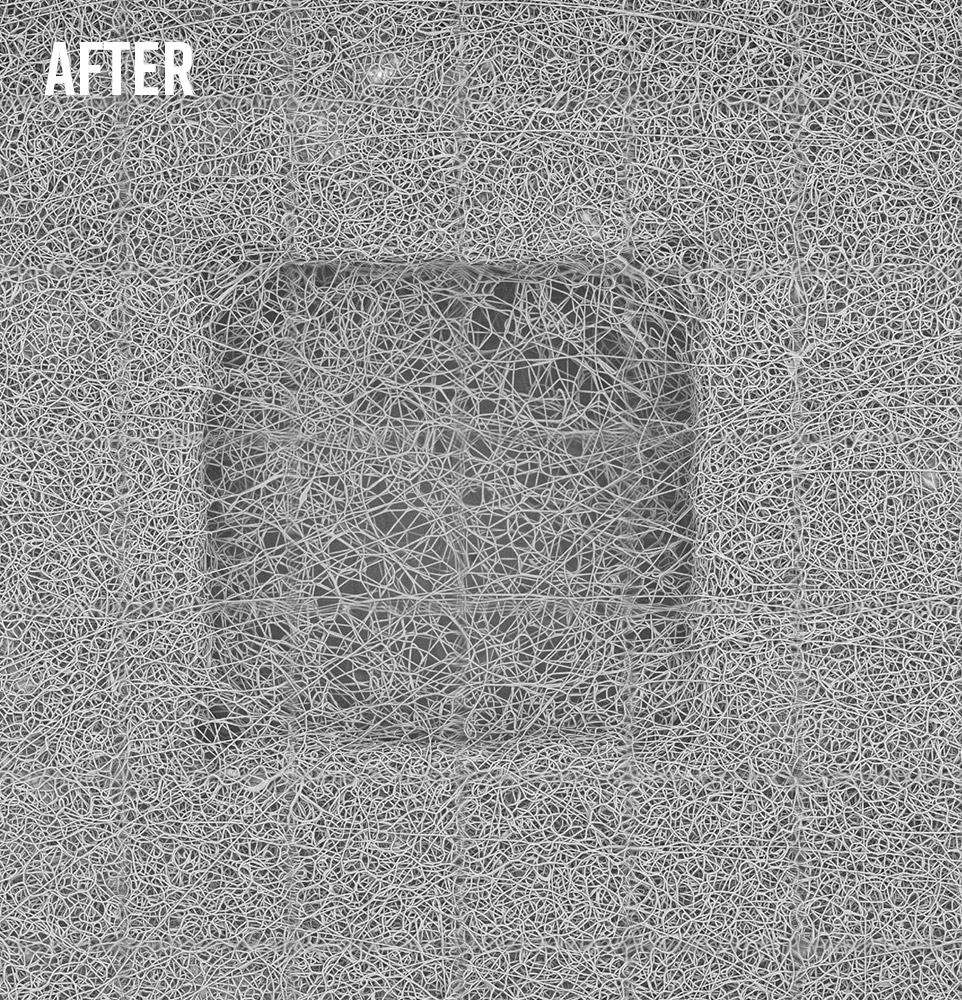
Filtration Applications:
Electrospun fibers can be used to coat the surface of a 3D-printed object, improving surface texture and increasing roughness, which is beneficial for filtration applications. 3D printing can be used to fabricate the macro-structure of a filter and electrospun fibers can add a fine, porous layer that traps smaller particles. This hybrid approach can be used to fabricate filters that are both structurally robust and effective at capturing fine particulates.4 In addition, electrospun fibers can be imbued with specific surface treatments or functional particles, like hydrophobic or antibacterial agents to enhance the surface properties of 3D-printed objects without altering their bulk structure.
Energy Applications:
In fuel cells or batteries, 3D-printed supports can be coated with electrospun fibers to offer high surface areas that are beneficial for providing reaction sites for catalytic reactions or tunable porosity and conductivity for ion exchange. Combined, these structures can enhance the efficiency and lifespan of energy devices.
Conclusion
In summary, 3D printing is versatile technique for fabricating complex, load-bearing structures at the macroscale with precise geometry while electrospinning is ideal for the fabrication of fine, fibrous, high-surface-area structures. In many cases, the best approach may involve combining both techniques to leverage their respective advantages. For example, a scaffold for tissue engineering might be 3D printed to achieve the desired macrostructure, then coated or reinforced with electrospun fibers to enhance cell attachment and growth.
Electrospinning and 3D printing complement each other by bridging the gap between macro- and nanoscale fabrication, enhancing the properties and potential applications of combined materials. This integration unlocks innovations in fields requiring both detailed surface properties and complex structural designs.
References
- Jandyal. A., et. Al., 3D printing – A review of processes, materials and applications in industry 4.0. Sustainable Operations and Computers, 2022. ↩︎
- Xue. J., et. Al., Electrospinning and Electrospun Nanofibers: Methods, Materials, and Applications. Chemical reviews, 2019 ↩︎
- Thangadurai. A., et. al., Advances in electrospinning and 3D bioprinting strategies to enhance functional regeneration of skeletal muscle tissue. Biomaterials advances, 2022 ↩︎
- Kozior. T et.al., Electrospinning on 3D Printed Polymers for Mechanically Stabilized Filter Composites. Polymers (Basel) 2019. ↩︎