Electrospinning and electrospraying technologies continue to gain prominence due to their versatility in nanofiber and nanoparticle development. Researchers, scientists, entrepreneurs, and industry professionals face the daunting task of choosing from a range of commercial and homebuilt solutions that meet the needs of their specific applications. One primary consideration is the price of the electrospinning machine which ranges from about ten thousand dollars to over a million dollars.
A combination of technical features, accessories, quality, and support services influence the cost of an electrospinning device. When considering an electrospinning device, it’s essential to evaluate the specific features and capabilities that align with the requirements of the desired application. This article discusses how several key aspects of electrospinning machines affect the cost.
Electrospinning machines can be broadly classified into home-built and commercial systems. The commercial systems can further be categorized as benchtop, floor model, and production scale equipment.
Home-built systems
Home-built systems can be a cost-effective way for basic proof-of-concept experiments when developing electrospun nanofibers or electrosprayed nanoparticles. They usually consist of a syringe pump, a high-voltage power supply, a spinneret, and a collecting device like a metal plate. Parts are usually acquired from different vendors and can be built for around $10,000.
Home-built systems offer basic capabilities for fabricating nanofibers and nanoparticles, but their main drawback is the lack of reproducibility and batch-to-batch consistency. It is challenging to develop a repeatable fabrication process using homebuilt systems since they do not have good environmental control, a critical factor that influences the electrospinning process. Also, since the parts for the system are acquired from different vendors and not designed to function in unison, getting them to work cohesively will prove challenging with virtually no support from any of the vendors. The software required to operate the system must be developed, and changes will need further programming. An additional concern is user safety due to the lack of ventilation and any safety features, such as emergency shut-off.
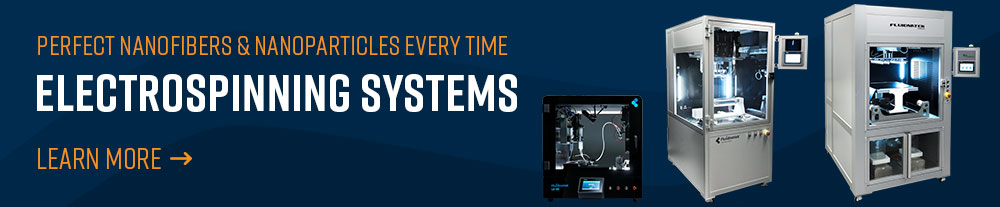
Commercial Systems
Commercial systems have been engineered with the goal of achieving consistent and reproducible fabrication of fibers and particles while ensuring user safety is of the highest priority. Price ranges from $20,000 to over $1,000,000, based on the configuration and capabilities. They offer a variety of accessories that can be implemented based on application needs, safety features, automation, and sample production. Features that are necessary to meet regulatory requirements like cGMP, ISO-13485, or standards like ASTM F3510-21 are also available.
Benchtop systems
The price range for commercial benchtop systems typically ranges from $20,000 to $250,000 based on features that are included. These are compact systems that can be easily placed on a benchtop in a standard lab setting. Processing parameters are typically controlled through built-in touchscreen panels. Processes can be automated with recipe functions and all critical parameters can be recorded with software-specific capabilities.
A range of accessories are usually available that allow the user to expand the capabilities of the instrument as their needs grow. This includes the addition of a rotating drum collector for fabricating aligned nanofibers and/or introducing an additional high-voltage source and stage allowing simultaneous electrospinning of two materials with independent control. Optional environmental control systems where predetermined temperature, relative humidity, and airflow can be maintained during sample processing would be available. These features enable homogenous fabrication of nanofibers and nanoparticles and are key to controlling batch-to-batch reproducibility. The ability to modulate emitter translation speed and distance between the emitter and collector also assists in the fabrication of a wide range of homogenous samples. Safety systems including ventilation under a slightly negative pressure to properly remove solvent vapors, a safety interlock system to prevent user contact with high voltages, and emergency buttons to power off the unit in case of emergencies are also features that can be found on benchtop systems.
Benchtop systems provide an ideal pathway for users who are currently looking to develop a repeatable process for fabricating nanofibers and nanoparticles but would like to scale up production in the future. While commercial benchtop electrospinning machines may have higher upfront costs than home-built systems, they can offer long-term cost-effectiveness with advanced options and safety features.
System | Output | Emitters | Collectors | Accessories | Safety | Cost |
Home built | + | + | + | + | • | $ |
Benchtop | ++ | ++ | ++ | ++ | •• | $$ |
Floor Systems | +++ | ++++ | +++ | +++ | ••• | $$$ |
Production scale | ++++++ | +++++++ | + | ++ | ••••• | $$$$$$ |
Floor Systems
The price range for floor systems typically ranges from $100,000 to $600,000 depending on the accessories, and scalability of the equipment. Floor-model electrospinning machines have all the features of benchtop systems and are suited for facilities with a need for higher production volumes. Floor systems can accommodate a larger number of needles (up to over 300 needles) and larger collectors to achieve larger sample sizes and increase throughput. Drum collectors with a diameter of 20 cm and a length of 30 cm, allow the fabrication of 20 cm x 62 cm sheets. The use of roll-to-roll collectors is also feasible if larger sheets are required. Due to the larger chamber size, they can be integrated with other techniques like 3D printing or even robotic arms to coat non-symmetrical samples.
Environmental conditions are more tightly controlled, and production under clean conditions is possible in certain models, as they offer sterilization and HEPA filtration functionalities. Another advantage of the floor model is the capability to work under inert environments by implementing nitrogen flow to reduce oxygen content when flammable solvents are needed for high throughput fabrication. Floor systems are ideal in applications requiring larger samples, advanced sample production, or planning toward scale-up production.
Production scale
The price for a production-scale electrospinning system is over $1,000,000 due to the large size, capabilities, and cost involved in setting up the facilities. Production scale electrospinning machines offer the capability to work with over 5,000 needles and volumes of more than 40 liters of solution that can be continuously filled. They are designed for continuous processing and reliable operation, allowing for 24/7 production for large-scale manufacturing. They are engineered and customized to meet specific industry needs such as pharmaceutical, biomedical, textile, and battery material production.
Conclusion
From research to industrial production scale, the cost of an electrospinning/electrospraying system varies widely based on the available options, accessories, throughput, safety features, and support. During the decision process of selecting an electrospinning system, the needs of the application should supersede the cost factor. Some of the other non-pricing-related aspects that should be considered include the availability of local support, upgradability, scalability, and versatility of the system. By understanding the specific requirements, prioritizing key features, and considering factors such as scalability, safety, and integration capabilities, an informed decision can be made while choosing the appropriate electrospinning machine.