Nanofibers, particularly polymeric nanofibers, are a burgeoning frontier in the world of materials science, offering a diverse array of applications across industries. These fibers, typically with diameters ranging from a few nanometers to a few hundred nanometers, represent a transformational leap in material engineering. Their unique properties, which include an extraordinarily high surface area, tunable mechanical properties, and flexibility, have propelled them to the forefront of scientific research and technological innovation. From biomedical applications, such as drug delivery systems and tissue scaffolds, to environmental solutions, like air and water filtration, nanofibers are shaping the future of sustainable materials.
There are several methods for fabricating nanofibers, which range from innovative and sustainable techniques to more traditional processes. Here we discuss 5 processes, electrospinning, self-assembly, template-based synthesis, phase separation, and melt-blowing. Each of these comes with its own set of advantages and limitations, the understanding of which is essential to select an appropriate fabrication method to meet the needs of the application. Electrospinning, with its precision and versatility, stands as a cornerstone, offering exceptional control over fiber properties. Phase separation, template-based synthesis, and self-assembly methods excel in their capacity for tailored structures and material diversity, yet they require fine-tuning and often face challenges in scalability. Melt blowing emerges as an efficient and scalable solution, particularly in high-throughput industrial applications, despite its limitations in achieving ultrafine fibers.
Electrospinning:
Electrospinning is a widely used technique for producing nanofibers. It involves ejecting a thin jet of a polymer solution into an electric field, causing the material to be drawn and stretched into nanofibers as it is deposited onto a collector. It is a versatile and relatively simple method, capable of producing nanofibers from various materials, including polymers, ceramics, metallic elements, and composites. One of the key strengths of electrospinning is its ability to operate at room temperature, making it a highly versatile and energy-efficient process that allows the fabrication of nanofibers from thermolabile materials. It also generates dry nanofibers in a single step, eliminating the need for time-consuming post-processing.
Electrospinning can accommodate fiber ranges spanning from the nanoscale to the microscale, multiple orientations of fibers, and multiple fiber types (hollow, coaxial, porous, etc.) allowing the creation of complex structures to address diverse application requirements. The technique also boasts the ease with which additives such as nanoparticles, biomolecules, drugs and others can be incorporated. Electrospinning is also a powerful technique to coat a variety of 2D and 3D substrates, including intricate geometries like meshes (e.g. stents), symmetrical, and non-symmetrical samples, expanding its utility in different fields. Advancements like the incorporation of multi-emitters, needle-less emitters, or gas-assisted electrospinning offer the ability to scale up to meet the needs of larger industrial-scale production. Electrospinning can be combined with other methods, like electrospraying, to further enhance the characteristics of the final product.
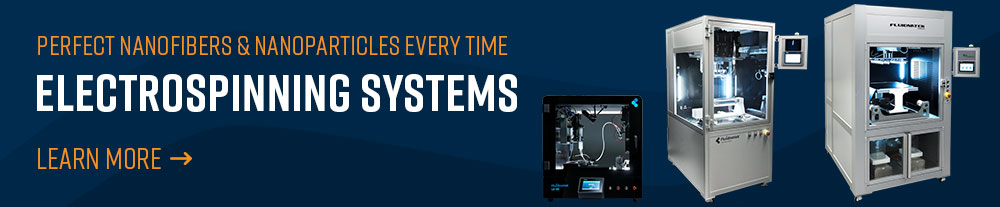
Self-Assembly:
Self-assembly methods rely on the natural tendency of certain molecules or nanoparticles to assemble into nanofibrous structures through non-covalent interactions. Examples include peptide-based self-assembly and DNA nanofiber formation. These methods can produce highly ordered nanofiber structures with specific functionalities. One of self-assembly’s primary strengths lies in its simplicity and efficiency, as it harnesses the intrinsic properties of certain molecules or nanoparticles to autonomously arrange into nanofibrous structures. This innate self-organization eliminates the need for complex and energy-intensive processes, minimizing the overall environmental footprint of nanofiber production. Moreover, the self-assembly method offers a high degree of control over the resulting nanofiber structures.
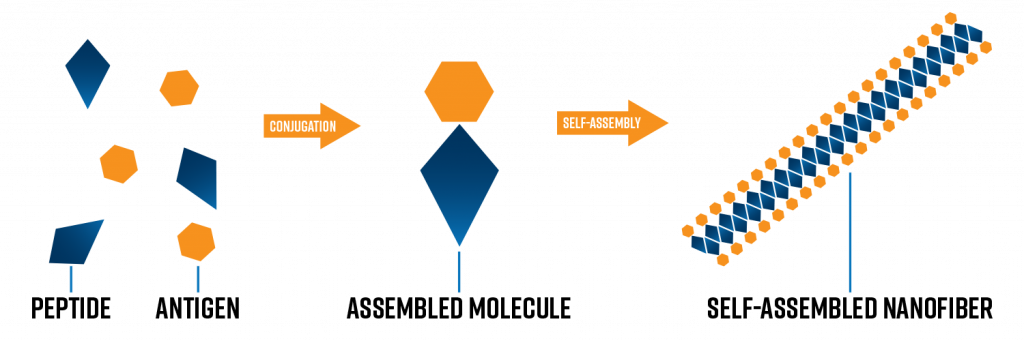
However, the method is limited to certain materials with certain intrinsic properties. Tuning the properties of the fibers or incorporating other components into the fibers can prove to be challenging.
Template-Based Synthesis:
Template-based methods use porous templates as molds for nanofiber formation. Materials are deposited into the template, and after removal of the template, nanofibers remain. By using templates with precise geometries and dimensions, researchers can dictate the size, shape, and alignment of the resulting nanofibers, allowing for the fabrication of complex structures. This level of control is invaluable in applications demanding strict dimensional specifications, such as photonic devices and filtration membranes. Moreover, template-based synthesis enables the production of nanofibers with a diverse range of materials, including metals, polymers, and ceramics. The technique is amenable to scalability and mass production, offering efficiency and reproducibility that are crucial for industrial applications.

Additionally, template-based synthesis can be a more environmentally friendly approach compared to some energy-intensive methods, as it often operates under mild conditions and minimizes waste. On the other hand, the method can be limited to certain materials and the separation of nanofibers, and the template may be challenging.
Phase Separation:
Phase separation techniques involve the controlled separation of different phases of a material to form nanofibrous structures. Examples of this method include thermally induced phase separation (TIPS) and nonsolvent-induced phase separation (NIPS). Phase separation provides versatility in accommodating a wide variety of materials, including polymers, ceramics, and composites. This adaptability allows for the creation of nanofibers with diverse properties and functionalities.
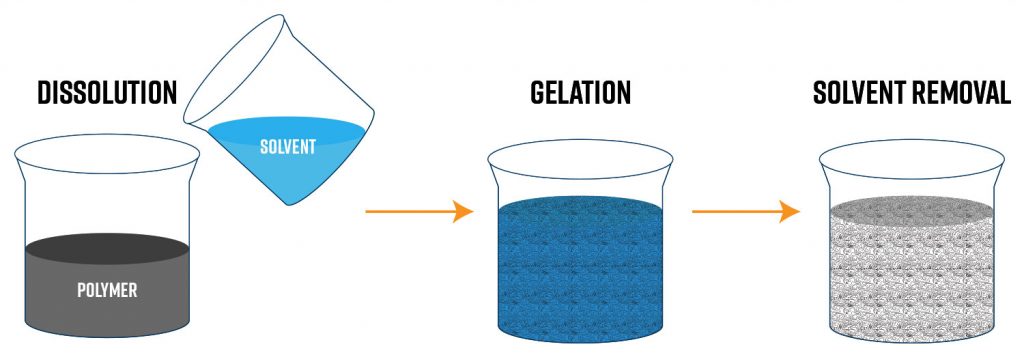
However, this method is limited to specific materials which can be processed into phases, and it may require optimization for different applications. Another notable advantage of the phase separation method is the precise control it provides over nanofiber morphology and porosity. Researchers can tailor the resulting structures by adjusting parameters like solution composition, temperature, and solvent choice. The phase separation method can also often operate under relatively mild conditions, minimizing the risk of damaging sensitive or bioactive components. The simplicity and cost-effectiveness of the phase separation technique make it an attractive option, as it eliminates the need for complex equipment or energy-intensive processes, contributing to its widespread adoption and utility in various fields.
Melt Blowing:
Melt blowing is commonly used for producing nanofiber-based nonwoven materials by extruding a molten polymer through fine nozzles and then stretching the fibers using high-speed air or other gases. The melt blowing method is efficient and scalable, making it attractive for nanofiber production. Its continuous and high-throughput process allows for the production of nanofibers at a rapid rate, making it suitable for large-scale manufacturing in various industries. The melt blowing method offers simplicity in operation and versatility in material selection. It involves melting a polymer and extruding it through fine nozzles while simultaneously introducing high-speed air to attenuate the polymer into nanofibers.
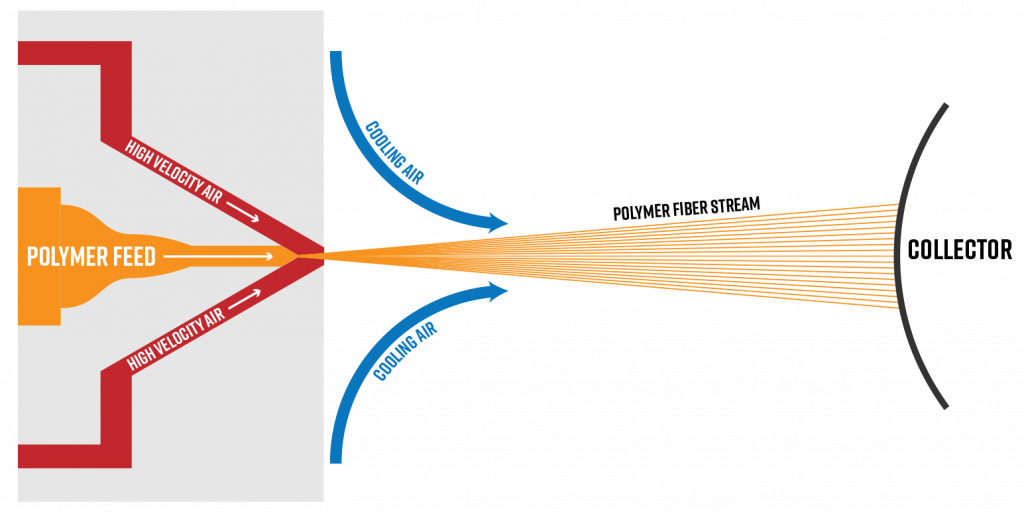
This straightforward process can accommodate a wide range of polymers, enabling the production of nanofibers with diverse chemical and mechanical properties. It is simple and cost-effective; however, it is limited to thermoplastic polymers and does not allow much control over the properties of nanofibers, such as diameter uniformity. On the other hand, melt blowing can be easily integrated into existing manufacturing lines, providing a seamless means of incorporating nanofibers into various products, even directly onto a substrate.
Conclusion
In the realm of nanofiber fabrication methods, each technique presents a unique set of advantages and limitations that collectively shape the landscape of nanomaterial engineering. Electrospinning, with its precision and versatility, stands as a cornerstone, offering exceptional control over fiber properties despite its energy demands. Phase separation, template-based synthesis, and self-assembly methods excel in their capacity for tailored structures and material diversity, yet they require fine-tuning and often face challenges in scalability. Melt blowing emerges as an efficient and scalable solution, particularly in high-throughput industrial applications, despite its limitations in achieving ultrafine fibers. Collectively, these methods form a rich palette, allowing researchers and engineers to select the most fitting approach based on their specific needs, balancing precision, scalability, and material diversity. The future of nanofiber fabrication lies in the synergy between these techniques, leveraging their strengths and overcoming their limitations to propel the field toward new horizons of innovation and application.