From zippy city scooters to heavy duty haulers, modern automobiles are assemblies of thousands of precisely manufactured components working in harmony to ensure smooth and safe rides. Beneath the sleek exteriors and plush interiors are components that at one point underwent stringent inspection for microscopic defects, particulates, and structures that could negatively impact performance, durability, and safety. These microscopic details make the difference between a flawless vehicle and a recall-ridden liability. One versatile method providing this microscale insight is scanning electron microscopy (SEM). SEM can reveal the intricate morphological and topographical details down to the nanometer scale. SEM uses a focused electron beam to raster-scan the surface of the sample and a range of detectors for collecting the resulting signals. SEM can even determine chemical compositions and contaminant sources when paired with elemental analysis techniques like energy-dispersive X-ray spectroscopy (EDS). With rapid sample turnaround and automated acquisition, modern SEM systems allow automotive manufacturers to perform quality assurance and process troubleshooting in-house. The analytical power of SEM makes it an extremely useful tool for continuous improvement across automotive research, development, and production workflows.
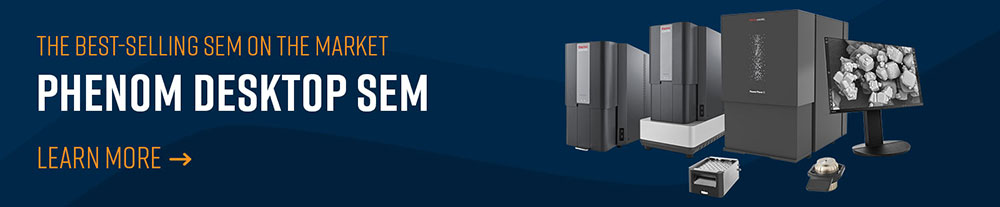
Dirty or Clean? Technical Cleanliness of Automotive Parts
Technical cleanliness is essential for optimizing the performance and longevity of modern road vehicles. Microscopic contaminants, if left unchecked, can degrade efficiency and reliability by abrasively wearing down surfaces, clogging nozzles, or short-circuiting electronics. To enable consistent cleanliness control, the automotive industry follows rigorous protocols like VDA-19 (German Association of the Automotive Industry) and ISO 16232 (the international standard) for the manufacturing of products. These standards establish guidelines for conducting automotive component cleanliness testing. They describe various extraction methods for obtaining particulate samples as well as different quantitative analytical methods and how to interpret the results for adherence to technical cleanliness.
While adhering to ISO 16232 provides a baseline minimum for technical cleanliness, truly unraveling the root causes of particulate contamination requires a more advanced examination of the particles. Established legacy methods like optical microscopy and gravimetric analysis simply lack the resolution to comprehensively characterize microscale threats. SEM generates extensive data on particle sizes, shapes, distributions, and chemical compositions, providing multidimensional datasets that can be used to pinpoint contamination pathways and sources. For example, morphological analysis can distinguish between spherical airborne particles against jagged metal debris. During parts machining or engine operation, extreme heat and pressure can cause wear and tear, resulting in debris formation. Hard abrasive particles, like metal and carbide shards, from these engine parts can then mix with lubricating oil in the system. If this isn’t controlled, abrasive contaminants circulating in oil can eventually cause deeper scouring on contact surfaces. SEM imaging could identify and quantify the damaging metal and carbide particles, highlighting angular shapes indicative of a debris origin rather than smoother particulate matter from environmental dust ingress.
EDS enables even deeper insights by discerning particulate elemental compositions. EDS analysis could pinpoint if contaminants contain signatures of ferrous metals from cylinder bores, chromium from piston rings, nickel or silicon carbides from bearing wear, or aluminum from engine block machining. This deep understanding provided via SEM of the nature and origin of contaminants enables diagnosing and addressing root causes of technical cleanliness issues right at their source.
By upgrading from minimal ISO compliance to robust SEM particle analysis, manufacturers gain the insights needed to continually strengthen processes against defect-causing contamination. Technical cleanliness standards represent just the starting line – enhanced analytical techniques like SEM provide ongoing intelligence for proactive root cause corrections and contamination prevention.
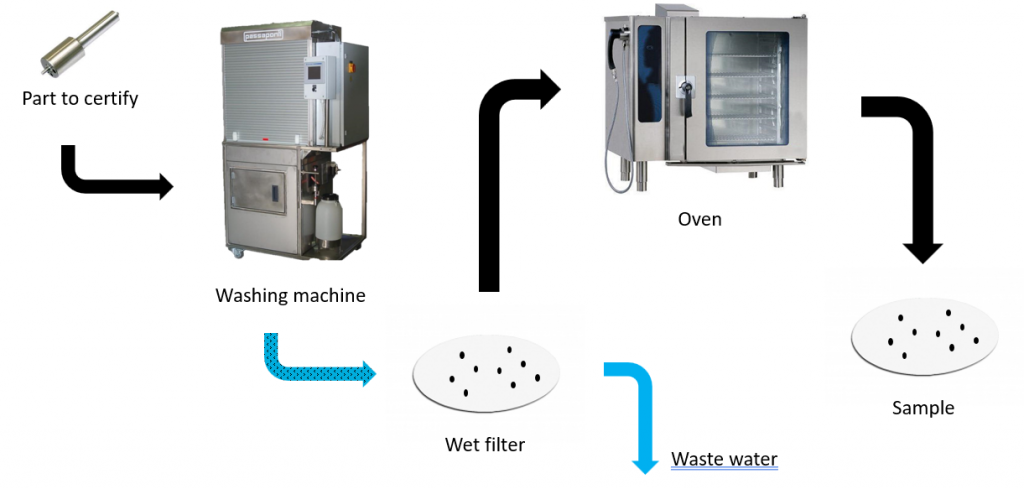
Electric Vehicle Batteries
Electric vehicles represent the future of the automotive industry. As such, developing batteries with a maximized driving range and lifespan is imperative to their mainstream adoption. This makes quality optimization in battery materials and manufacturing critical for EVs. SEM helps battery engineers make ongoing improvements as they can reach previously inaccessible details at the micro and nanoscale with the technique.
High-resolution imaging is key to visualizing crucial morphological details of battery microstructures that influence overall performance factors like charge capacity and energy density. Therefore, careful electrode surface characterization helps optimize formulations by identifying ideal particle size distributions. Maximizing these qualities in turn maximizes reactive surface area and ion transport kinetics within the battery architecture.
EDS provides an additional layer of indispensable revelations when used correlatively with SEM. This powerful combination enables precise quantitative elemental analysis on individual battery particles, elucidating particle heterogeneities invisible to bulk measurements.
In this EDS example of nickel, cobalt, and manganese particles, a ternary diagram from the data exposed fluctuations up to 20% in cobalt content within the same batch. Even more striking, the analysis spotlighted greater inconsistencies in nickel versus manganese proportions, especially in larger particles. Without this granular characterization, these hidden irregularities could propagate, leading to reliability issues and performance variations. Therefore, EDS analysis allows battery engineers to pinpoint and remedy sources of compositional discrepancies during formulation and synthesis. Such meticulous optimization during synthesis, homogenizes particles, in turn maximizing reactive surface area and ion transport kinetics within the battery framework.
In addition to materials research, SEM assists failure analysis of battery materials by revealing cracking, corrosion, and general separation issues in layered battery components. Imaging these degradation modes provides insights to iteratively refine compositions, coatings, and fabrication methods to enhance durability over time. Pairing these capabilities with EDS further bolsters the depth of analysis in terms of the sheer volume of morphological and chemical classification datasets available to engineers.
In Summary
By revealing the microscopic details that underpin the functionality of automobiles, SEM enables ceaseless refinements that allow vehicles to travel farther, perform better, and last longer. This versatile technique helps ensure that whatever century automobiles and electric vehicles drive into, it will be one attributed to the rigorous science conducted on the smallest of scales.