Electrospinning & Electrospraying
Electrospinning Collectors
A critical component of the electrospinning or electrospraying setup is the collector, as it is where the sample is deposited. For electrospinning, the type of collector used during processing has a direct impact on the alignment of the fibers as well as the size and shape of the final electrospun sample. For electrospraying, the type of collector can prevent particle agglomeration and allow easier removal of particles post-processing.
The various Fluidnatek collectors enable precise deposition of the material of interest to produce defect-free nonwoven sheets, tubular structures, continuous yarns, or fine coatings on products of all sizes and shapes.
The collectors are crucial components of Fluidnatek systems and should be chosen based on application needs, taking into account how the final sample will be manipulated at the microstructural level. For demanding or unique R&D and product development projects, we also offer customized collectors to help meet specific needs. Whether standard or customized, all our collectors are plug-and-play and can be interchanged at any time, depending on the sample that will be developed.
Collector Types
Talk to an Instrumentation Specialist Today!
Electrospinning & Electrospraying
Collectors for Electrospun & Electrosprayed Materials
Flat Plate Collector
The flat plate is the most common deposition surface used for collecting electrospun nanofibers or electrosprayed nanoparticles. Nanofibers collected on the flat plate deposit in random alignment with respect to each other when no external force influences the electric field, resulting in the fabrication of flat sheets of nanofibrous material. Thanks to its simplicity, the flat plate is an ideal platform for initial testing of polymer solution formulations and is often the first collector used by electrospinning novices. Fluidnatek’s flat plate collectors can be stationary or motorized, offering surfaces ranging from 20 cm x 20 cm to 60cm x 64cm, depending on the equipment model and its chamber capacity. When using the flat plate collector in combination with needle translation in X-Y-Z axes, homogeneous samples can be achieved. The flat plate collector is commonly used to coat flat surfaces such as semiconductors, surgical meshes, conductive substrates, or thin non-conductive materials. A liquid reservoir can also be placed atop the flat plate collector to collect nanofibers or nanoparticles.
Drum Collector
Drum collectors are motorized, cylindrical devices that rotate at various speeds to collect electrospun fibers or electrosprayed particles. Fluidnatek systems utilize a universal rotating platform, which allows drum collectors and other rotating collectors (e.g. mandrels and disks) to be interchanged as needed throughout electrospinning or electrospraying processes. Drum collectors are typically made of anodized aluminum, but other materials are available if modifications are necessary for a specific application. For example, Stainless Steel 316L drum collectors have been developed for customers in the medical industry to improve cleanliness when Fluidnatek systems are installed in clean room environments. Fluidnatek’s standard drum collectors range in size from 10 cm to 20 cm in diameter, with widths of 20 cm to 30 cm. They can be adjusted to rotate in either direction at speeds as low as 20 rpm up to 3,000 rpm, based on the model of the equipment in which they are installed. Drum collectors with different rotation speeds can also be designed by request.
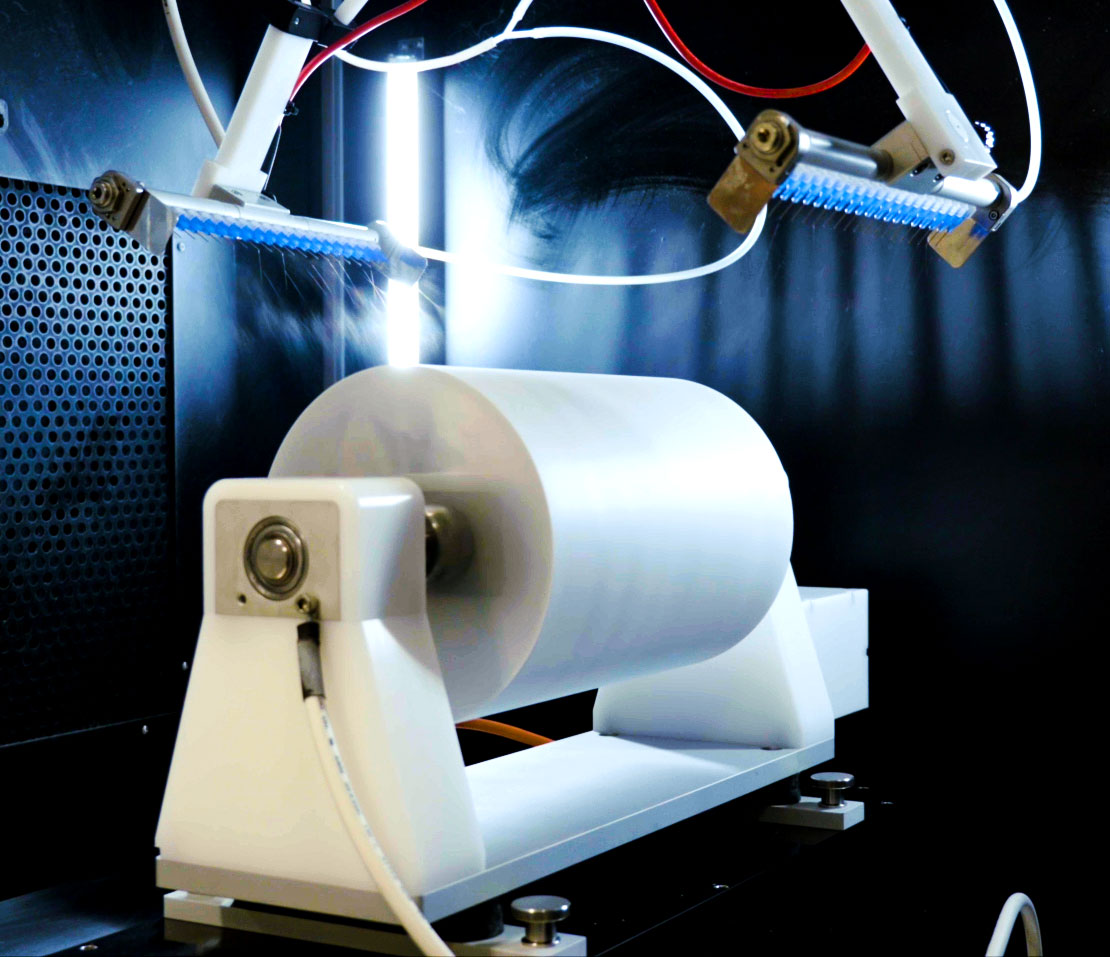
Employing dual sample processing while using the rotational drum supports easy development of advanced materials. This configuration allows the generation of samples composed of two or more different materials at the same time (e.g. two types of fibers, two types of particles, combination of fibers and particles, or fibers and live cells).
For electrospinning, the rotational speed and diameter of the drum collector influence the microstructure of the final sample; specifically, the alignment of fibers with respect to each other. By varying the rotational speed or size of drum, it is possible to generate samples with randomly, semi-aligned, aligned, or super-aligned fibers. With larger diameter drums and/or higher rotational speeds, the linear velocity will increase, resulting in increased fiber alignment.
In the examples of electrospun polycaprolactone (PCL) microstructures shown below, the drum diameter remained constant while rotational speed was increased for each iteration of the process. As the rotation speed increased from 50 rpm to 2000 rpm, the microstructure of the nanofibers became increasingly aligned.
Demonstrated effect of drum RPM on fiber alignment
For electrospraying, the drum collector can be used to prevent particle agglomeration based on the rotational speed used. Thanks to the negative voltage applied to the collector and its compatibility with almost any substrate, particles can be collected onto the drum with ease.
Mandrel Collector
The mandrel collector, like the drum collector, utilizes Fluidnatek’s universal rotating platform to collect homogeneous layers of nanofibers in thin, hollow cylindrical shapes. This allows easy fabrication of tubular nanofibrous structures, which are increasingly used for tissue engineering applications as scaffolding materials. The mandrel collector also allows mounting of tubular devices such as stents, heart valves, and other medical devices for the application of electrospun and electrosprayed coatings, which is a key feature of the Fluidnatek LE-100 BioTubing electrospinning and electrospraying system. A benefit of using mandrel collectors for such coatings is that they support the deposition of electrospun fibers on the inside and outside of a tubular medical device, functionalizing all surfaces. Several mandrel diameters are available for the Fluidnatek electrospinning machines, from 250 µm wires to 10 mm or larger rods. As demonstrated in the video, two different materials can be deposited onto a mandrel simultaneously to generate advanced materials, depending on application needs.
Disk Collector
Fluidnatek’s disk collector attaches to the same universal rotating platform that is used for the drum and mandrel collectors and collects aligned fiber bundles along the disk’s edge. Depending on equipment model, the standard disk is either 20 cm or 30 cm in diameter with a 1 mm sharp edge. Since the collector has such a narrow surface area, all fibers are attracted towards the 1 mm edge, allowing them to align more easily than fibers collected on a rotating drum, even at low rotational speeds. This collector is a useful tool for forming sutures and other multifilaments or electrospun yarns on a small scale. It can also be used to collect small amounts of aligned fibers for proof-of-concept purposes.
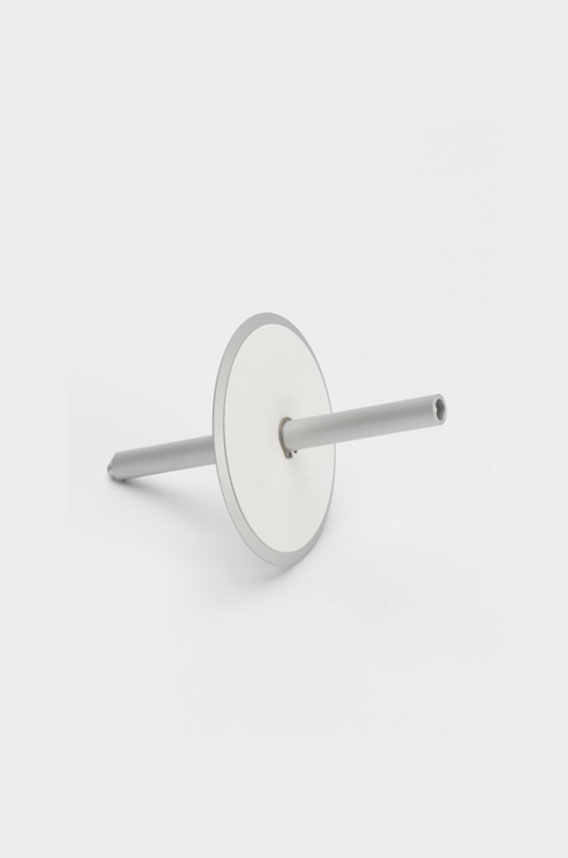
Yarn Collector
The Fluidnatek yarn collector is a unique solution for streamlining the fabrication of continuous bundled nanofibrous yarns. This intricately engineered collection system attracts the jet of electrospun nanofibers towards a conical rotating collector, which in simplified terms, coils electrospun fibers into one continuous yarn structure. The fibers can be attracted towards the collector area in three different ways: by implementing a grounded collector, charged collector, or charged pin electrode. A motorized winding system on the opposite end of the collector apparatus then twists to collect the yarns on a reel for secure storage, along with constant translation of the emitter to improve continuous homogeneity of the collected yarn throughout the reel length. Depending on the rotational funnel and reel winding speeds, different types of morphologies can be achieved in the final electrospun yarn.
The yarn collector can also be used to continuously coat filaments with electrospun fibers or electrosprayed particles. Filaments such as surgical sutures, fiber optics, or other materials can be functionalized to improve mechanical properties, loaded with drugs or therapeutic agents for controlled drug delivery directly to surgical sites, or made more biocompatible for medical device applications. Fluidnatek’s yarn collector expands the possibilities for advanced yarn development and filament coating.
Roll-to-Roll Collector
The roll-to-roll collector enables users to fabricate large sheets of electrospun material or continuously collect electrosprayed particles. The collector system includes a flat plate with two motorized rollers on both sides for loading and moving the substrate based on speed and individual roll tension. Positive or negative voltage can be applied to the flat plate during the spinning process to pull fibers or particles towards the substrate as they are emitted from the jet(s). By continuously rolling the substrate across the flat plate collection area and utilizing needle/emitter translation during the electrospinning process, the roll-to-roll collector ensures homogeneity in mat thickness and sample distribution for large quantities of collected material. An example of this process is shown in the video below, in which a 20-needle linear emitter setup was programmed to translate across the collector surface while the roll-to-roll collector provided automated movement of the substrate to form an even, homogeneous layer of nanofibers.
Conveyor Belt for Roll-to-Roll Collector
Depending on the type of substrate used with the roll-to-roll collector, it may be beneficial to implement Fluidnatek’s conveyor belt, which helps to ensure that the substrate continues to roll smoothly across the charged flat surface during processing. This accessory allows the use of conductive substrates and prevents them from adhering to the flat plate collector area on the roll-to-roll assembly. It also prevents tears or deformation when using thin substrates like nonwoven materials for filtration applications or thin medical meshes.
Dummy Collector
The dummy collector enables users to streamline electrospinning or electrospraying workflows and keep final samples uniform and defect-free. It is intended to be used for semi-continuous processes in which a new sample needs to be generated. In general, the dummy collector provides a secondary location over which the emitter can hover when starting electrospinning processes, removing finished samples from the chamber, or during longer processes in which multiple collectors are used. This supports a faster process and exchange of collectors, boosting productivity without significant interruptions. Use of the dummy collector requires a translating emitter motion system as well as an additional high voltage connection.
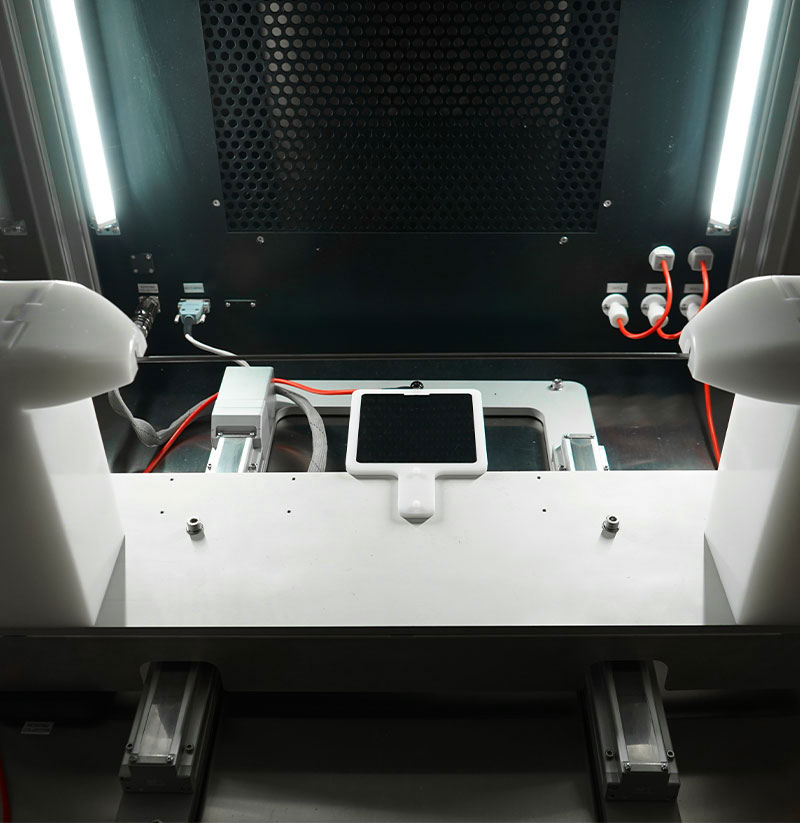
Custom Collectors
Electrospinning and electrospraying are used in different industrial applications and research fields. Some applications might demand the use of collectors that are not currently available, or that require specific modifications based on the types of microstructures desired in the final sample. In these cases, we can collaborate with Fluidnatek to help you obtain a customized collector that will fulfill your application needs. Over the years, we have developed different types of collectors based on complex requirements, including a collector where non-symmetrical samples can be coated, and flat plate collectors with temperature control between 0 °C and 150 °C for when in situ cooling or sintering is necessary. Please reach out to us to discuss your application and we will help you find the right solution for your electrospinning and/or electrospraying needs.
Electrospinning & Electrospraying
Product Knowledgebase
Webinar
Innovative Drug Delivery Systems for Wound Healing Using Electrospinning
Chronic wounds and wound infections are a major problem for the society and novel treatmen…
Blog
Fabricating Complex Geometries with Electrospinning
Electrospinning has emerged as a transformative technique for fabricating fibrous material…
White Paper
Controlling the Orientation of Electrospun Nanofibers for Tissue Engineering
Electrospinning is a versatile and promising technique for fabricating nanofibrous scaffol…