Electrospinning & Electrospraying
Electrospinning Emitters
There are several types of emitters, also referred to as nozzles or spinnerets, used for processing electrospun fibers and electrosprayed particles, or blow-spun or sprayed materials. The type of emitter used for an electrospinning or electrospraying process depends on the desired morphology and composition of the final product, based on application needs.
The Fluidnatek systems utilize carefully designed Luer Lock-compatible emitters that are engineered to produce a stable, reliable Taylor Cone. Whether reusable or disposable emitters are desired, the Fluidnatek systems can accommodate it. These ‘needle-based’ emitters are the standard for Fluidnatek equipment, but the instruments are not limited to only needle-based processing. When higher throughput is desired, it is also possible to use Fluidnatek’s unique ‘slit injector,’ which offers controlled electrohydrodynamic processing of solutions without using needles, and offers capabilities for gas-assisted processing.
Emitter Types
Single Phase Emitters:
Needle-less Emitters:
Talk to an Instrumentation Specialist Today!
Electrospinning & Electrospraying
Single Phase Electrospinning Emitters
Single Needle Electrospinning Emitter
The single phase, single needle emitter is the most common emitter employed in electrospinning processes and is typically used to generate small amounts of nanofibrous materials or nanoparticles. Using just one blunt-tipped needle and one liquid solution feed, this emitter creates nanofibers or nanoparticles of one morphology at a time. A benefit of using a needle that produces a single Taylor cone and jet per emitter is that this setup produces uniform, homogeneous electrospun samples, with minimal defects in fiber morphology, microstructure, or macrostructure of the final sample. The single-phase, single emitter configuration provides a controlled platform for optimizing solution and process parameters when initiating the fabrication of an electrospun or electrosprayed sample. Whether using a solution, emulsion, suspension, or dispersion, the single-phase, single-needle setup is the best starting point for proof-of-concept and R&D projects to develop fibers or particles.
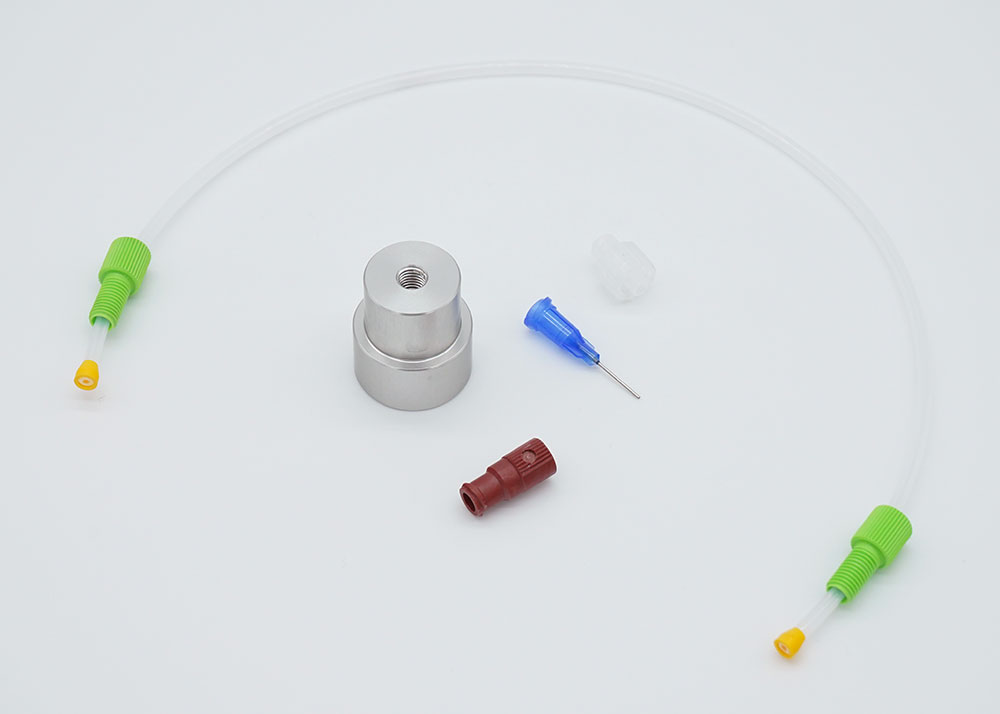
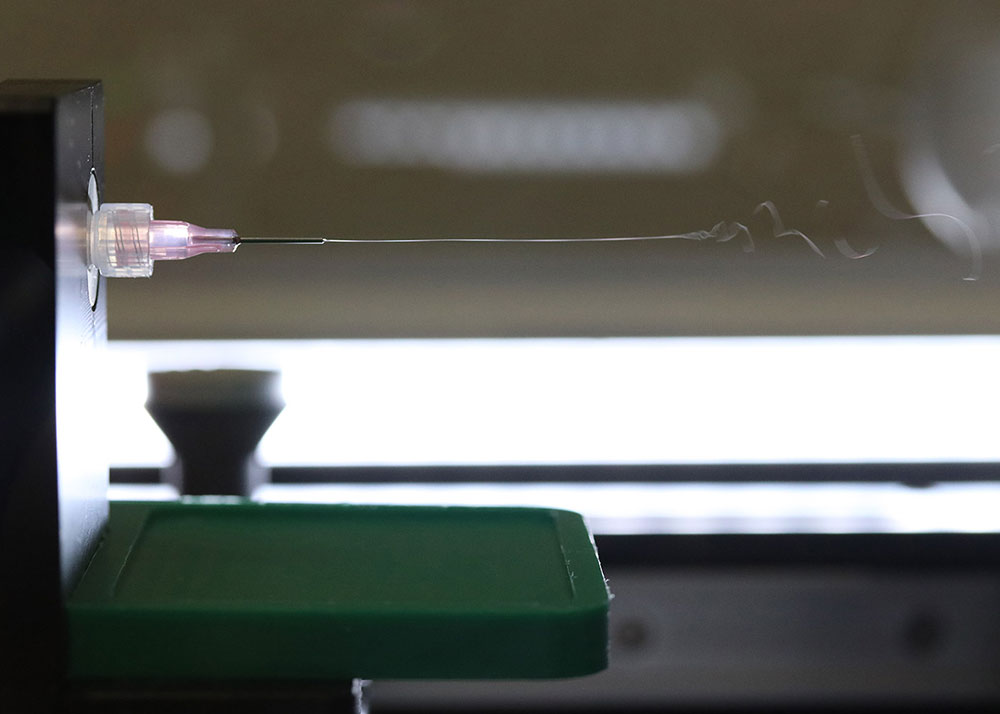
Tubeless Solution Dispensing System
The tubeless solution dispensing system eliminates the need for tubing when flowing your solution, thereby minimizing waste of high value solutions during processing. It employs a secondary liquid that advances your material through the dispenser by means of a plunger, preventing the generation of any dead volume. Whether there are limited volumes of biological materials or costly polymers being used, the tubeless solution dispensing system allows for maximum material production with minimal loss of solution.
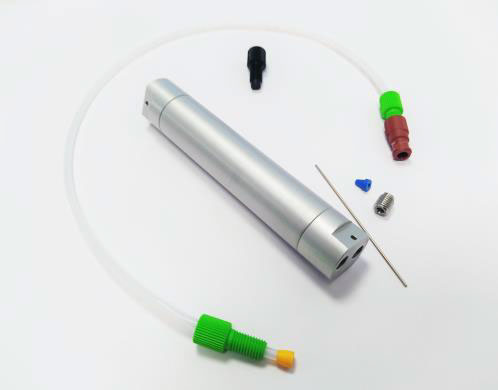
Single Phase Solution Heating Device
Used to perform hot solution electrospinning or electrospraying when using liquids with high surface tension and/or high viscosities are employed. In combination with the tubeless solution dispensing system, this system will allow you to increase solution temperature from 30 to 120°C with one solution in single-phase. Ideal accessory to manipulate the solvent evaporation rate when using solvents with low vapor pressure or when temperatures above 45°C are needed to achieve nanoscale fiber or nanoscale particles through electrospinning. It also opens the possibilities of using less-toxic solvents when compared to regular solution electrospinning and depending on application needs.
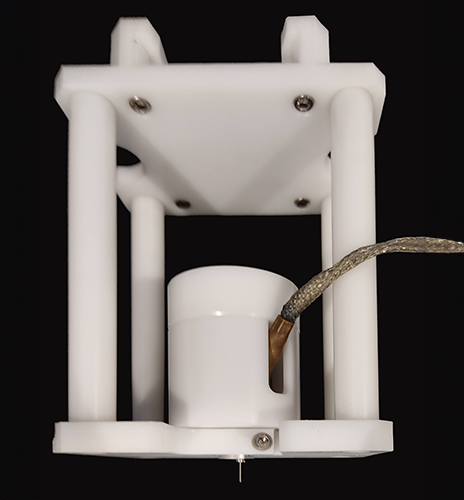
Multi-Needle Linear Emitter
The multi-needle linear emitter allows the use of multiple needles to increase throughput during an electrospinning or electrospraying process. Fluidnatek’s proprietary multi-needle emitters are engineered to maintain equal pressure across every needle, minimizing clogged emitters, allowing consistent flow throughout each nozzle, and creating samples with unrivaled homogeneity.
Linear emitters for Fluidnatek systems can be configured with 5, 20, 30, or 37 needles, and stacked to total up to 370 needles, depending on the equipment model in which the multi-needle apparatus will be used. Being Luer-Lock-based, any port not needed can be blocked, allowing fine tuning of the process based on application needs.
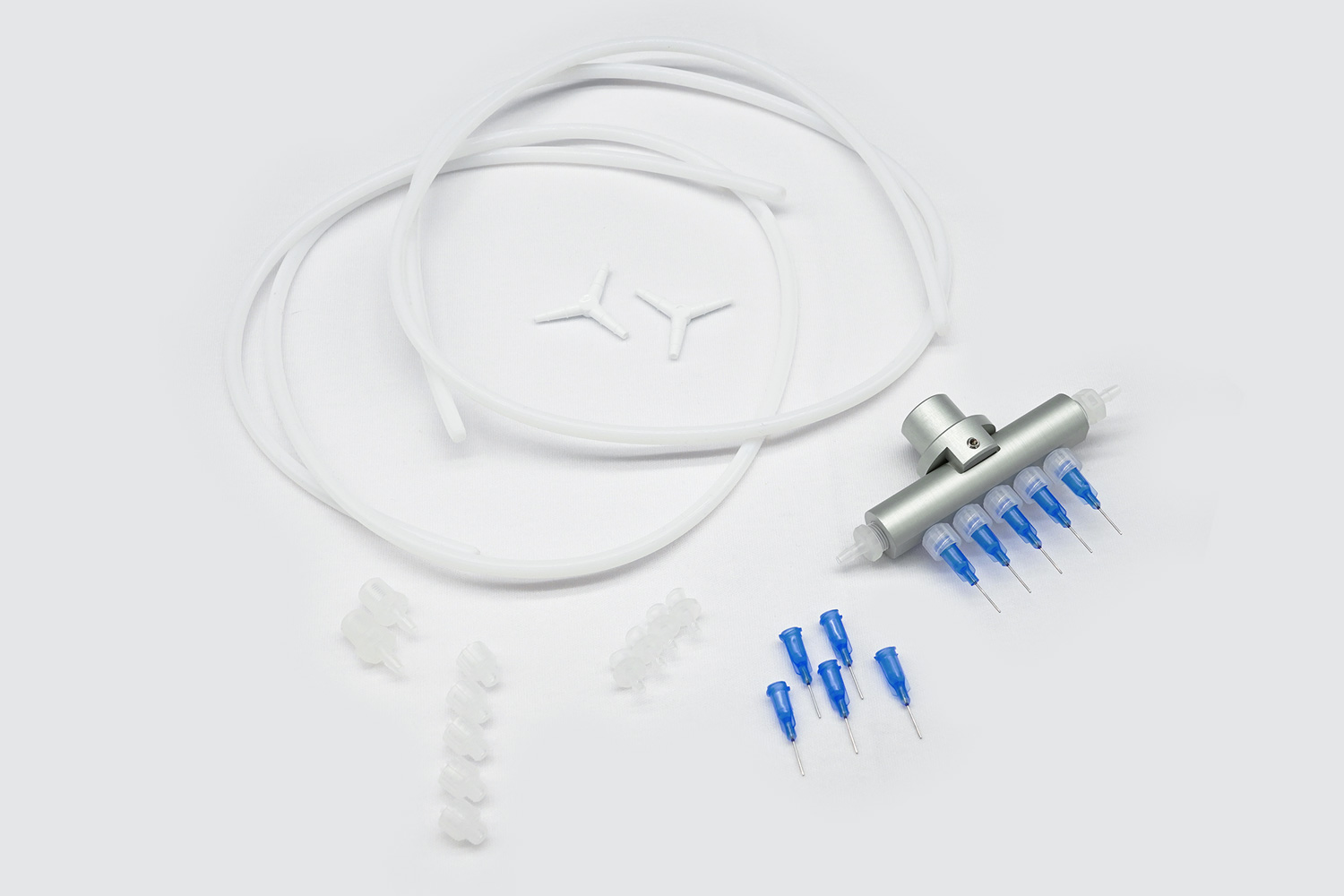
Field Deflectors for Linear Multi-Needle Emitters
When working with linear multi-emitter electrospinning setups, the individual jets from each needle will repel each other due to charge repulsion. The Fluidnatek technology implements the use of field deflectors, which are metal plates at the end of the linear multi-emitter with the same charge as the needles. They are available for most of our linear multi-needle emitters, which mitigate charge repulsion between polymer jets and redirect them towards the collector to improve sample deposition and homogeneity. The effectiveness of the field deflectors is demonstrated by the following photos, in which the redirected jets create a more homogeneous layer of polyacrylonitrile (PAN) fibers and reduce wasted material during the electrospinning process. Field deflectors are available for 5, 20, 30, or 37 needle linear emitters.
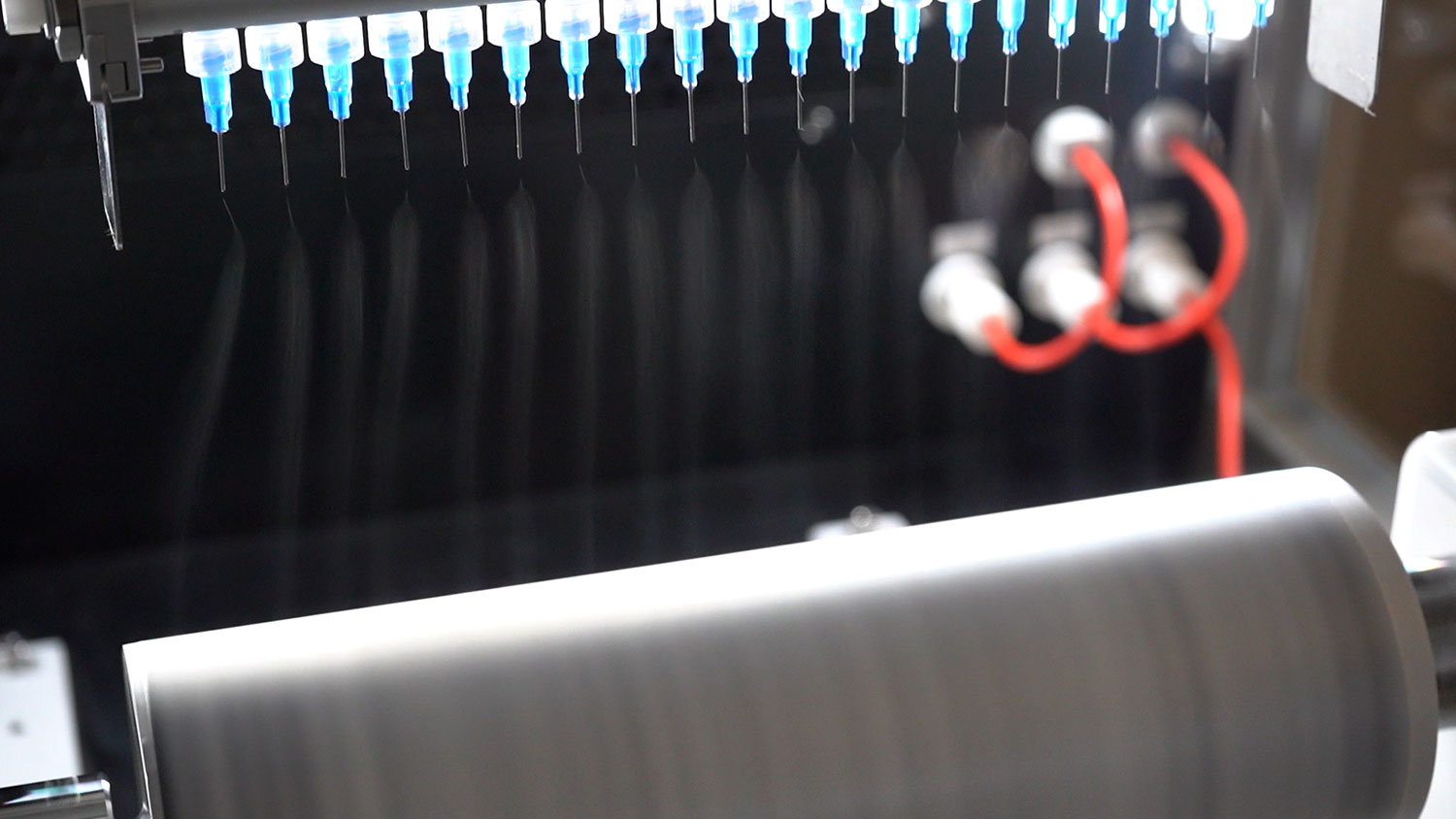
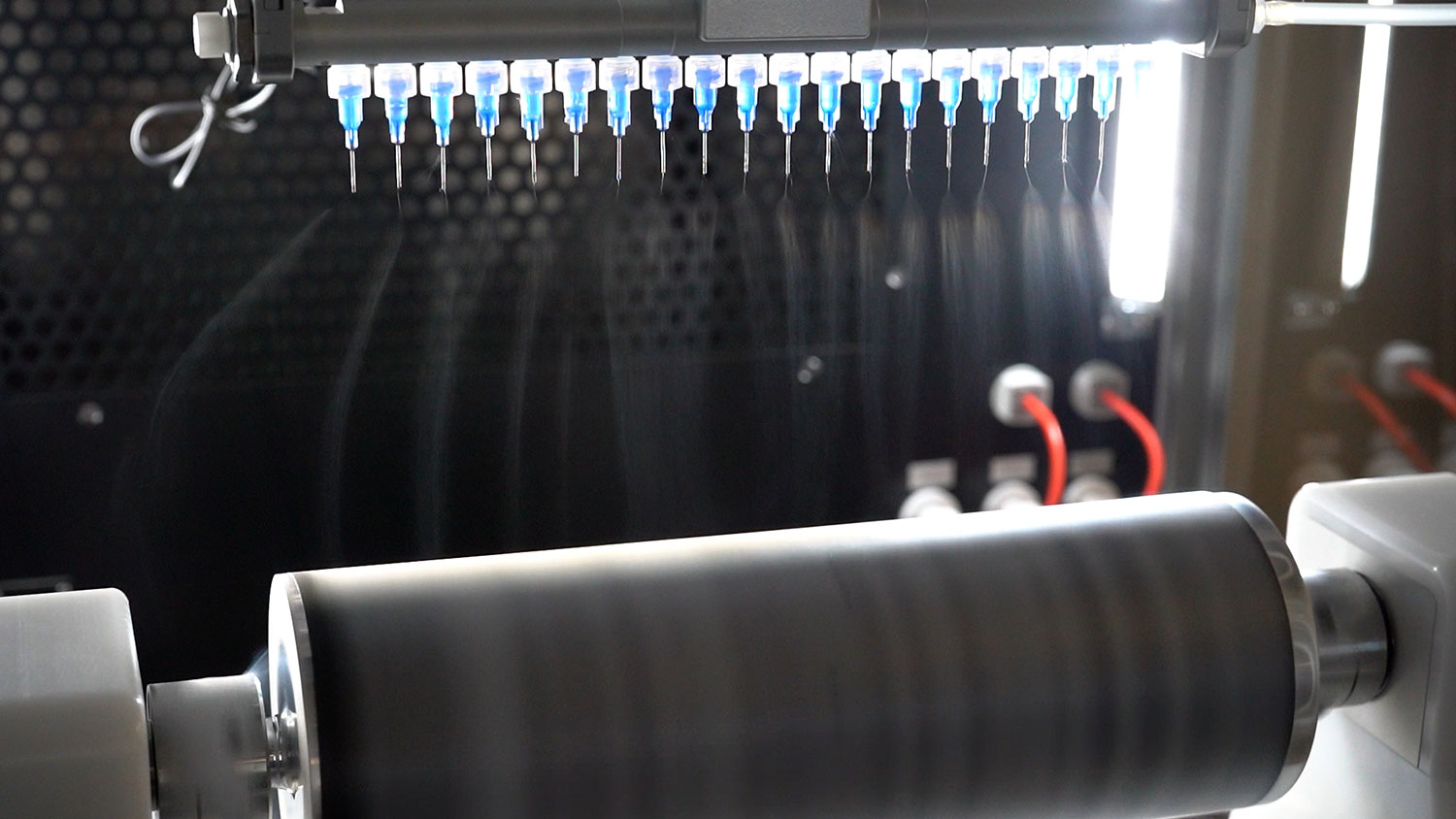
Effect of field deflectors on processes using linear multi-needle emitters (Left, field deflectors installed. Right, no field deflectors).
Electrospinning & Electrospraying
Multiaxial Electrospinning/Electrospraying Emitters
Multiaxial emitters enable the production of core-shell or core-sheath fibers or particles, fibers or particles with hollow cores, or Janus structures, which are fibers or particles containing two different materials side-by-side. Coaxial emitters are often configured with a small-diameter, blunt-tipped capillary needle inside a larger-diameter capillary needle, enabling one solution to envelop the other as the solution is ejected from the emitter during processing. It is also possible to flow gas through one of the needles. Gas-assisted electrospinning, electroblow-spinning, and blow spinning utilize compressed air or other inert gases to accelerate the jet of polymeric material towards the desired collector, the details of which are described below. These gas-assisted methods can be used strategically to increase throughput, change fiber morphology in the final sample, or deposit nanomaterials onto non-conductive substrates.

Single Nozzle Coaxial Electrospinning/Electrospraying Emitter
The single nozzle coaxial emitter enables research-scale production of complex fiber structures, including core-sheath fibers and particles, hollow fibers, or the encapsulation of additives on the core structure to protect them from harsh environments. With one coaxial nozzle, it is possible to process two different polymer solutions, flow gas through one of the inlets, or use pure solvent in the shell to minimize clogging when processing solutions that evaporate quickly. Depending on which inlet is connected to the gas flow, these configurations either result in the fabrication of hollow fibers, or gas-assisted electrospinning of solid fibers.
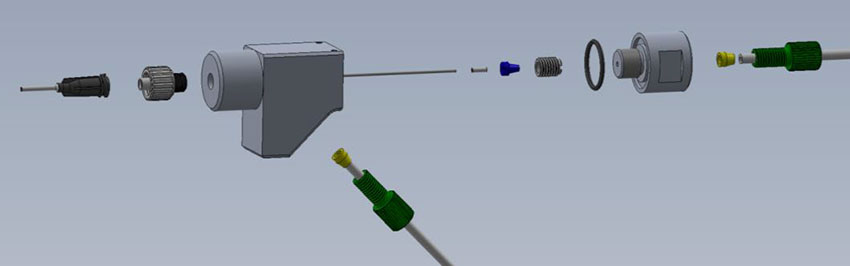
Triaxial Electrospinning/Electrospraying Emitter
The triaxial emitter system operates on the same premise as the coaxial emitter but includes an additional port to simultaneously feed a third material through the outer shell. Triaxial emitters are advantageous for the development of drug-loaded fibers or particles with different types of drugs through each layer, enabling fine tuning of long-term drug release systems. Materials with improved functionalities that cannot be developed with regular coaxial morphology can typically be processed using the triaxial emitter. Gas can also be employed with this emitter system, allowing processing while flowing air, nitrogen, or solvent vapors through the outer shell to prevent clogging or increase throughput when generating coaxial fibers or particles.
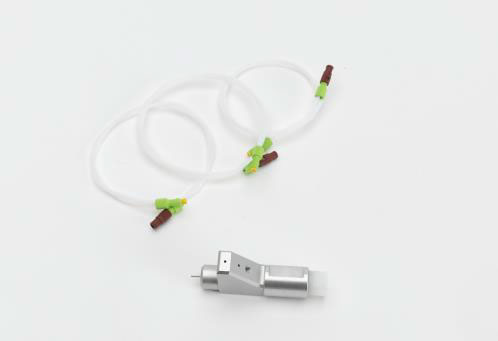
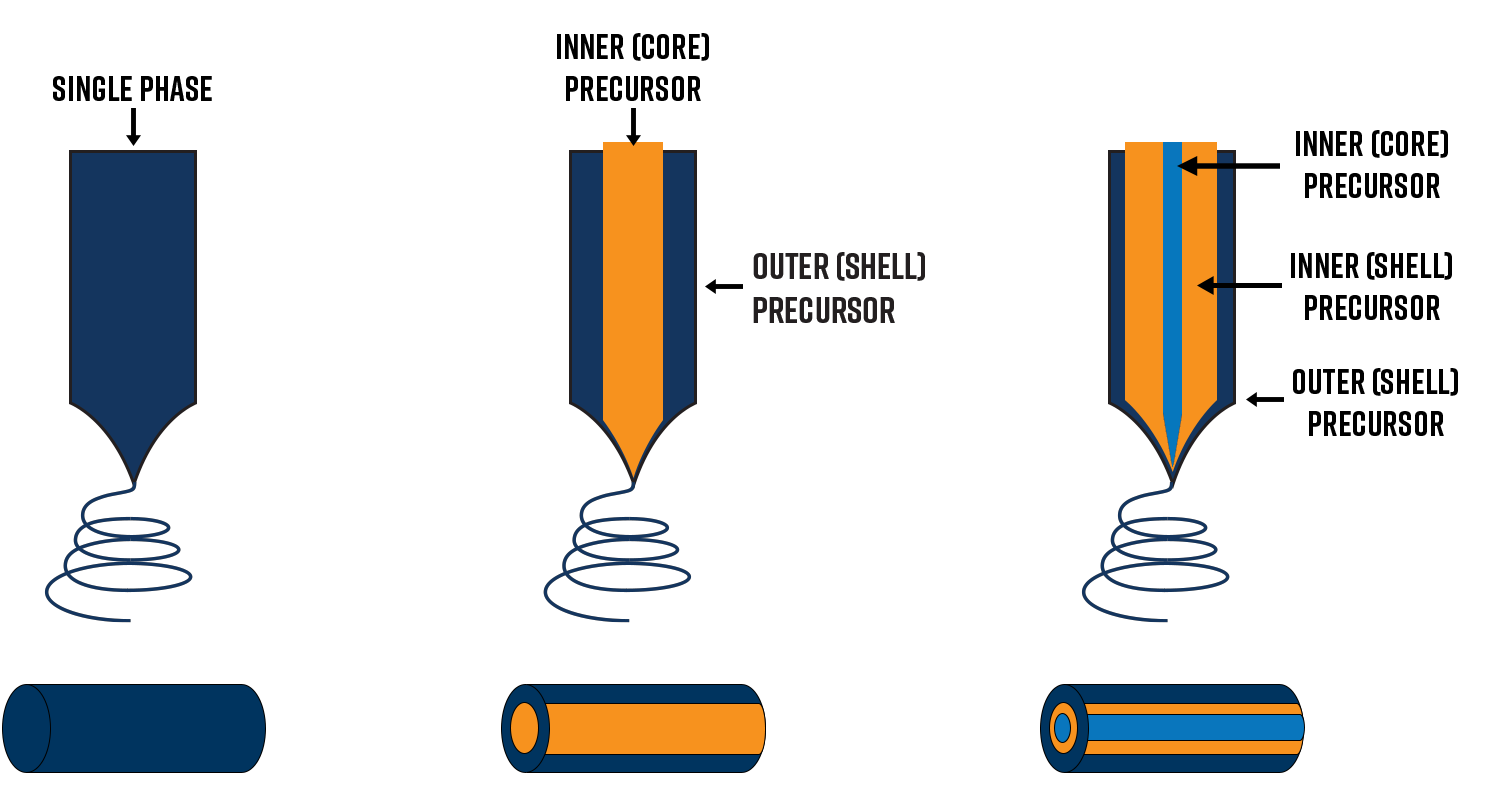
Solvent Gas Jacket Electrospinning/Electrospraying Emitter
The solvent gas-jacket emitter operates in a similar manner to the gas-assisted electrospinning emitter, but rather than using compressed air or an inert gas to accelerate the polymer jet, the solvent vapor surrounds the needle during sample fabrication. This is particularly useful for processing polymers that tend to clog the emitter needle, as it uses any desired solvent that can dissolve the main material to ensure the Taylor cone forms properly and the process continues without any clogging. The solvent gas-jacket apparatus works in tandem with the coaxial-style emitter and is therefore available in a single emitter and linear multi-emitters with 5, 20, or 28 nozzles, depending on the model of the machine in which it is installed. Field deflectors are also available for the 5-needle linear solvent gas-jacket emitters.
Gas-Assisted Electrospinning Emitter
Gas-assisted electrospinning, also referred to as electroblowing, electroblow-spinning, or gas jet electrospinning, is a process that enhances the traditional electrospinning process and increases throughput of nanofibrous material. In gas-assisted electrospinning, air (room conditions or heated) or an inert gas is blown through the larger capillary needle of a coaxial emitter nozzle to complement the electrostatic repulsive forces of the electrospinning jet and draw solution out of the needle at a higher rate. There are several reasons why gas-assisted electrospinning might be employed during processing, including increasing productivity and speed of fiber/particle deposition, along with many other practical benefits. Depending on the solution and processing parameters, gas-assisted electrospinning can increase throughput up to 20 times compared to traditional electrospinning or electrospraying. The gas-assisted emitter designed by Fluidnatek is available in a single-emitter configuration, as well as 5, 20, and 28 needle linear injectors.
Blow-Spinning Emitter
Blow-spinning is a technique that enhances fiber production and is useful for depositing nanofibers onto non-conductive substrates. However, it is not to be confused with “electroblow-spinning.” While these two terms sound similar, there is one fundamental difference. The blow-spinning emitter designed by Fluidnatek flows compressed air or an inert gas through the shell needle of a coaxial emitter nozzle to assist in accelerating the polymer solution towards the collector without applying voltage to the needle. Therefore, it is not an electrohydrodynamic process, but rather relies upon gas at a high flow rate to stretch the polymer jet towards the collector surface and dry out the fibers by quickly evaporating the solvent. Typically, blow-spinning produces fibers that are larger in diameter than those produced by electrospinning. One of the key advantages of the blow-spinning emitter is that it expands the list of possible substrates that can be used within the same Fluidnatek instrument.
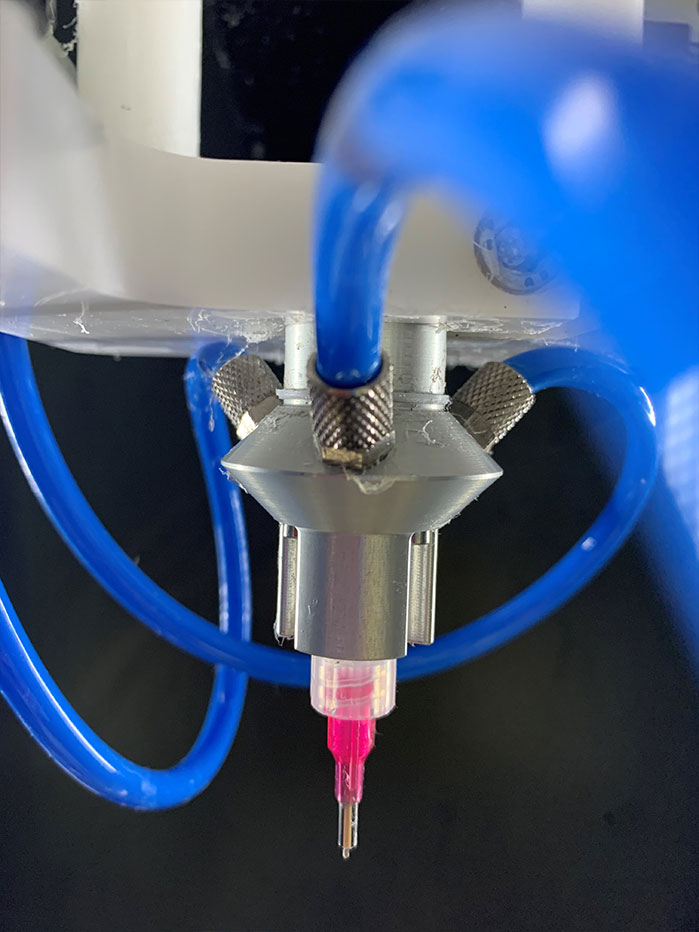
Coaxial Linear Multi-Needle Emitter System
The coaxial linear multi-needle system increases throughput during an electrospinning or electrospraying process. Fluidnatek’s proprietary multi-needle emitters are engineered to maintain equal pressure across every needle, minimizing clogged emitters and creating samples with better homogeneity. The system has been engineered to allow users to employ disposable needles on the shell and use reusable needles in the core of the system. Field deflectors can be implemented on the 5-needle linear coaxial multi-needle system to improve sample homogeneity while increasing sample throughput.
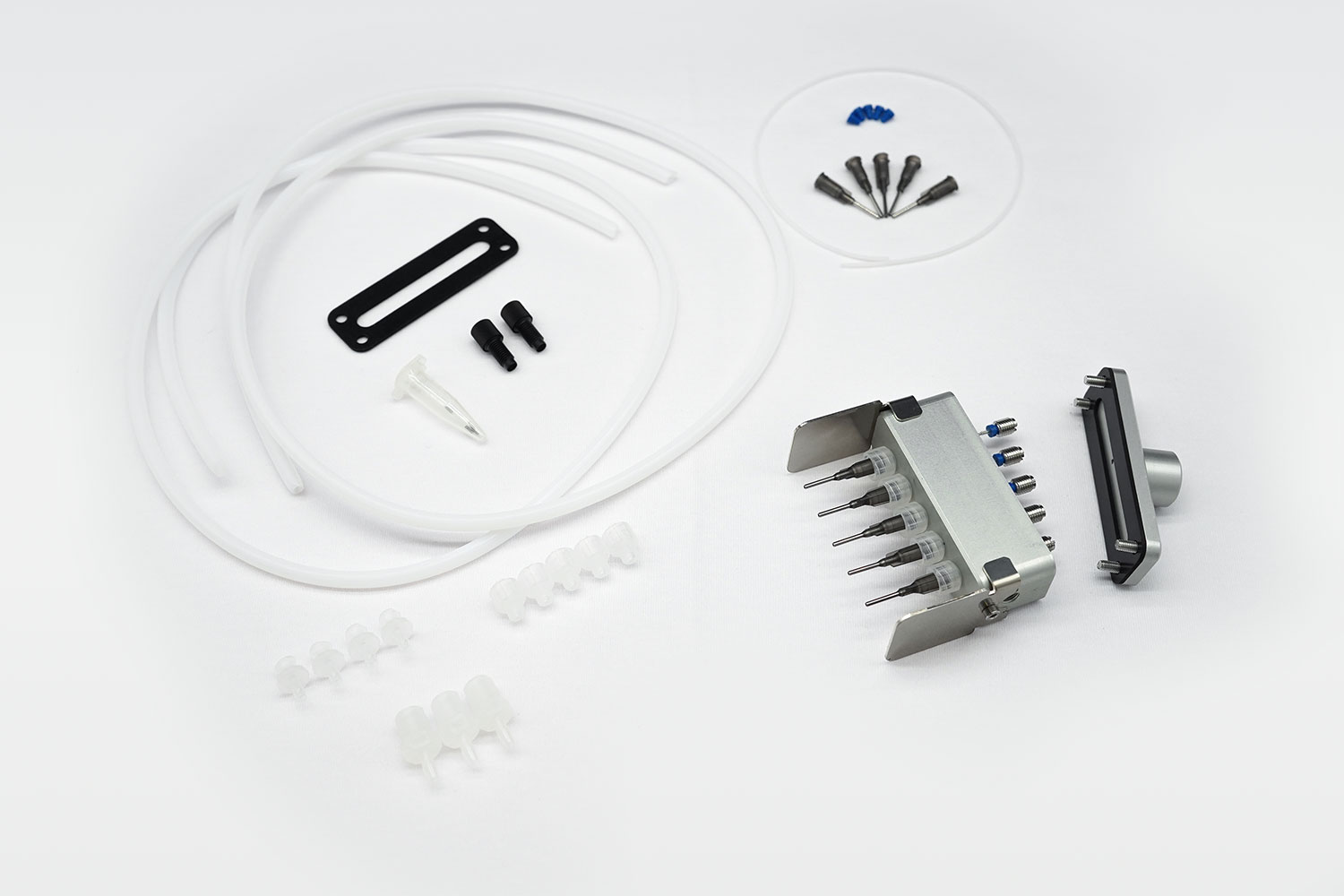
Coaxial linear emitters for Fluidnatek systems can be configured with 5 or 28 nozzles, and stacked to total up to 112 needles, depending on the equipment model in which the coaxial multi-needle linear injector will be used.
Electrospinning & Electrospraying
Needle-Less Electrospinning/Electrospraying Emitter
Needle-less Electrospinning/Electrospraying Emitter (Slit Injector)
The slit injector, Fluidnatek’s carefully engineered needle-less electrospinning emitter, is unique compared to other needle-less electrospinning platforms available for professional-grade equipment. Typically, needle-less electrospinning setups use open-surface techniques to produce nanofibers. However, this can produce unstable Taylor cones, which often leads to samples with poor homogeneity, abnormal fiber morphologies, and macroscopic defects in the final sample. Another disadvantage from open-surface techniques is that the solution is open to the atmosphere, causing the concentration to change over time, which negatively affects sample consistency. Unknown flow rates during processing are another disadvantage of open-surface processing.
Fluidnatek’s slit injector circumvents these process issues by feeding the polymer solution through a completely enclosed narrow slit, which creates stable, well-controlled Taylor cones and allows careful monitoring of the final overall flow rate during sample processing. The resulting nonwoven mats of electrospun material have good homogeneity and minimal to no defects, demonstrating that higher process throughput can be achieved using needle-less electrospinning processes without sacrificing the quality of the final sample.
Thanks to the enclosed system, solvents with low boiling points can be processed through needle-less electrospinning without blending with other solvents or including additives. The slit injector also allows the use of gas-assisted electrospinning with air (room temperature or heated) or inert gases like nitrogen if further increase of throughput is desired. It is also possible to combine needle-less emitters with needle-based emitters within the same Fluidnatek system, opening the possibilities for advanced sample manufacturing, creating multi-layered nanomaterials, or other complex R&D projects. The Fluidnatek slit injector is available in 10, 30, 40, and 50 cm lengths, and can be configured to operate with up to four simultaneous injectors, depending on the Fluidnatek system.
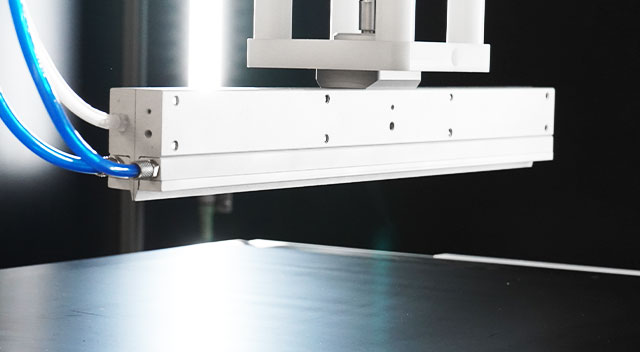
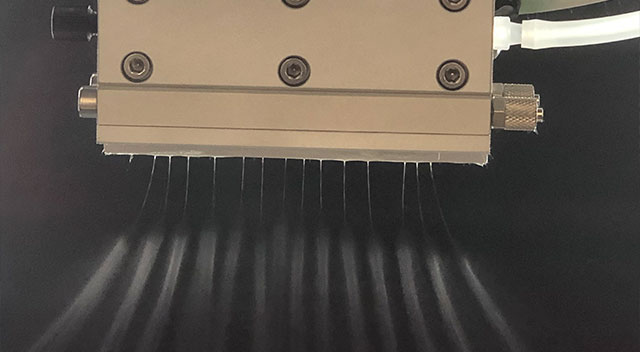
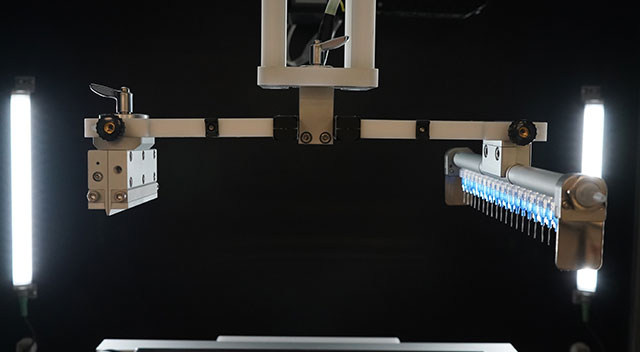
Electrospinning & Electrospraying
Product Knowledgebase
Webinar
Innovative Drug Delivery Systems for Wound Healing Using Electrospinning
Chronic wounds and wound infections are a major problem for the society and novel treatmen…
Blog
Fabricating Complex Geometries with Electrospinning
Electrospinning has emerged as a transformative technique for fabricating fibrous material…
White Paper
Controlling the Orientation of Electrospun Nanofibers for Tissue Engineering
Electrospinning is a versatile and promising technique for fabricating nanofibrous scaffol…