Electrospinning & Electrospraying System
Fluidnatek® LE-50 G2
The Fluidnatek LE-50 is a precise electrospinning and electrospraying system that allows researchers to produce nanofibers and particles with tightly controlled diameters and morphologies. It offers fully adjustable parameters including emitter and collector voltages, flow rate, automated needle translation, spinning distance, and more for optimized nanomaterial production.
Premier Processing
Advanced flexibility with simultaneous dual-solution processing & independent HV controls for both needle-based & needle-less technology
Exceptional Environmental Control
Ensures consistent and reproducible results every time with an ECU that provides precise heating, cooling, drying, and humidifying
Compact to Commercial Scale
Easily translate R&D processes on LE-50 benchtop unit to large-scale production processes with precise, sophisticated process control & sample quality
Talk to an Instrumentation Specialist Today!
Best-in-Class Benchtop Electrospinning and Electrospraying Machine
The Fluidnatek LE-50 G2 electrospinning unit is a professional benchtop system engineered for precision laboratory-scale research and development of nanoscale materials. Featuring a comprehensive control interface, researchers can adjust parameters such as voltage, flow rate, and spinning distance to tailor the characteristics of the produced nanofibers with exceptional accuracy. Its environmental control capabilities ensure consistent conditions within the processing chamber, optimizing reproducibility and experimental outcomes. With its user-friendly design and scalability options, the Fluidnatek LE-50 empowers researchers to explore various materials and applications, making it an ideal choice for cutting-edge nanomaterial research and development.
Application Areas:
Fluidnatek LE-50
Product Features
Full Environmental Control
The LE-50 works seamlessly with the Fluidnatek Environmental Control Unit (ECU) with capabilities to regulate temperature and relative humidity within the processing chamber. This ensures consistency and reproducibility of electrospinning experiments, especially when working with difficult solutions, sensitive materials, or in varying environmental conditions.
Global Process Monitoring
Comprehensive oversight of all critical parameters and stages throughout the electrospinning process is possible with the LE-50 data storage and/or High-definition Process Data Hub. This includes real-time monitoring of variables such as voltage, flow rate, temperature, humidity, and solution viscosity to ensure optimal conditions and reproducibility. By implementing advanced sensors and data acquisition systems, researchers can track these parameters globally, enabling precise control and adjustment to achieve desired nanofiber properties consistently. Additionally, integrated software may provide visualization tools and data analytics to analyze trends and optimize process parameters for enhanced efficiency and product quality.
User-friendly Interface
The Fluidnatek LE-50 includes a fully integrated touchscreen panel featuring a user-friendly interface with intuitive controls and software for easy operation. Researchers can set up experiments, adjust parameters, and monitor process parameters conveniently, reducing the learning curve and enhancing productivity.
Advanced Sample Development
Multiple configurable and automated electrospinning emitter stages with independent high voltages and solution supplies allow for dual spinning (co-spinning) of multiple solutions simultaneously for complex sample development. The LE-50 accommodates the production of fiber-fiber, fiber-particle, or particle-particle sample productions in various material combinations and form factors.
Versatility
The Fluidnatek LE-50 offers versatility in compatible materials, solvents, and 10+ electrospinning configurations. Researchers have the flexibility to experiment with various materials (polymers, ceramics, metallics, etc.), additives, emitters (needle, multi-needle, coaxial, needle-less), spinning orientations (vertical, angled, horizontal), and collectors (e.g. flat plate, drum, mandrel, water bath) to fabricate nanofibers and particles with different properties for numerous applications all in a single integrated electrospinning unit.
Scalability
While designed for laboratory-scale research, the Fluidnatek LE-50 offers a clear scalability pathway for potential transition to larger-scale production processes performed with the Fluidnatek LE-100 or LE-500. This scalability ensures seamless continuity and compatibility between lab-scale experiments and industrial-scale manufacturing.
Safety Features
Numerous safety features such as chamber door interlock, password-protected operator access, regulated airflow for solvent vapor removal, and emergency shutoff are integrated into the design of the Fluidnatek LE-50 to ensure operator safety during electrospinning operations.
Top-tier comprehensive US-based support and service for the LE-50 and accessories, including installation assistance, training, maintenance, and technical support are available to help users maximize the performance and reliability of the equipment.
Fluidnatek LE-50
Product Accessories
Environmental Control Unit or Dry Heating Unit
ECU provides tightly controlled temperature (18-45°C) and relative humidity (10-80%) with HEPA filtration, a necessity for ensuring reproducible and consistent electrospinning results. DHU provides an alternative environmental control for solution processing requiring low humidity (ambient RH down to 25% at 25ºC, or down to 10% at 45ºC) and/or increased temperature (RT up to 45ºC).
High Definition Process Data Hub
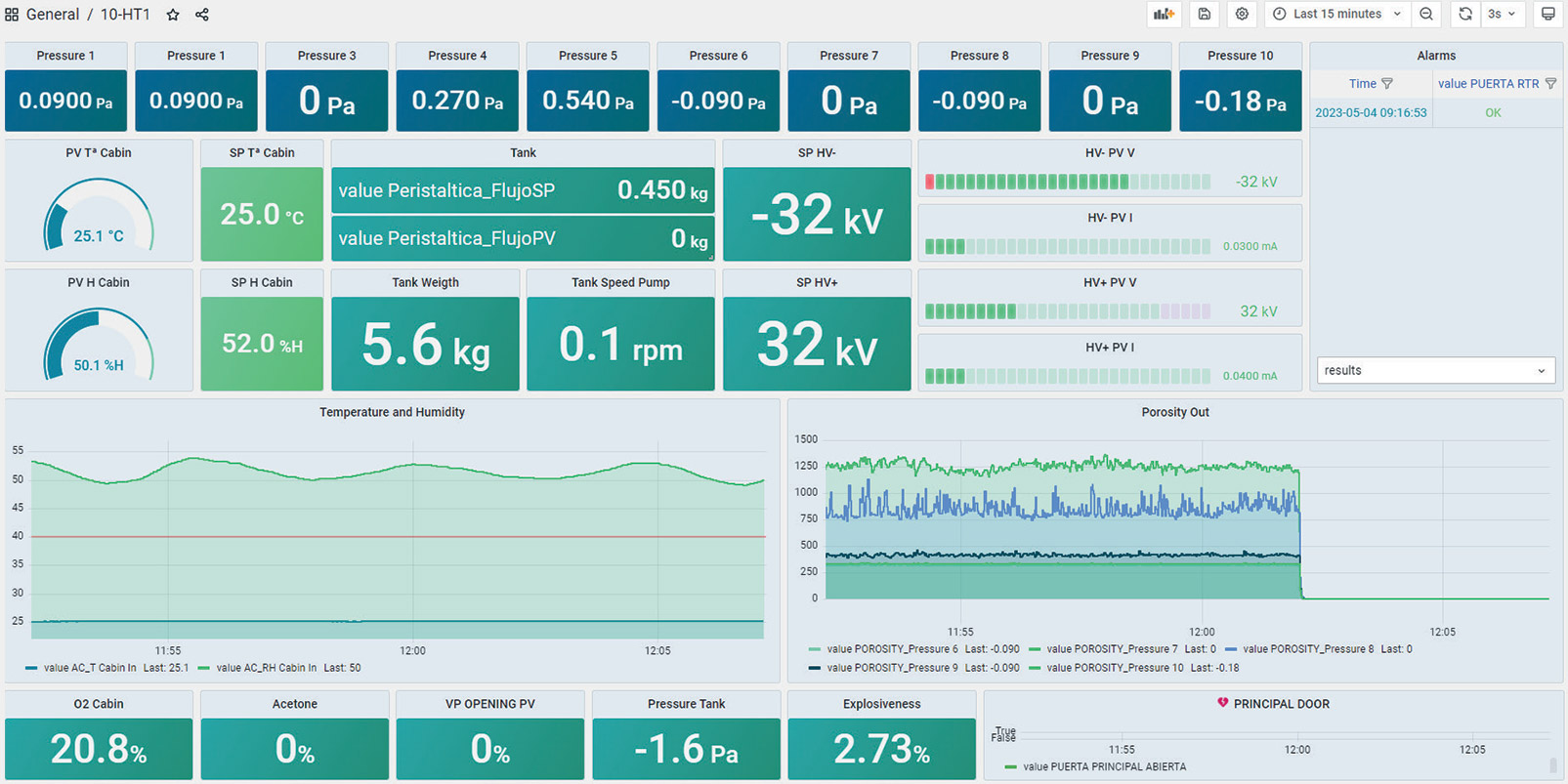
High Voltage Options
With multiple independent high voltages available in the unit, bias can be applied to additional emitters and/or collector. Additionally, the collector voltage can be upgraded to operate from 0 to -10 kV. Multiple adjustable voltages and a secondary stage in tandem provide configuration flexibility, such as co-spinning or dual spinning/spraying, emitter/collector voltage inversion for specific orientation, or preferential sample deposition/morphology.
Multiple Syringe Pumps
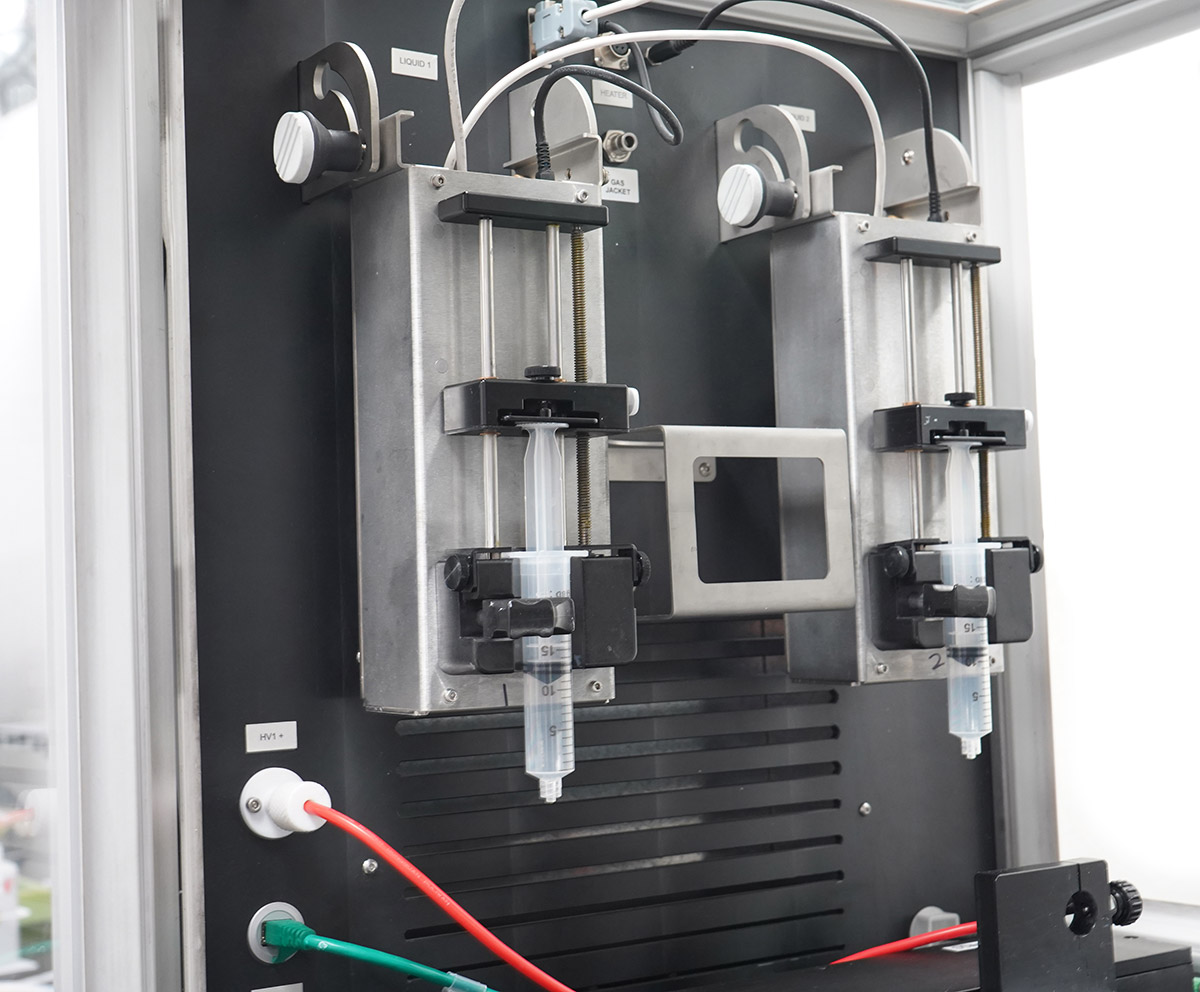
Needle Translation
The LE-50 equipped with improves sample homogeneity and thickness with needle translation. This helps produce more uniform fibers by distributing the electrospun solution more evenly across the collector, reducing fiber defects and ensuring consistent fiber diameter. Additionally, it enhances productivity by increasing the deposition area, allowing for the fabrication of larger, more uniform samples efficiently.
Adjustable Emitter Orientation
LE-50 compatible emitters can be positioned vertically and horizontally on independent spinning stages or angled (using an articulating flexible arm). Vertical orientation for top-down spinning or spraying onto collectors or water bath providing options for improved solution processing or particle collection. Horizontal and angled positioning prevent solution dripping onto collectors, easily allowing solution optimization or low viscosity solutions to be processed without defect to the final sample.
Taylor Cone Visualization System
The Taylor cone visualization system uses a high-quality camera to focus directly on the emitter needle tip for a close view of Taylor cone formation and solution processing. Taylor cone formation is indicative of the electrospinning quality and is therefore crucial for monitoring during process optimization. By observing the cone shape and stability in real-time, operators can quickly adjust parameters such as voltage or flow rate to ensure consistent fiber production and reduce defects. This leads to improved control over fiber diameter, morphology, and quality, resulting in a more efficient and reliable electrospinning process.
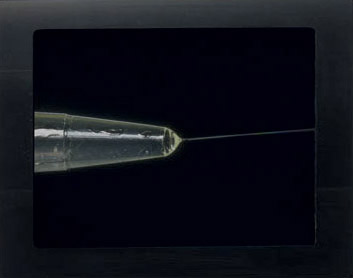
Emitter Variety
The LE-50 accommodates both needle-based (single phase, coaxial, triaxial, multi-needle, gas-assisted) and needle-less (slit injector) emitter forms all in a single electrospinning unit. This extensive array of emitters means and equally extensive array of fibers and particles morphologies are possible, including core-shell, core-shell-shell, hollow, textured, porous, and many more. Gas-assisted and solvent-gas jacket configurations provide assistance in spinning difficult or low boiling point solutions. Additionally, multi-needle and slit injector (needle-less) options can increase overall throughput and sample productivity.
Collector Variety
In addition to a standard flat plate configuration for randomly oriented fibers, the LE-50 can be equipped with a rotating drum, rotating mandrel, or rotating disk collector for various types of sample deposition. These collectors provide a controlled, dynamic surface for fiber deposition, leading to the production of aligned or oriented fibers, which can enhance mechanical properties such as tensile strength. Rotating collectors can improve uniformity and consistency in fiber distribution, and when paired with needle translation the continuous motion helps to avoid buildup in any one area, facilitating the production of non-woven mats with consistent thickness and density over larger areas for increased productivity.
Syringe Heating
Syringe heating can be implemented from 30°C to 120°C for processing of viscous or temperature-specific solutions. Controlled heating of solutions can enhance the flow and reduce viscosity, resulting in smoother and more consistent fiber production. This can be especially useful for polymers with high melting points or that are difficult to dissolve at room temperature. Syringe heating also improves process stability, quality, and efficiency, as it reduces clogging and maintains a steady flow rate throughout the electrospinning process.
Instrument Certifiability
The high-quality, professional nature of the Fluidnatek line provides the basis for GMP, GLP, GAMP, FDA, and/or ISO-13485 certifiable electrospinning machines. This certification enhances product reliability, consistency, and safety, making electrospun materials suitable for medical, pharmaceutical, and other regulated industries. It also builds trust with clients and stakeholders, demonstrating commitment to compliance and quality control, setting the machine apart from competitors and opening doors to broader market access and potential collaborations.
Fluidnatek LE-50
Electrospinning & Electrospraying Applications
Biomedical & Tissue Engineering
Electrospun nanofibers are used to create scaffolds for tissue engineering applications. These scaffolds mimic the extracellular matrix, providing a supportive environment for cell growth and tissue regeneration. They are prevalent in wound healing, bone regeneration, nerve regeneration, and more.
Medical Devices
Whether as coatings for prefabricated structures, active ingredient additives, or total device fabrication, medical devices implement electrospun nanofibers and particles for enhanced therapeutic effectiveness. These fibers and particles can allow for improved performance in mechanical properties, biological microenvironment control, cellular integration, and many more application-specific advantages.
Drug Delivery
Electrospun fibers and/or particles can be loaded with drugs or therapeutic agents and used as drug delivery systems. Precisely controlled electrospinning parameters allow the high surface area-to-volume ratio and tunable properties of nanomaterials providing controlled release of drugs, making them suitable for targeted and sustained drug delivery.
Functional & Bio Textiles
The enhanced performance of textiles by imparting properties such as water resistance, flame retardancy, and antimicrobial activity can be accomplished using electrospun materials. These fibers are used in lightweight protective clothing, wound dressings, and specialty textiles for various applications.
Filtration & Separation
Nanofibrous membranes produced by electrospinning are employed in filtration and separation processes due to their small pore size and high porosity. They are used in air filtration, water filtration, oil-water separation, and other environmental applications. This can be done using high-throughput electrospinning methods, such as needle-less electrospinning.
Batteries & Fuel Cells
Energy storage and conversion devices such as batteries, supercapacitors, and fuel cells utilize electrospun nanofibrous materials for improved performance of these devices due to their high surface area and electrical conductivity. Ease of particle incorporation, such as ceramic/inorganic nanoparticles, and homogeneity in electrospinning promotes the efficiency of the fibrous materials electroconductivity.
Cosmetics
Electrospun nanofibers can be used as carriers for active cosmetic ingredients such as vitamins, antioxidants, peptides, plant extracts, and more to provide targeted treatment for things like anti-aging, anti-scarring, UV protection, or moisturizing. These nanofibers provide a large surface area and controlled release properties, ensuring better penetration into the desired area and enhanced efficacy of the active ingredients.
Environmental Remediation
Electrospun nanofibrous materials are employed in environmental remediation applications such as wastewater treatment, oil spill cleanup, and air pollution control. They can effectively remove pollutants and contaminants from the environment due to their high surface area and adsorption capacity.
Food Packaging
Electrospinning in food packaging involves utilizing nanofibers and incorporated particles to create innovative packaging materials with enhanced barrier properties against oxygen, moisture, and microbes, extending the shelf life and freshness of food products. These nanofibrous packaging materials offer a sustainable and environmentally friendly alternative to traditional packaging materials, contributing to the reduction of food waste and environmental impact in the food industry.
Fluidnatek LE-50
Product Knowledgebase
Webinar
Innovative Drug Delivery Systems for Wound Healing Using Electrospinning
Chronic wounds and wound infections are a major problem for the society and novel treatmen…
Blog
Fabricating Complex Geometries with Electrospinning
Electrospinning has emerged as a transformative technique for fabricating fibrous material…
White Paper
Controlling the Orientation of Electrospun Nanofibers for Tissue Engineering
Electrospinning is a versatile and promising technique for fabricating nanofibrous scaffol…