Polymer compounding & shaping equipment
Polymer shaping systems
Micro compounders are widely used in research and development for small-scale polymer processing. To further process and shape extruded polymers, various polymer shaping systems are available, ensuring precise control over strand formation, cooling, and granulation. These systems are designed to handle the fragile nature of newly extruded polymer strands while preparing them for further analysis, secondary processing, or upscaling.
Talk to an Instrumentation Specialist Today!
Polymer shaping systems
The Xplore polymer shaping systems enhance the capabilities of micro compounders by improving material handling, ensuring consistent polymer morphology, and enabling scalable production processes. They can be used in combination with micro compounding instruments or as standalone tools.
Micro 3D Filament Line
Xplore’s 3D print filament line is designed to produce high-quality Fused Deposition Modeling (FDM) filaments with precision and efficiency. It integrates with the Xplore MC 15 HT or MC 40 micro compounder, creating a fully integrated 3D print filament screening system. This add-on provides a cost-effective solution for generating consistent, reliable filaments while minimizing waste and infrastructure costs.
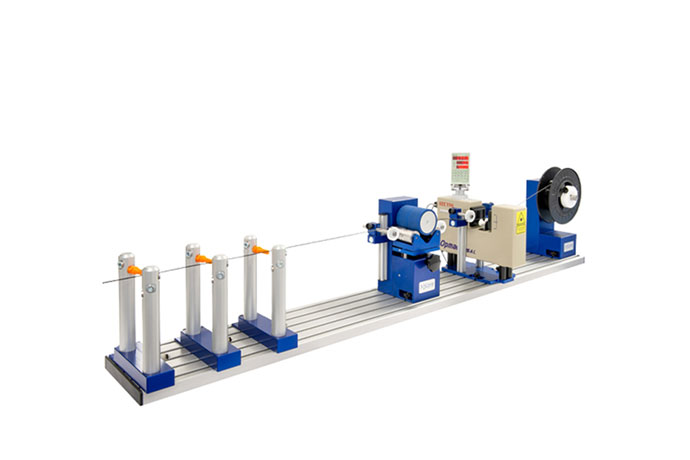
Key Features:
- High-Quality Filament Production – Ensures homogeneous, accurately dimensioned filaments free from voids.
- Broad Material Compatibility – Supports standard FDM materials such as PLA and ABS, as well as high-temperature engineering polymers like PC, PEEK, and PEI.
- Adjustable Line Speeds & Winding Capability – Offers a wide range of line speeds and the ability to wind filaments onto standard industrial bobbins.
- Precision Feeder (Optional) – Maintains consistent molten polymer throughput, ensuring uniform filament diameter and quality.
With its ability to accelerate R&D, optimize material usage, and enhance formulation testing, Xplore’s 3D print filament line is an indispensable tool for researchers developing next-generation 3D printing materials.
Microfiber Line
The Xplore Microfiber Line is engineered for the efficient production of fibers from minimal material quantities, requiring only 5 – 10 g of material and 10 – 15 minutes. This system significantly reduces material waste, accelerates development time, and lowers R&D costs while delivering high-quality, representative test fibers for research applications.
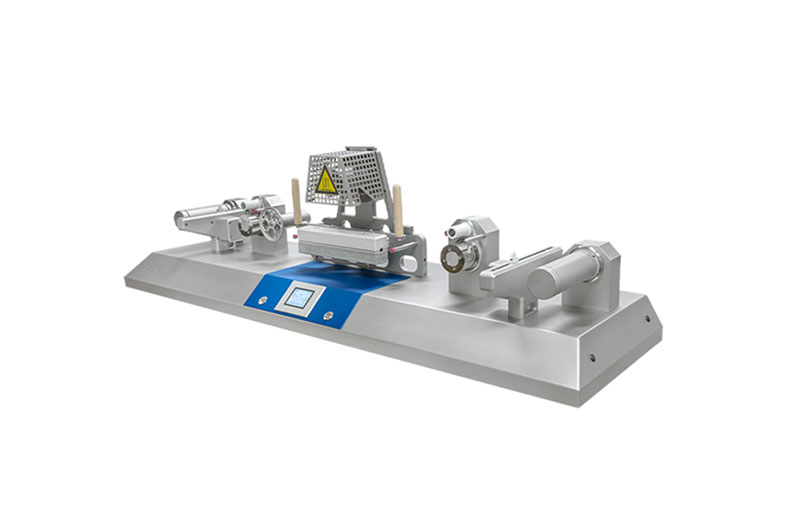
Key Features:
- Continuous Fiber Production – A continuous feed kit enables the generation of exceptionally long fiber samples without the need for an additional spinning pump.
- High-Speed & Low-Rate Conditioning – Features a high-speed winding unit (up to 200 m/min) and a low-rate conditioning unit to enhance fiber properties.
- Precise Stretching & Conditioning – Controls fiber drawing speed, ratio, and temperature, supporting both hot and cold stretching processes.
- Programmable Startup Sequence – A slow startup function prevents fiber breakage during stretching for improved process stability.
- Flexible Heating & Spool Compatibility – Accommodates various spool types and offers both radiative (hot shoe) and conductive (heated cylinder) heating options for optimal fiber processing.
- Optional Multifilament Die (MFD) for Advanced Spinning – Enhances multi-filament spinning with a vertical die outlet featuring twelve die openings. It can be integrated with a two-stage quench box, wetting unit, and melt strength measurement system for high-quality multifilament production.
By enabling rapid sample generation with minimal material usage, the Xplore Microfiber Line is a highly efficient solution for research and development in fiber innovation.
Micro Cast Film Line
Xplore’s Micro Cast Film Lines are designed for the efficient production of cast films using minimal material, making them ideal for applications involving limited material availability or high-cost polymers and additives. These systems are fully compatible with Xplore micro compounders, reducing screening costs and accelerating research workflows. By enabling the rapid production of representative films within minutes, they significantly streamline the material screening process while using only a fraction of the material required in conventional film production.
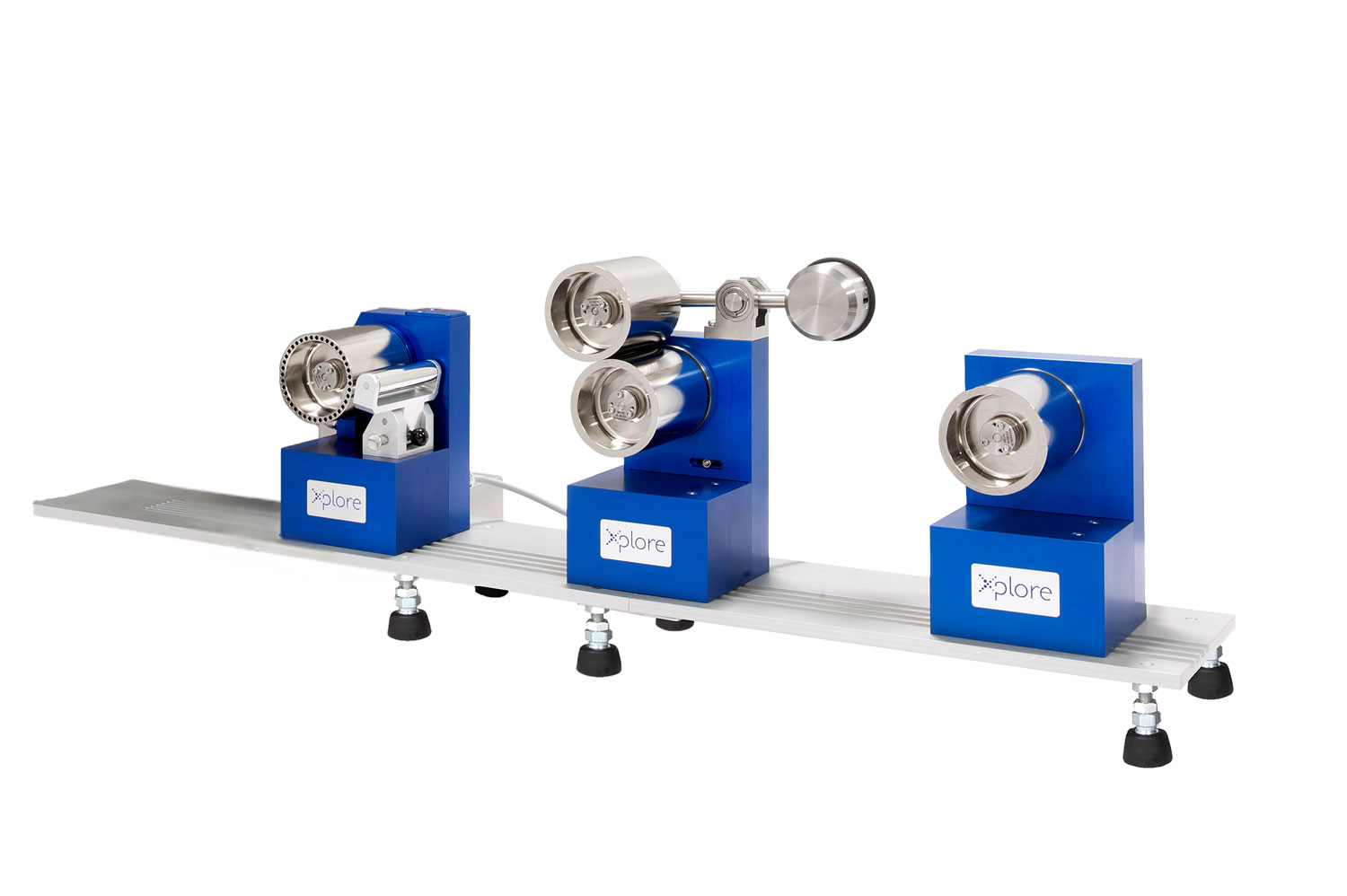
CFL 35 (Cast Film Line 35 mm)
When paired with Xplore Micro Compounders, the CFL 35 enables the production of reproducible cast films using just 5–10 grams of material within 5–10 minutes. This model is ideal for applications where material availability is limited, ensuring efficient screening with minimal waste.
CFL 65 (Cast Film Line 65 mm)
CFPL (Cast Film Pro Line)
The CFPL (Cast Film Pro Line) is Xplore’s most advanced micro cast film system, designed for precise process control in film formulation testing and optimization. It is particularly suited for films requiring specialized properties, such as optical clarity, mechanical strength, or barrier performance.
Key Features:
- Precise Film Drawing Control: Adjustable speed ranging from 100 to 5000 mm/min in 1 mm/min increments for optimal film processing.
- Torque-Controlled Winding System: A second collecting drum winder adapts to the increasing roll diameter during operation, ensuring consistent film uptake with precise 1 Nm tension adjustments.
- Uniform Film Quality: An air knife positioned immediately after the die prevents film necking, ensuring even thickness and quality.
- Continuous Feeding Kit: Enables automatic feeding in continuous extrusion mode for seamless operation.
- Optional Air-Cooled Take-Up Roll: The first take-up roll can be air-cooled to enhance film processing conditions and improve material handling.
These features make Xplore’s Micro Cast Film Lines an essential tool for researchers looking to efficiently produce high-quality cast films while minimizing material waste.
Xplore offers three Micro Cast Film Line models, each designed to produce high-quality cast films efficiently while minimizing material usage. These systems enable precise film formulation and process control, making them ideal for research and development applications.
Injection Molder (IM 12)
The Xplore IM 12 micro injection molder is a compact, precise, and versatile solution designed for seamless integration with Xplore twin-screw compounders. It can also function as a stand-alone unit by manually loading powders or granules. Engineered for flash-free operation, it ensures high-quality, shrinkage-free test samples through precise control of holding pressure and time. With a 12 ml shot volume, the IM 12 enables fast, reliable, and cost-effective testing of novel or expensive materials.
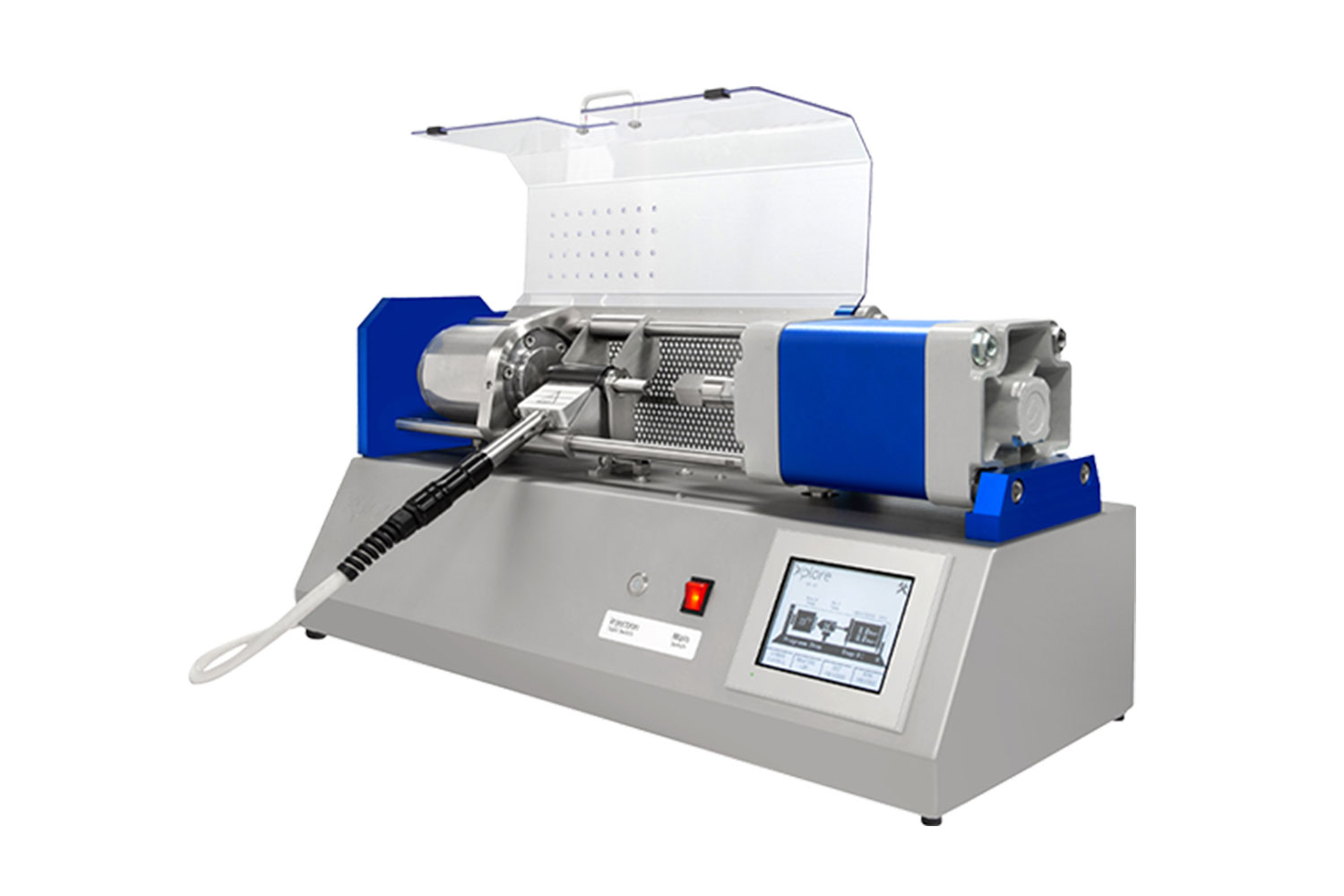
Key Features:
- Temperature-Controlled Mold Housing – Operating at mold temperatures reaching 300°C and an 18 kN injection force, it allows for precise molding of thin and elongated samples.
- Compressed-Air-Powered Plunger – Provides accurate injection with adjustable holding pressure for optimal sample quality.
- Multi-Cavity Mold Design – Enables the production of multiple test samples in a single cycle, improving efficiency.
- Standard and Custom Molds – Offers standard mold options, including dog bone-shaped tensile bars, Izod bars, and pharmaceutical tablet shapes, with customization available for specific applications.
Pro Pelletizer
The Xplore Pro Pelletizer is a post-die granulation unit engineered to cut polymer and rubber strands into a wide range of pellet sizes. It is fully compatible with all Xplore twin-screw compounders. The freshly cut pellets can be utilized for a second compounding step in one of the micro compounders or processed in a larger extruder for upscaling.
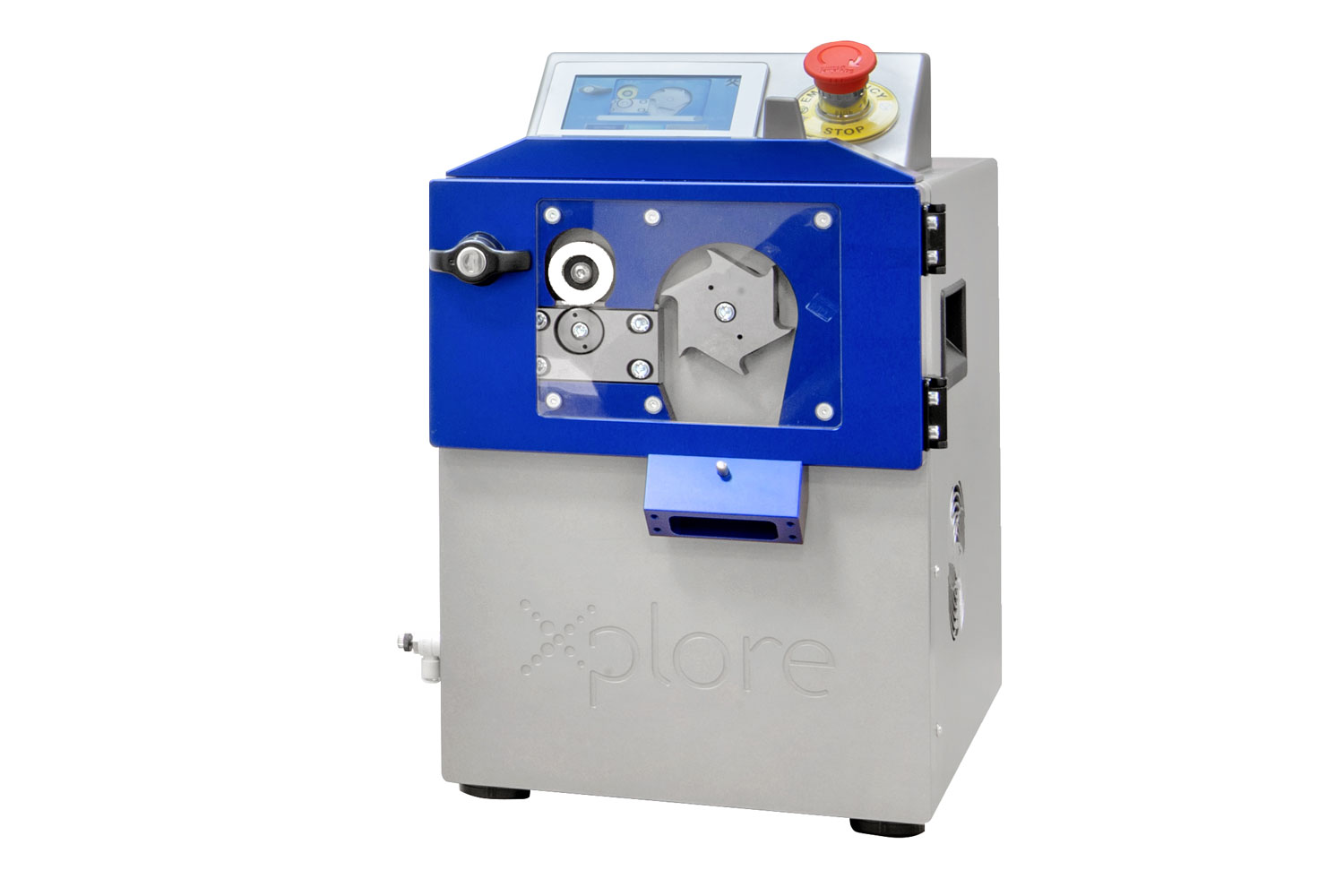
Key Features:
- Versatile Cutting Speeds: Equipped with two powerful servo motors, the Xplore Pro Pelletizer offers a broad range of cutting speeds, ensuring precise control over pellet length.
- Integrated Touchscreen Control: Allows users to adjust pelletizing speed with precision, enabling the production of pellets in various sizes.
- Easy Maintenance: A front-access opening panel facilitates quick and hassle-free cleaning.
- Optional Water Bath: Helps cool the polymer strand before pelletizing, ensuring the precise cutting of fragile, semi-solid polymer strands without protrusion issues.
Tow Impregnation Die (TID)
The Xplore Tow Impregnation Die is designed to impregnate multifilament fiber bundles with molten polymeric material. It utilizes spreader bars to separate the fiber bundle, ensuring uniform polymer penetration between individual filaments and preventing inconsistencies in the impregnation process.
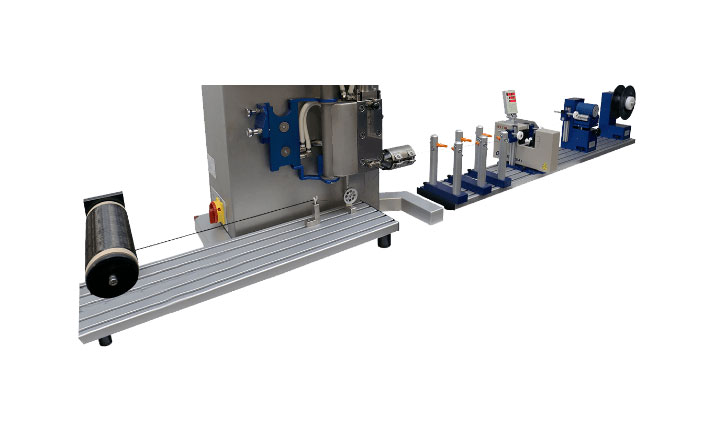
Key Features:
- Customizable Inner Sleeves: The coating die features interchangeable inner sleeves that can be tailored to specific diameters. This adaptability ensures precise polymer penetration in the fiber bundles, providing a broad range of processing capabilities.
- Integrated Pressure Control: A threaded hole is included for attaching a pressure transducer, enabling real-time pressure monitoring and adjustments. This ensures optimal impregnation performance and consistency throughout production.
Conveyor Belt Pro
The Xplore Conveyor Belt Pro (CB Pro) is designed to guide polymer strands directly from a micro compounder or small extruder. It is fully compatible with all Xplore micro compounder models, including the MC 5, MC 15 HT, and MC 40. The CB Pro features a non-stick PTFE conveyor belt, ensuring the controlled and consistent handling of fragile, nascent polymer strands. This prevents breakage or deformation while maintaining the polymer’s intended shape for further analysis or direct feeding into a small pelletizer.
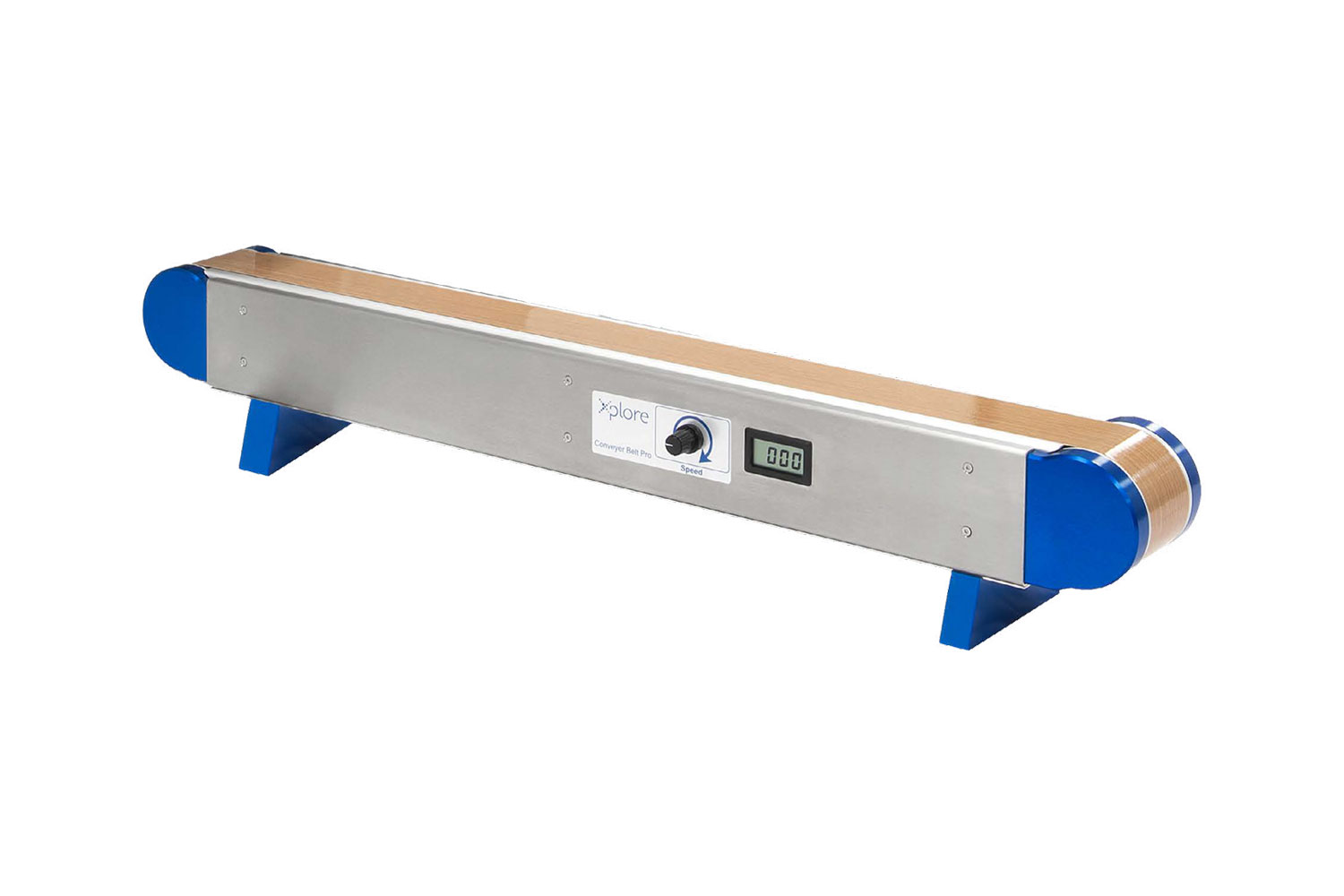
Key Features:
- Adjustable Belt Speed: Allows precise control, enabling customization for various processing requirements.
- Extended Operating Window: Supports prolonged draw rates as low as 1 m/min, ensuring accurate processing of delicate polymer strands.
- Versatile Retrofitting: Can be integrated into existing extrusion lines, making it an adaptable and efficient solution for research and development applications in polymer processing.