American Chemical Society: Fall 2024
Expo Hours
August 19-21, 2024:
Monday: 11pm – 5pm
Tuesday: 11pm – 5pm
Wednesday: 10pm – 2pm
Location
Booth #1719
Colorado Convention Center
700 14th St
Denver, CO 80202
Meet us in Booth #1719 at the American Chemical Society’s Fall Meeting!
In addition to showcasing our analytical services and instrumentation solutions for the fabrication and characterization of nanomaterials, we will be presenting two talks in the Division of Polymeric Materials Science and Engineering.
In the meantime, we invite you to explore our wide range of solutions and services for chemists, including:
Nanomaterial Fabrication Systems
- Fluidnatek Electrospinning/Electrospraying Equipment for fabricating nanofibers and nanoparticles from solution, suspension, or emulsion
- VSParticle Nanoparticle Generators and NanoPrinter for generating nanoparticles from any (semi-)conductive material and depositing nanostructured layers
Nanomaterial Characterization Tools
- Attension Theta Optical Tensiometers for side-on measurement of contact angles (static and dynamic), surface free energy (SFE), surface/interfacial tension with the pendant drop and reverse pendant drop methods, roughness-correction, interfacial dilatational rheology, and adhesion prediction
- Attension Sigma Force Tensiometers with robust, yet precise microbalances for measurements of surface tension, interfacial tension, liquid density, powder wettability, Critical Micelle Concentration (CMC), and sedimentation, among others
- QSense Quartz Crystal Microbalance with Dissipation monitoring (QCM-D) for real-time quantification of nanoscale interactions and reactions; offering label-free measurements of phenomenon such as attachment, removal, and conformational changes at surfaces
Process Development & Analytical Services
To learn more about the capabilities of our dedicated Analytical Laboratory, visit Nanoscience Analytical’s website
Presentations: (Held at Sheraton Downtown)
Nanoscale Porosity on Polymeric Sintered Electrospun Capsules for Long-Term Controlled Release | Aug. 20 | 5:15 – 5:40pm | Tower Court C
Speaker: Dr. Francisco J. Chaparro, Senior Product Manager – Electrospinning/Electrospraying
Drug delivery vehicles made through extrusion or film formation are frequently used to control drug release rates. While effectiveness can be limited based on drug size, incorporation of nanoscale porogens can improve release rates and prevent biphasic release. Incorporating salts into polymer solutions used for electrospinning offers an alternative approach to generate nanoscale porosity onto sintered electrospun capsules for controlled drug delivery. Electrospun polycaprolactone (PCL):polyethylene terephthalate (PET):HEPES salt (70:10:20, 80:10:10, 85:10:5 and 88:10:2) fibers were generated using a Fluidnatek LE-100 unit. Samples were electrospun onto 3 mm rods and sintered under vacuum at 100°C for 3 h to form dense specimens. After rod removal, salts were leached out in water and samples were then sealed with a model drug (rose bengal, RB) and oil carriers (hydrophobic and hydrophilic) to form closed capsules. Nanoscale pores were observed on electrospun and sintered capsules post-water treatment. Pore size and interconnectivity varied depending on HEPES content with more interconnectivity at higher initial salt loading. Water uptake over 49 days showed no weight increase when hydrophobic oil was used. Meanwhile, depending on the type of hydrophilic oil used, water uptake increased either 15% or 30% of the initial capsule weight. RB release from capsules following salt removal and using a hydrophilic oil as the carrier showed zero-order in vitro delivery over 10 days. Release rates were 6.87 ± 0.23, 10.56 ± 0.09, 33.81 ± 0.56 and 60.73 ± 1.34 μg day for 88:10:2, 85:10:5, 80:10:10 and 70:10:20 PCL:PET:HEPES, respectively. The inclusion of soluble salts in polymeric solutions is a promising approach for creating nanoscale porosity in electrospun fibers. Following densification and post-salt leaching, we can enhance the porosity and interconnectivity of the resulting capsules. These sintered vehicles have the potential to improve drug loading, as they can be tailored to different sizes and can use various carriers to enhance water uptake and drug delivery.
High Throughput Production of Electrospun Composite Nanofibers: From the Benchtop to the Converter | Aug. 21 | 5:00 – 5:15pm | Savoy Room
Speaker: Logan Gray, Material Scientist II
For decades, the development of nanofibrous materials has been critical for the fabrication and optimization of textiles, medical devices, aerospace, energy, and filtration technologies, as well as numerous other industries. Electrospinning is a technique that can be used to develop these nanofibrous materials with a high degree of reproducibility and control. Most known electrospinning systems operate at the benchtop scale and typically employ the use of a single emitter, limiting nanofiber production to low throughputs for research purposes. It is critical to develop strategies to increase nanofiber production beyond its current scale for manufacturing processes. One such strategy is increasing the number of emitters to significantly increase throughput in nanofiber production.
In this work, we produce and functionalize electrospun fibers at the pilot production scale with incorporated TiO2 particles for the formation of composite materials. In addition, post-processing of the fibers through a carbonization process results in the production of enhanced carbon nanofibers . Optimizations to the electrospinning process showed that the environmental conditions, namely relative humidity, played a crucial role in increasing the rate of nanofiber generation with throughputs as high as 160 mL/hr at the pilot production scale with a roll-to-roll configuration. These findings enable a viable manufacturing approach for continuously producing highly controllable and tunable nanofiber composite materials that serve numerous industries.
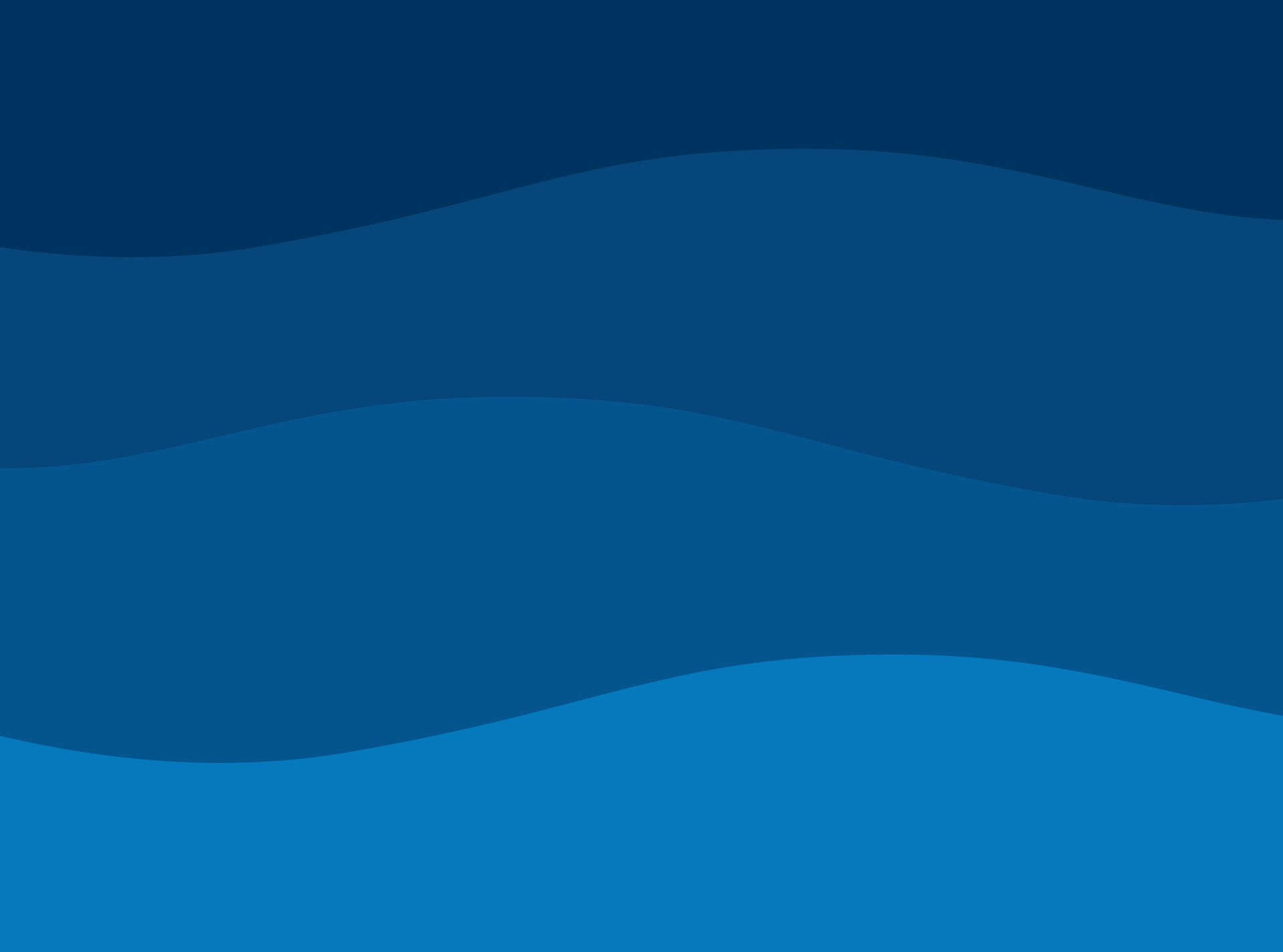